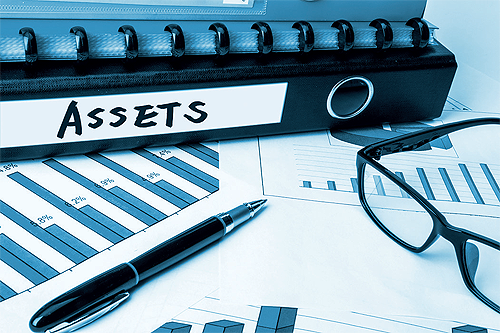
Peak performance
Automating asset failure prediction has become a key priority for manufacturers moving towards asset performance autonomy. Along with just about everything else, asset performance management (APM) is currently going through a period of major change and driving the adoption of APM solutions is a repositioning from site functional excellence to enterprise-wide performance management and customers’ desire for above-site management principles.
So, what does APM have to offer manufacturing organizations? Terry O’Hanlon at Reliability Web defines APM as: “A holistic approach and dynamically connected technologies to manage assets and the value they generate. APM matrixes at the business/managing system level to align asset management policy and strategic asset management plan to organizational objectives.”
This definition is spot on. That alignment delivers even greater value when there is enough warning from predictive maintenance to give manufacturers time to plan functions around downtime instead of just doing damage control. The overall value to the organization from APM increases dramatically when there is enough time for operations and supply chain action to mitigate downtime’s impact. With a longer prediction window comes a broader range of mitigation options.
In manufacturing, re-scheduling can avoid excessive transitions without missing orders. There is also the ability to use maintenance events as an opportunity to pull in maintenance items in order to reduce the turnaround scope.
APM software solutions use innovations such as predictive analytics and asset-related data to recommend a maintenance solution that will improve the reliability of the asset. They also enable end users in manufacturing to anticipate failure or life of an asset. More and more leaders in these sectors have come to understand that APM suites integrate operations, inventory management, risk, quality and finance to provide the highest business value.
The evolution of APM
The tools of the trade for APM are undergoing an enormous transformation as artificial intelligence (AI) and machine learning are serving as a force multiplier for asset experts, as well as enabling a new generation of workers to quickly become effective. APM providers are embedding AI and machine learning in their APM solutions in a manner that makes them essentially transparent to the user.
Technologies such as condition monitoring for equipment are being augmented with predictive process analytics that warn of overly aggressive operations that could degrade asset integrity and lead to unexpected downtime. Asset and process alarms are consolidated and being evaluated in terms of their relative impact to the balance sheet, and the risk to life and the environment. This keeps asset performance aligned with the manufacturing needs and priorities.
Another potential payoff for implementing risk mitigation technologies comes from institutional investors increasingly incorporating environmental, safety and governance issues into their investment decisions. Technology that works to eliminate the surprise of unplanned downtime enables companies to minimize the most dangerous plant conditions and reduce the amount of gases released into the atmosphere.
Responding to a rapidly changing environment
In the wake of Covid-19, manufacturers have been looking for ways to evaluate new business models and quickly align production with the new market realities. This global shift is driving a series of rapid changes to production slates and rates for companies around the world. These shifts are creating new safety and environmental risks that must be anticipated and managed, along with the obvious economic concerns. In production environments, change means increased risk.
At the same time, operating companies have been shouldering more of this risk, as insurance coverage is not as readily available, and even when it is, the cost of coverage has doubled in some cases. All of this is putting the methods that companies monitor and manage production processes under the spotlight.
APM has become an indispensable tool
APM may well play a role in determining the availability and cost of operations disruption insurance by protecting against unplanned downtime where most accidents happen and the greatest damage to the environment occurs. Many operating companies are running operations in new ways in response to Covid-19. That represents new risks to the equipment and its operators.
Companies need to quickly identify if any of those new operating conditions are degrading the asset and adjust accordingly. APM is undergoing a rapid transformation that will make it an indispensable tool to improve margins, safety and environmental compliance for asset intensive operations.
Robert Golightly
Robert Golightly is Senior Manager, Product at Aspen Technology (AspenTech) a global leader in asset optimization software. Its solutions address complex, industrial environments where it is critical to optimize the asset design, operation and maintenance lifecycle. AspenTech uniquely combines decades of process modelling expertise with artificial intelligence. Its purpose-built software platform automates knowledge work and builds sustainable competitive advantage by delivering high returns over the entire asset lifecycle. As a result, companies in capital-intensive industries can maximize uptime and push the limits of performance, running their assets safer, greener, longer and faster.
www.AspenTech.com