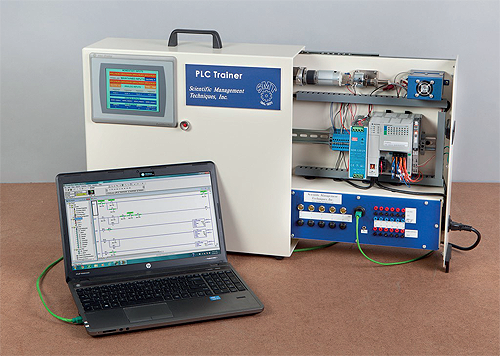
Global Skills Enhancement by SMT Across 47 Nations
Game changers
Scientific Management Techniques (SMT) was founded in Boston, MA, in 1970 by mechanical engineer Richard Whouley. Now Chairman Emeritus at the business, Richard’s first product was the Standard Timing Model mechanical skills assessment machine and program, and from this small beginning, the company has grown until today it has a large global footprint and operates in 47 countries.
“Fortune 500 manufacturers rely on SMT programs to drive performance and profitability by increasing the skill level of their workforce,” began company President Stephen Berry, when asked to give some details on SMT’s operations. “To sum up our solutions, we deliver hands-on, competency-based, manufacturing skills assessment programs and a full, hands-on, mechatronics skills training curriculum. We design and build the assessment machines and the training aids, and our programs are proven to be highly effective across a wide variety of manufacturing platforms and industries. Basically … we solve the manufacturing skills shortage/skills gap problems.”
The services supplied by SMT are delivered through two separate and distinct divisions – the Assessment Program and the Skills Training Program. Stated in the simplest terms, SMT’s Assessment programs ‘identify and measure the skills required to operate, maintain and troubleshoot a modern manufacturing facility’. Before getting into the specifics of the Divisions, Stephen posed an attention-grabbing question that he likes to ask plant managers: ‘How much more productive would you be today, if 50 per cent of your workforce were as effective as your top 20 per cent?
“That gets their attention!” he exclaimed. “This is because manufacturing leaders recognize that the top 20 per cent of their workforce is more effective/productive than the average performer. They live this reality every day. Our programs change this dynamic. With our skill solutions that top 20 per cent grows to 40 per cent – 80 per cent over time. Our programs are Powerful Productivity Tools.”
Skills Assessment Programs
“We achieve our results via five unique hands-on, competency-based assessment machines/programs – Mechanical Skill Assessments, Electrical Skill Assessments, Programmable Logic Control (PLC) Skill Assessments, Process Control Skill Assessments and Computer Numeric Control (CNC) Skill Assessments,” Stephen continued. These programs have four uses: “They are used in the hiring process; where they lower the risk and cost of hiring, they measure aptitude; to identify if unexperienced applicants have the potential to be trained, they measure skills gaps; to see what training might be needed in existing staff or new hires, and they can be used to measure the effectiveness of training delivered and help identify individuals that could or should be considered for advancement. This is valuable as our clients always want to promote the most highly skilled and the most efficient people. Using our assessment program in the hiring process assures that each new ‘skilled hire’ is a top performer and each ‘entry level hire’ is trainable.”
The solutions provided by SMT are clearly sophisticated and multifaceted, so Stephen used the Mechanical Skills Assessment Program, which uses the Standard Timing Model machine, as the exemplar of how the organization’s customers benefit from these programs.
“This machine identifies and measures mechanical skills, knowledge and ability. With most of the machines there are tests at different degrees of difficulty, so the particular test that you use is a function of the skillset that you are trying to identify and measure. With the Mechanical Assessment, there is a maintenance level test and there is a less challenging operator level test.”
The reason that the Maintenance level is more difficult is because within large manufacturing facilities, the maintenance team has the deepest mechanical trouble-shooting ability and the most knowledge of the equipment, the programs and the production line. “There is a very deep level of mechanical skill at the maintenance level,” Stephen confirmed, “so the Maintenance test is used to identify and measure the pre-existing skill set of a properly trained and experienced maintenance professional.
“The Operator level is a less difficult test on the same machine, and this has two uses. Number one is to identify and measure the pre-existing skill set of a proficient and knowledgeable operator – we know that when someone posts a strong score, that person will be one of the most efficient operators in the production facility. Number two is measuring mechanical aptitude, and aptitude translates directly to ‘trainability’,” asserted Stephen. “Individuals that possess mechanical aptitude are dramatically more trainable than those with little to zero aptitude. Our clients use this capability when they hire entry level staff that require training. This methodology significantly decreases turnover for entry level staff.
“The program also measures skills gaps, so how someone performs during the assessment gives you a very good understanding of what skills they do and don’t possess,” he added. “That is valuable information, because it enables you to deliver highly targeted skills training, and it means that you only have to take manpower out of production for the specific training that that individual requires, which increases the return on investment (ROI) of training dollars spent.”
All of the Assessments that Stephen speaks of are undertaken on a hands-on machine, and the applicants or operatives go through a test that generates a score from zero to 99 per cent. “If you are testing for mechanical aptitude then you are looking for any score at all, because if someone with literally no training or experience can intuitively figure out this machine and solve one or two problems and post a score of five or ten per cent, then they have proven that they have mechanical aptitude and trainability,” elaborated Stephen. “If you are looking for a pre-existing skill set, and you want to hire someone that is going to be effective right away, then you are looking for what we call a cut score of 50 per cent or higher.”
These scores are extremely important, especially in the hiring process, because SMT knows that when an individual posts a strong score, the applicant will be a top performer, and will be extremely productive. “Basically, they will be one of the top ten or 20 per cent of your workforce. The ROI of the assessment program is easily over 100 per cent the first pays for itself quickly. We have many clients that have been using the assessment program for decades.”
The effectiveness SMT’s assessment program had been validated by independent Industrial/Organizational PhDs 40 times. The program is proven to be Reliable, Valid and Defensible.
Skills Training Programs
Alongside the Assessment Division of SMT is its separate Skills Training curriculum, which is used to train the workforce to increase skill levels, performance and productivity. “Our hands-on skills training curriculum trains the specific skills required to optimize performance. It is highly customizable, so program users have the ability to deploy the specific Volumes/Units that are aligned with their training needs and objectives,” explained Stephen.
On the assessment side, the services provided by SMT are unique. “We are the only company in the world that has hands-on competency based manufacturing skill assessment machines and assessment programs,” agreed Stephen. But on the Training side, this isn’t the case as there are a lot of training programs out there. So, what makes SMT’s offering stand out from the competition? “That would be the curriculum, which has been developed over many years, and it is 100 per cent demand driven,” stated Stephen. “We work very closely with all our program users around the world in many, many different manufacturing industries, to ensure that we are training the specific skills that they require.”
SMT provides a Basic and an Advanced program, where a graduate of the Basic will be a highly effective operator, technician and entry level maintenance professional. A Graduate of the Advanced will be a highly effective maintenance professional.
In the same way that SMT’s assessments are very much hands-on, so too is the training program, which utilizes over 200 physical training aids that replicate real world conditions in manufacturing facilities. “We teach the theory and then we directly apply that in a hands-on lab setting and how that is split is vital, 30 per cent of the time is spent teaching the theory and 70 per cent of the time is hands-on training labs working with the training aids,” said Stephen. “Troubleshooting and problem solving are the focuses of the program, and the training aids are very dynamic – they don’t just sit there – they replicate production lines, they have moving parts, and are electric or hydraulically powered, they are very active and responsive.”
There are two deliverables for the training program: SMT delivers the training in its client’s facility with its own trainers, or SMT trains the client’s own staff to deliver the curriculum, and they own the program. “For the first model, we would ship in the training aids, and we would send in our trainers and deliver the training and we do this on a regular basis,” clarified Stephen. “Typically training deployment/placement is two weeks to six weeks, but for some companies we might go one week every month for a year, so with that component the time blocks are flexible.
“The second option, which is becoming much more popular these days, is when organizations buy the training curriculum and the physical training aids, and they license the curriculum, the students’ study guides and text books, and we train people on their staff to deliver the curriculum. That way they have got their own internal capabilities to deliver training whenever they need it. Realistically, the approach you choose comes down to costs and budget.
“Another unique aspect of our program, in addition to the demand driven curriculum, is that it is extremely effective in a short period of time,” continued Stephen. “That is important because when you are delivering training in these large facilities, you are taking manpower out of production to increase their skills but you want to get them back into production, with deeper skills sets, as quickly as possible for the obvious reasons.”
As Stephen had emphasized, the training curriculum supplied by SMT has been vetted and deployed by Fortune 500 manufacturers, which goes a long way to illustrate its pedigree and standing in the market. Adding to this reassurance is the fact that it has been reviewed by the American Council on Education (ACE) – the largest accreditation body of curriculum in the United States. This gives the program official recognition for its quality.
“The training program has been vetted and deployed globally by Fortune 500 manufacturers across a wide variety of manufacturing platforms and industries. The curriculum has also been reviewed by the American Council on Education (ACE) for college credit, ACE recommends 21 college credits for successful completion of our curriculum.”
Having mentioned the vast amount of data that SMT has at its disposal, Stephen disclosed some further fascinating insights that have been revealed from the millions of assessment scores that the business has on file, dating back to 1971.
“We probably have more data regarding the skill levels of the manufacturing workforce than any organization in the world,” he revealed. “When we put the scores into a chart, it shows that the average mechanical skills score was relatively stable from the early 1970s to the mid 1990s, with a few ups and downs. Then in the mid 1990s scores started to decline, and today there is a rather acute global shortage in the skills required to operate, maintain and troubleshoot a manufacturing facility, and that is now a big deal.
“For many years manufacturers hoped that local schools would deliver the skills training that they need, but that did not happen, so they have now taken it upon themselves to solve the problem, and that is where we come in with the deployment of our curriculum.”
Stephen believes there is a combination of factors that have come together to create this issue. “I have this conversation on a regular basis with manufacturers around the world, and although we operate in 47 countries, our deepest experience is in the States, and I find that here, in the US, one of the things that happened in the mid 90s, was that high schools started to do away with shop classes – woodshop, metalshop, autoshop – so children in High School weren’t learning these skills.
“Then we had the advent of the internet, so young people were moving onto the computer. Finally, society started to convey to the younger generation that if you want to be successful in life, you really have to have to go college for four years and get a degree, rather than going to a trade school. The thought of working in an industrial setting became less and less attractive in society’s eyes, and unless you are in some way attached to the manufacturing world via a friend or family member, the assumption is that working in a factory is your grandfather’s job, and is dirty and smelly. The reality is exactly the opposite of course, these are great jobs, in high tech facilities and pristine working environments But if you are not attached to this world you are unaware of it.”
The data that SMT is able to analyze means that its solutions can assist manufacturers in finding the right caliber of employee, but this is not a static process and its solutions need to evolve with the market, which in some cases is fast-moving and features a lot of state-of-the-art technology. “Not a year goes by that we don’t improve components of the curriculum and add new curriculum, so the program is dynamic and we consider it an ongoing needs-analysis of the skills required to optimize performance in industry,” shared Stephen. “We work closely with our global client base to ensure the curriculum is aligned with technology upgrades in the production environment.”
As we enter 2021, the manufacturing sector is facing a skills gap that is significantly impacting the bottom line of facilities all over the world. While governments and educational establishments may look for answers, what industry needs right now is an immediate solution with an impeccable pedigree that can provide an instant impact – and increasing numbers of blue-chip organizations are turning to SMT for exactly that. “Our Assessment program is a real game changer,” emphasized Stephen. “When organizations deploy the program, they recognize immediately how effective it is, because they have the ability to compare the first person hired through the assessment program to everyone that they have hired in the past. Our solutions are simple, but they are quickly identified as extremely powerful tools, which improve performance and productivity by increasing the skill levels of the workforce.”
He concluded with a very interesting fact, which adds even further evidence to the success and benefits of SMT’s approach. “On the Assessment side, there is a money back success guarantee,” he said. “If after deployment any program users feel that the program is not effective, we will buy it back from them. We have been in business since 1971 and nobody has ever taken us up on that offer, not in 50 years!”
Scientific Management Techniques
Services: Vendor of uniquely effective manufacturing skills solutions
www.scientific-management.com