Alongside empowering employees, Kontroltek’s new Employee Ownership Trust boosts business growth and innovation
In a world where globalization and market demand pressures often encourage equipment replacement over repair, Kontroltek was founded to keep repairing alive, offering a more sustainable alternative and a hugely positive contribution to organizations’ asset management strategies. The company believes in providing solutions, rather than up-selling replacements, making it a direct competitor to traditional suppliers in the market. With a vision to be the partner of choice for industrial repair solutions, Kontroltek’s mission is both people-powered and customer-centric. By prioritizing clients and empowering its workforce, the company guarantees that customers remain at the forefront of its operations while ensuring employees are equipped to tackle any challenge they encounter. Andrew Follant, Managing Director, takes a deep dive into Kontroltek’s background and operations.
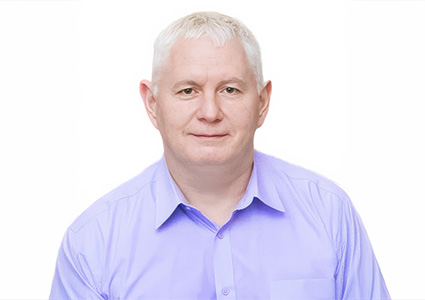
Continuous improvement
“Kontroltek emerged from a management buyout of my previous company 13 years ago. Thankfully, the original 12 employees placed their trust in me and themselves to create a new type of industrial electronic repair firm. The difference lies in our approach to running the business. Indeed, Kontroltek was formed as a family-style company with the vision that at one point in the future, every single team member could become one of its owners. Over the years, we have grown rapidly and now offer electronics and mechanical repairs for the manufacturing sector and automated businesses across numerous industries, including automotive, food and beverage, facilities management, utilities, aerospace, and renewables to name a few. Six months ago, I decided to establish an Employee Ownership Trust (EOT), which now owns 60 percent of the business. This move is intended to ensure the company’s success and continued progression, with our employees at the helm going forward,” he opens.
Cath Demaid, Director of Commercial and Human Resources (HR), tells us more about the impact of the EOT on Kontroltek and its employees. “The EOT acknowledges and rewards the invaluable contributions made by every staff member to the business, particularly those who joined Andrew at the outset. Andrew’s intention and passion have always been to foster a sense of ownership and belonging for everyone in the company.”
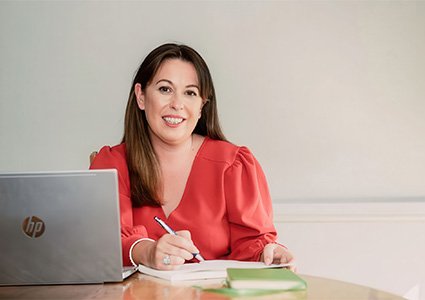
Though only recently implemented, the EOT has already started positively impacting the culture at Kontroltek. “Given my position as Commercial and HR Director, I have been very pleased with the response to the EOT. Since its implementation, I have noticed that our employees share more ideas with me, with a focus on continuous improvement in alignment with growth. Our team is now much more mindful of costs, expenditure, growth, and profit, and this has resulted in a positive impact on the business. For example, people are noticing expenditure more and there is a renewed focus on quality. This is good for the business because it makes us leaner, more productive and more profitable. Moreover, I find that our employees are more willing to approach us with suggestions for improving the way we work. From a commercial perspective, the EOT has sharpened our focus on customer service, and I have observed significant enhancements in this area,” Cath reflects.
Efficient and effective testing
Moving away from the EOT, Andrew noted that on the technical and production side, Kontroltek has significantly invested in test rig capabilities. “A long time ago, we identified that to grow, we needed to fully functionally test equipment for our customers. To understand what fully functional testing is, let’s consider the analogy of a car. If a car’s engine needs replacing, the easiest way to test the engine is to replace it and drive the car on the road. The same principle applies to our test rigs. We build a rig to test a customer’s product, aiming to replicate their machine. To do this, we reverse engineer things. For example, many years ago, one of our national rail customers had signal box issues that were controlled by a programmable logic controller (PLC) that switched the rails over. While this could be done manually via a telephone and a button press, there were automated systems behind the scenes. By reverse engineering the test rig, we enabled our customers to plug in the PLC and test it, resulting in a more efficient and effective testing process,” he explains.
Maintaining its excellence through investments such as this has helped Kontroltek maintain its leading position in the marketplace. By continually developing testing facilities, developing staff and prioritizing innovation, Kontroltek looks set to provide the most efficient and cost-effective repair solutions for UK industry in the years to come.