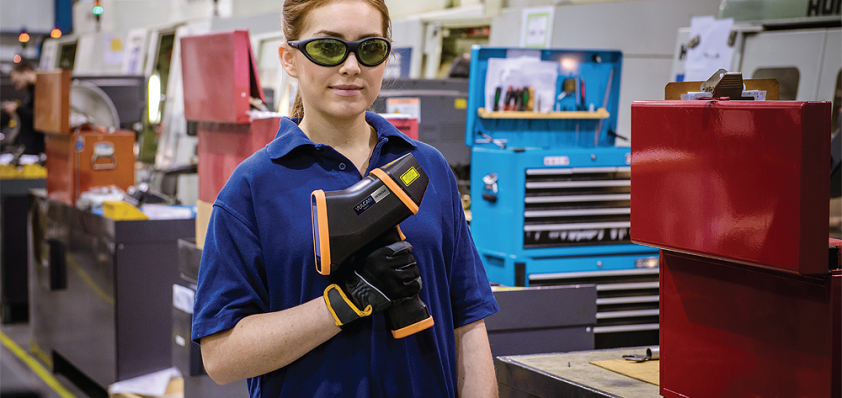
A material world
Tough legislation on carbon emissions is forcing manufacturers to innovate across the automotive supply chain. Earlier this year, the US Environmental Protection Agency followed the international example by announcing its developing new rules to decrease pollutants in vehicle emissions. Similarly, China 6a emissions regulations are set to come into force this year, with the EU’s next phase of Euro 6 standards coming into effect in 2021.
As global legislation becomes increasingly stringent, innovations in materials, vehicle design and propulsion systems are bringing fresh challenges. Light-weighting is a key strategy to meet this next generation of emissions targets. Further, as CO2 emissions fall by 8.5g per 100km for each 100kg lost, cutting weight remains a priority for manufacturers striving to get more from every drop of fuel or battery charge. Moreover, the emerging generation of electric and connected vehicles contain a myriad of complex components and require new material specifications, too.
This evolution is bringing crucial analysis and quality control requirements across the supply chain – from foundries, fabricators and metal component producers to electronics suppliers and recycling facilities. Here we consider the trends and technologies enabling the automotive supply chain to succeed in a time of rapid change.
The road to light-weighting
Two of the key metals facilitating vehicle weight reduction are aluminum and magnesium. Aluminum weighs about a third of steel, while magnesium is the lightest structural metal – 75 per cent lighter than steel and 33 per cent lighter than aluminum – and is abundant and easily recyclable too. BMW recently used aluminum to more than halve the weight of the 5-Series tailgate; and Opel (part of PSA group, Europe’s second biggest car maker) used magnesium to replace steel in the Vectra’s dashboard support, shaving 5kg in weight.
By 2022, the average car is expected to contain around 100 kg of aluminum as a replacement for steel and other materials, and the global market for magnesium and aluminum-alloy automotive components is predicted to be c.$48 billion by next year, growing at a c.7 per cent CAGR.
Consequently, in a bid to regain market share, steel makers are developing super-lightweight steels that are stronger, cheaper and (almost) as lightweight as aluminum. These are expected to reach the market in 2021.
To meet automotive manufacturing requirements, a range of carefully controlled alloys are required to provide the properties needed for vehicle components. By itself, aluminum can be relatively weak. And, while the introduction of lithium significantly increases its tensile strength, Al-Li alloys can be brittle and subject to deformation and fracture. The machinability of an Al-Li alloy can be improved with the addition of phosphorous and sulphur, but this needs to be strictly controlled as both have a detrimental effect on corrosion resistance. Similarly, magnesium is also brittle, with the addition of rare earth elements (REEs) – such as dysprosium, praseodymium and ytterbium – needed to improve this.
Adapting to the EV evolution
The electrification of vehicles is also disrupting the supply chain for the automotive industry, and poses a significant, imminent threat to the forging and metal casting sectors in particular. The average powertrain in an internal combustion engine (ICE) has about 107 forged parts and around $550 worth of metal castings, but an electric vehicle such as a Tesla typically has fewer than ten forged components and about $200 of cast parts, and those are mostly die castings.
Several factors are coalescing to make, inevitable, the looming fleet change to EVs (electric vehicles), including global environmental concerns and legislation, and the subsequent decision by the world’s largest auto market, China, that all its cars will be EVs. Companies such as Volkswagen and GM have announced they are not conducting further research and development into ICEs, in part to avoid hefty EU penalties for non-compliance of €30,000 per vehicle per day.
The push to improve vehicle range is also driving the global pace of change towards vehicle light-weighting. Every part of a vehicle is undergoing intense scrutiny for possible redesign and all materials are likely to be new and improved in the new generation of EVs heading for our roads. While the predicted transition in the US is slower than in countries such as China, manufacturers across the whole automotive supply chain are being forced to rethink their business models, with a renewed focus on developing innovative processes and materials in order to weather the approaching storm. Although the US Energy Information Administration (EIA) estimates that EVs will represent only five per cent of cars/light trucks and 0.5 per cent of freight trucks on US roads by 2033, savvy businesses should be gearing up now for the inevitable change – as the old adage goes, a stitch in time saves nine.
As foundries, metal casters and other manufacturers adapt, this will likely see them work more rigorously to produce the highest quality parts at the most affordable prices. Achieving this goal naturally presents new material analysis challenges that will need to be dealt with too.
Analysis technology developments
In five years, it’s likely that vehicles will use a larger range of materials than ever before, and the need to ensure the use of the right material for the right component will be paramount. As vehicle designs evolve and new materials are developed, technologies are evolving to provide effective materials analysis and enable manufacturers at every stage of the supply chain to improve quality control for incoming materials and outgoing parts.
There’s a growing trend towards 100 per cent PMI (positive material identification) too and more companies are investing in tools to improve quality control processes in the pursuit of 100 per cent quality. In the case of raw materials and metal components, we are seeing that companies are relying less on supplier certificates and investing more on analyzers. Given the critical and increasing role of electronics in demanding markets like automotive as well, reliability and accuracy in production and quality control are paramount for safety, with many switching their analysis in-house.
The quality of new alloys being developed stems from manufacturers having the right tools. From making sure the right material is used to controlling the metal melt, it is crucial for organizations to invest in analyzers that provide results fast and accurately for decision making. This includes providing teams with handheld laser induced breakdown spectroscopy (LIBS), X-ray fluorescence (XRF) or optical emission spectroscopy (OES) analyzers for materials analysis and quality checking to verify material grades.
For analysis of alloys to the ppm level, OES technology gives the most precise results, covering the complete spectrum of elements in metal, including phosphorous, sulphur and boron, which can’t be measured at all or with the necessary detection limits with either a handheld LIBS or XRF analyzer. The new generation of OES analyzers are designed for fast, reliable and cost-effective melt and raw material analysis. They allow analysis of all main alloying elements and identification of exceptionally low levels of tramp, trace and treatment elements in metals.
Conclusion
The pace of industry innovation brings crucial quality control challenges across the automotive supply chain and, in response, the field of materials analysis has been rapidly changing. The continued development and application of technologies like OES, XRF and LIBS is making analysis easier, with huge potential to unlock commercial value. Choosing the right technologies for every stage of the automotive development process is critical to ensure analysis keeps up with industry innovation and changing regulatory demands. Continued innovation and development of analysis technology is vital to help the automotive industry meet its current and future challenges.
Mikko Järvikivi
Mikko Järvikivi is the Head of Global Product Management at Hitachi High-Tech Analytical Science. For over 45 years, Hitachi High-Tech Analytical Science has specialized in high-tech analysis solutions designed to meet the tough challenges of a rapidly evolving industrial sector. Today, it is helping thousands of businesses streamline their costs, minimize risk and increase production efficiency. Its range of laboratory-based and robust high-performance in-field testing instruments deliver materials and coatings analysis that adds value throughout the production lifecycle, from raw material exploration to incoming inspection, production and quality control to recycling.
https://hha.hitachi-hightech.com/en/