
Aalberts: Advancing Metal Tech & Sustainability
Specializing in processes that improve the characteristics of metal parts, Aalberts Surface Technologies (Aalberts) provides heat treatments, surface treatments, brazing, and hot isostatic pressing (HIP) to regional and global customers. Aalberts is also a leading manufacturer of ferritic nitrocarburized steel bars known as NitroSteel®. The company’s NitroSteel® products are an environmentally friendly alternative to traditional chrome-plated bars, providing superior durability and increased corrosion resistance. Through its expertise and innovative business model, Aalberts plays a vital role in the production of high-quality, long-lasting components for industries that demand exceptional performance and longevity. Steve Wyatt, President of Aalberts Surface Technologies in North America, shares a brief introduction to Aalberts.
“Aalberts N.V. is a Dutch technology company headquartered in Utrecht, Netherlands. Aalberts Surface Technologies is one of several technology clusters within
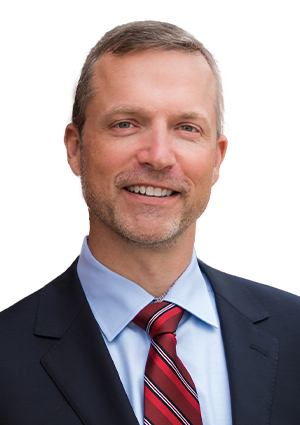
Aalberts N.V., with locations in North America, Europe, and Asia. Aalberts Surface Technologies HIP/braze/heat treatment is based in the US and consists of several businesses that were established as early as the 1970s and acquired by Aalberts over the last two decades. These businesses include Accurate Brazing, Applied Process, Ionic Technologies, and Premier Thermal; over the past year, we have rebranded these businesses, retiring the legacy names in favor of a single brand. As a result, we have become a large, specialized heat treatment, brazing, and HIP organization, primarily located in the eastern half of the US, with 18 plants spread across 17 sites and a dedicated workforce of nearly 500 employees. Globally, we are the second-largest heat treating company,” he enlightens.
Aalberts’ unique business model and multiple specializations enable it to provide a wide range of services. “To clarify our business, we primarily operate as a service provider. We do not engage in designing and producing parts; that responsibility lies with our customers. Our job is to enhance those parts, making them better, and suitable for the end use of the part. When a customer produces a part, the initial microstructure of the part is often not uniform, which can lead to issues like breakage. In other cases, a customer may want a part hardened or softened. A part may have porosity issues and require densification. The list goes on; our services include anything from HIP to aluminum processing (such as solution and aging), austempering, ferrous metal processing (such as normalizing, oil quenching, temper annealing), coatings, and nitriding (including ion, plasma and gas nitriding), as well as ferritic nitrocarburizing. We also offer vacuum brazing to support prime and tiered suppliers across a variety of industries. We are a specialty metal processor, optimizing and enhancing the performance of our customers’ parts and ensuring that they meet higher standards and provide superior functionality.
“The sheer breadth of services we provide is one of the key factors that sets us apart from our competitors. It is rare to find another business offering such a comprehensive range of services. Another differentiating factor is our technical expertise. Our team includes numerous seasoned metallurgists, several with advanced degrees and many years of hands-on experience helping our customers to solve problems. Our diverse service offerings and strong technical expertise enable us to provide exceptional service and support to our customers, surpassing that of most other heat treaters in the industry,” Steve emphasizes.
Steve discusses Aalberts’ day-to-day operations across its multiple sites in the US. “We have operational sites located in Wisconsin, Michigan, Indiana, Ohio, New Hampshire, Connecticut, Arkansas, and South Carolina. Being present across various locations, our core business revolves around offering heat treatment, brazing, and HIP’ing services that are typically demanded within a 300-mile radius. While the production of parts may be offshored, heat treatment processing typically takes place near where our customers are based to reduce logistical costs and lead times. Our diverse geographic positioning provides us with a strategic advantage, allowing us to effectively serve a broader customer base. Our manufacturing facilities operate mostly on 24-hour shifts, with some running two shifts and many running three, five-to-seven days a week. The size of our sites ranges from roughly 30,000 square feet to 160,000 square feet, and the staffing levels at each plant vary from approximately 12 employees to around 55-to-60,” he explains.
As environmental regulations become more stringent, Aalberts has proactively integrated them into its services. “From a sustainability and green initiative standpoint, we prioritize initiatives aimed at minimizing our energy consumption and carbon footprint throughout our operations. This involves implementing various enhancements, such as the installation of new burner technology that reduces our natural gas consumption. Currently, we offer a product called NitroSteel®, which is a ferritic nitrocarburized bar. In simple terms, the manufacturing of this product involves changing the surface of a steel bar or tube, improving its durability and corrosion resistance. This product is primarily used in cylinder rod applications, such as those found in bucket loaders, tractors, and shock absorbers. Traditionally, most of the market for cylinder rods has been supplied with chrome-plated bars, the production of which has long been known to have negative environmental impacts. The production of our NitroSteel® product is an environmentally friendly process, a factor that will become more and more important to cylinder manufacturers who are committed to sustainability,” Steve concludes.
Aalberts has accomplished significant growth and has strengthened its services throughout the US through a strong focus on mission-critical people, technology, innovation, and a relentless pursuit of excellence. The company continues to pursue growth, seeking opportunities where technology matters and real progress can be made.