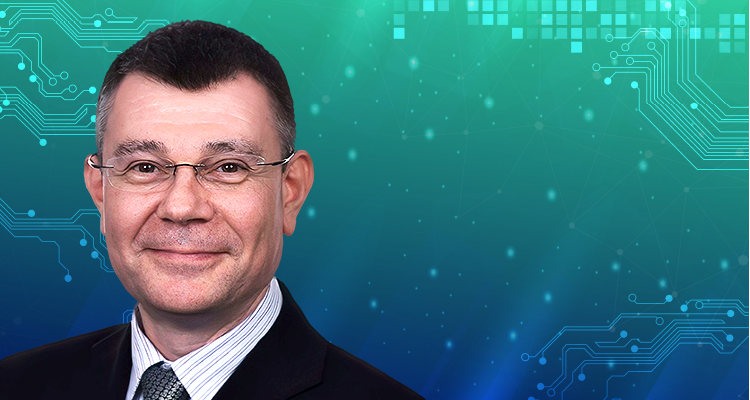
Adrian Park discusses Hexagon’s vision of empowering an autonomous, sustainable future
Adrian Park, Vice President for Pre-sales for the EMIA region has been working at Hexagon for 16 years. “I joined from a Norwegian owner-operator,” he begins. “At that time, they were called Statoil, now Equinor. I was an advisor in the area of technical information management and that included responsibility for the handover of information and documentation from large CapEx projects to operations. I benefitted from early exposure to digital twin technology and brought that knowledge to Hexagon while working on solutions aimed at the owner-operator community as we tried to expand our business in that area. Then about three or four years ago, I started my current role in pre-sales for our Europe, Middle East, India and Africa region. We’re a team of around 50, supporting the sales function in pursuing opportunities from the early stages all the way through to purchase order, prior to handover to our implementation teams. While I’ve only been in my current role for a few years, I’ve been working in the industrial facilities field for over 40 years and have been in Norway now for over 30 years.”
Harnessing data
Hexagon is the global leader in digital reality solutions, combining sensor, software and autonomous technologies. Its solutions enable customers to harness data, putting it to work to boost efficiency, productivity, quality and safety across industrial, manufacturing, infrastructure, public sector and mobility applications. Alongside managing his team, Adrian also functions as an industry consultant. “What I enjoy the most is getting out to meet customers, so, that we can understand the challenges they’re facing and pinpoint how our solutions can help resolve those issues on a day-to-day basis,” he explains.
Throughout his time in the industry, Adrian has experienced significant change, particularly so, in the field of information management for industrial facilities. “These days, digital transformation has been absorbed into that sort of movement. Whereas in the past, it tended to be a niche subject, now it seems to have leapt to the top of the executive agenda,” Adrian continues.
“Many of our customers are interested in how they can better manage information, and how that information can be leveraged to contribute to improved manufacturing, safety, quality, productivity, and sustainability. This focus has become much more mainstream than it was, say ten years ago. Of course, the technologies have also matured, which allows us to implement them in a much more practical way and we’re increasingly moving to the cloud and SaaS solutions that were not available to us a few years ago.”
Smart digital reality
Indeed, Hexagon’s vision is for a smart digital reality. “We want to move beyond the digital twin towards the autonomous industrial facility that reduces or eliminates the need for human intervention. We explain it as being a feedback loop between the real world and the digital world, fusing them into a single, smart digital reality. As such, we’re using some key technologies to move in this direction.
“Our reality capture solutions include fully robotic laser scanning solutions that are now commercially available. The scanners can move autonomously around a facility and capture 3D reality. Alongside this, we’ve got positioning technologies which basically allow us to track anything, anywhere, anytime; whether that’s a person, a vehicle or a piece of equipment. We also have design and simulation technologies with which we can digitally replicate the real world of an industrial facility. Lastly, we have locational intelligence solutions which provide situational awareness surrounding events, both past and present, in a geospatial context. Together with automation that manages tasks and workflows, we can utilize these technologies to create an autonomous industry.
“Central to the smart digital reality concept is what we’re calling the digital backbone. This is where we capture, consolidate, and contextualize this information. It’s much more than a platform for visualizing and analyzing information. It’s got enough intelligence for us to be able to execute work processes that enable improved safety, quality, efficiency, and productivity of industrial facilities. An important aspect of it is how you present information to people. We use the term, the single pane of glass; the idea being that we present information in a context that enables clients to work safely and effectively. That can include information that we’re pulling from our smart digital reality and the digital backbone, but it can also be information we pull from external sources. For example, a maintenance supervisor logging into the system might be able to see from a digital model where maintenance or inspections have been delayed on critical equipment and can then initiate remedial action. Equally, a construction planner would have near real-time access to design and fabrication progress; whether a material has been conditioned, purchased or delivered to the site, for example. With digital reality, we’re going to be able to positively impact people’s day-to-day work,” Adrian enthuses.
This reinforces the aim of enabling people to make faster, better decisions, and in some cases, automate certain aspects to reduce the amount of human intervention.
Adrian continues: “One of the biggest pressures on the manufacturing industry today is sustainability. There are increasing demands in terms of legislation, alongside greater stakeholder expectations for manufacturers to be more sustainable. While the smart digital reality by itself can’t resolve the issue, what it can do is help organizations to make incremental improvements. For example, having an up-to-date digital twin can reduce the need to travel to a site and verify the information. Additionally, having more quality information available should enable better decision-making, such as reusing or repairing equipment rather than replacing it.
“We also see today’s manufacturers under pressure to do more with less. As such, it’s important that people become more efficient and productive. By improving access to information and automated workflows we have greater traceability. Ensuring that plant floor workers have easy access to the right information to perform their work safely and efficiently has probably never been more important than it is today,” he reinforces.
“Manufacturing facilities need to be sustainable, resilient, and profitable. At Hexagon, we don’t see any contradiction between improving sustainability and profitability. Indeed, we always talk about the marriage of economic and environmental sustainability as being potentially the greatest business opportunity of our generation.
“In fact,” Adrian concludes. “We’ve got a perfect storm of opportunity to make a major impact on manufacturing with digital technologies. There’s never been quite this level of executive engagement. There’s also the industrial imperative to make a change. Technology has matured and progress is such that we can really make a significant impact on safety, productivity and sustainability.”