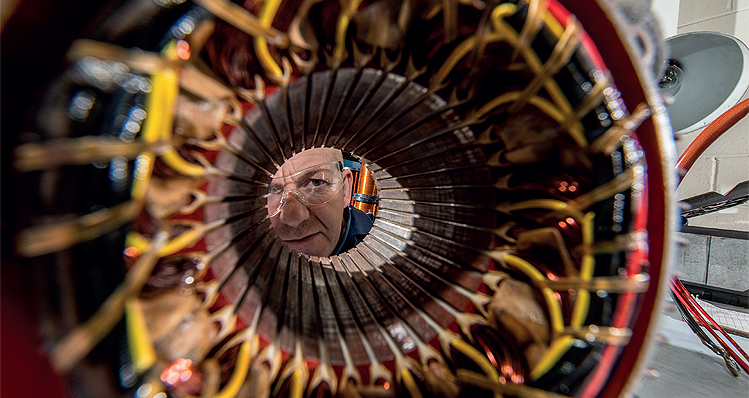
Adapt and evolve
The Covid-19 pandemic has pushed businesses and leaders to reconsider the way that we operate as a society. ‘Build back better’ is common rhetoric used to describe how we can recover from the pandemic and concentrates on redesigning the global economy by prioritising sustainability and tackling the climate crisis. To support this initiative, Prime Minister Boris Johnson has pledged that offshore wind farms will power every home in the UK by 2030, aiming for net-zero emissions by 20501.
Every business, in every sector, has the legal and moral duty to support a greener future. As we move into the post-pandemic world and green initiatives take centre stage, engineers and manufacturers must consider adopting new approaches to support the energy transition and the environmental and economic crisis. The circular economy is an existing model that can be used to change the way we use natural resources for the better.
A closed-loop system
It’s no secret that the practices used by the engineering and manufacturing industry have played a significant role in contributing to the climate crisis. It is estimated that the UK generated 37.2 million tonnes of commercial and industrial (C&I) waste in 20182.
At present, the go-to system in manufacturing is described as the linear economy where we take, make, and waste. We take resources, manufacture goods and buy products. When those products become dated or break, we throw them away. This system is not only expensive; it is having a catastrophic effect on our environment.
The circular economy is at the forefront of rethinking how we create and consume. It is an economic system that aims to eradicate waste through the continual reuse and repurposing of resources. The circular economy model creates a closed-loop system where once a resource is in use, it stays in the manufacturing and consumption cycle for as long as possible. Its philosophy is parallel to the linear economy as it aims to make, use and then remake again.
The principles outlined within the circular economy are to design products that are built to last, preserve and extend what already exists and to use waste as a resource. In essence, it aims to keep materials in use for as long as possible, alleviating the need for them to end up in landfill.
While these principles can be implemented during the engineering and manufacturing process, the most significant challenge we face is changing our way of thinking.
Adopting a circular mindset
Old habits die hard. It has become commonplace that when a product or tool breaks or becomes worn, we dispose of them with little thought. Engineers, manufacturers and procurement departments alike must start to adopt a circular mindset to overcome our ‘throwaway culture’.
Rather than disposing of products and materials when they break, firms should consider if it can be repaired or repurposed. For example, if you have sections of piping that are subject to erosion, you should determine if the piping is suitable for refurbishment. Not only would the piping avoid landfill but would be renovated using the latest technology and techniques, meaning its likely to be a superior product than when in its original form.
The environmental impact of this is evident, but the economic benefits are frequently overlooked. Often, refurbishment and repair is a more cost-effective alternative to replacing a bespoke product or tool. Additionally, if we start to embrace a circular vision, there’s an opportunity to use waste to create new products and solutions which can be sold to make further revenue.
Engineers hold the key that could unlock a world of possibility beyond the repairing of products. To fully implement the circular economy, products need to be designed with durability in mind. This approach would require goods to be designed for modularity, disassembly, remanufacturing and refurbishment with attention given to minimising waste that occurs from over-specification. It’s only through designing for material efficiency that we can truly eradicate waste and support environmental initiatives.
Why aren’t firms already embracing this model?
The answer is quite simply that we have never had to truly consider the environmental and economic impact of consumption in such detail before now. With the energy transition in full swing and our industry under a microscope to change for the better, there is a clear benefit of implementing circular systems into engineering and manufacturing processes. The circular economy model can support the energy transition by reducing energy consumption and promoting the most efficient use of resources, such as converting wind into power.
This model is gaining such momentum that the Scottish Government is in the process of consultation for the Circular Economy Bill to become legislation. This could enforce new laws that would introduce reporting mechanisms to help monitor, track and reduce waste3.
The first step we can take as an industry to adopt the circular economy is to change our mindset, step back and ask if there is a better way of doing something. We must discover alternative means of managing our resources, engineer with durability in mind and aim for waste disposal to be our very last option.
Jim Davidson
Jim Davidson is CEO of Albacom a Scotland-based engineering and manufacturing firm that has diversified into sustainable engineering. Jim is a keen advocate for the circular economy model and has become an ambassador for the initiative. The company’s recent merger with energy storage company Genista Energy has expanded Albacom’s offering into the renewable energy sector.
www.albacom.co.uk
1 https://www.bbc.co.uk/news/uk-politics-54421489
2https://assets.publishing.service.gov.uk/government/uploads/system/uploads/attachment_data/file/918270/UK_Statistics_on_Waste_statistical_notice_March_2020_accessible_FINAL_updated_size_12.pdf
3https://assets.publishing.service.gov.uk/government/uploads/system/uploads/attachment_data/file/918270/UK_Statistics_on_Waste_statistical_notice_March_2020_accessible_FINAL_updated_size_12.pdf