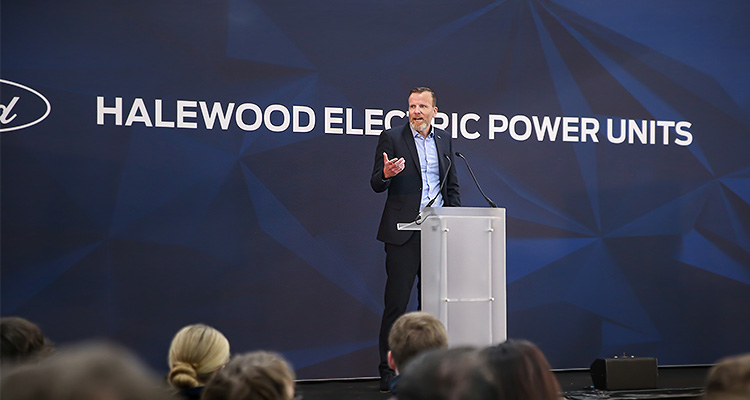
Behind the scenes at Ford’s Halewood Plant: where industrial heritage meets cutting-edge manufacturing
For more than a century, Ford has been pioneering innovation in the automotive industry. As the industry charges toward an electrified future, Ford’s goal is to help build a better world, where everyone is free to move and pursue their dreams. Ford’s Halewood Plant (Halewood) stands at the heart of this transformation, playing a central role in the company’s objectives. Located in the village of Halewood, near Liverpool, the plant’s current products include transmissions for iconic models like the Fiesta, Focus, Kuga, and Transit. Since 2024, Halewood has been manufacturing components for Ford’s next-generation electric vehicles (EVs), including the E-Transit Custom, E-Tourneo Custom, Transit Courier, Tourneo Courier, Puma, and further future products. Lee Meyers, Plant Manager, provides an overview of Halewood’s role in Ford’s operations.
“Halewood is a transmission plant established in 1964, which was an interesting time for the region. Like many transmission plants in Europe, in 2001, it transitioned from being a Ford plant to being operated under Getrag Ford Transmissions (GFT). This joint venture lasted until 2021, a 20-year period that could be considered quite an uncertain time for our employees. However, it was key in preparing us for where we are today, as it allowed our team to bid for work with all original equipment manufacturers (OEMs). To that end, everyone was required to sharpen their focus and develop an entrepreneurial spirit to ensure that we remained competitive, as we had no divine right to be awarded work for Ford or anyone else. In March 2021, we dissolved the joint venture, thereby reintegrating the facility back into Ford. As a result, Ford now has a highly efficient plant that is not only competitive on cost but also boasts a strong reputation for quality. This success helped us secure the bid for power unit work for EVs, enabling us to move forward with an electric future,” he begins.
Proactive approach
In a recent development, Ford has awarded Halewood a £380 million investment as part of a revitalization program. “Consisting of two phases, this investment enabled us to become the first European power unit plant. No company would award £380 million in investment merely because Halewood is a great place to work with talented people. This decision was driven by the total landed cost at the customer vehicle plant, which includes the logistics of delivering the power units to the vehicle plants. Consequently, we worked closely and diligently with our trade union business partners to agree on a framework for how we will run the business moving forward. The facility we now have can be traced back to our flagship initiative, E:PriME. This began at our research facility in Dunton, where our powertrain manufacturing engineering team created a prototype facility to determine the best way to produce a power unit. By working with the government and various partners, our research facility was able to refine that process, leading to the start of mass production of this new product. Thanks to the development work at Dunton along with a significant amount of reuse of existing components and processes, we were able to put together a successful bid,” Lee divulges.
Production of Ford’s new electric drive units commenced in December of 2024 at Halewood. Lee reveals how the first few months have performed thus far. “Although every launch is not without challenges, we are currently meeting our targets, an impressing feat considering we have onboarded over 400 people while simultaneously introducing new products, technologies, and processes. Typically, this would not be the recipe for a successful launch, but our proactive approach has made the difference. We have heavily invested in upskilling our teams particularly with the Rotor and Stator teams. In additional to traditional training, we also involved our teams directly in the commissioning and sign-off processes and fostering collaboration with our machine tool vendors. The role of our machine tool builders cannot be understated. While making gears and machining components and remain parts of our core skills, our growing focus on mastering new technologies has also been transformative. What is most remarkable is how everyone, from new apprentices to employees with over 40 years of service, has fully embraced this opportunity to enhance their skillsets.”
Close relationships
As Ford’s first European EV power plant, Halewood plays a critical role in the overall production of the firm’s finished EVs. Lee explains what made Ford choose Halewood as the ideal facility for this development. “During the bidding process I mentioned earlier, our reputation for quality and our progressive team were key to our success. Once the bid was secured, the real work began, with the powertrain manufacturing engineering team from the E:PriME days developing the processes. Additionally, we took the unusual step of embedding some of our engineers into those teams, allowing them to work directly together to develop the processes, thus significantly enhancing our expertise. When those engineers later moved on to the next project, our remaining team members, who are responsible for running and maintaining the facilities, had already worked closely with our machine tool vendors and taken ownership of the processes. Traditionally, a company might spend heavily on new machinery and expect it to work perfectly from the start without further optimization. Meanwhile, when we receive new machines, we assume they are at their worst and use several improvement methods to refine both the equipment and the facility. By doing so, we keep increasing efficiency, developing better methods, and ultimately outperforming the original specifications,” he informs.
If there is one aspect of Halewood that Lee is especially proud of, it is its unique approach to community engagement. “Throughout my career at Ford, the most inspiring thing I have witnessed is our employee-led charities committee. Every Halewood employee donates a portion of their wages to the committee, and the team acts swiftly to make an impact. To amplify this effort, we partnered with Ford Philanthropy to pledge £1 million in support of local community groups across the city region. This funding focuses on essential services, education, and more. We chose three key partners; one in education; another dedicated to workforce readiness, named Strawberry Fields; and the Torrington Drive Community Association (TDCA), a historic school-turned-community center. TDCA was built over 60 years ago and once provided food services and free school meals to children in an underserved area. Today, through the hard work of their team they can maximize the impact every donation to ensure it supports the community. We have helped them refurbish their aging building and sustain their social supermarket, where residents can shop for essentials at symbolic prices (like pennies per item) instead of relying on traditional food banks,” he emphasizes.
Similarly, with his origins as an apprentice in the automotive industry, training is very close to Lee’s heart. We learn more about Halewood’s recruitment strategy, aimed at maintaining a strong team aligned with its values. “I am a passionate advocate of apprenticeships, which is why we have significantly expanded our apprentice program in the last few years. My objective is to give our apprentices the same experience I had, consisting of working with alongside talented and supportive people. One of the things that helps attract new apprentices is Ford’s reputation as an employer of choice. At Ford, we prioritize treating our people well at every level, and while I may be biased, I genuinely believe Ford stands above other automotive companies as the best company to work for. Much of this stems from Bill Ford’s leadership as Chairman, which ensures long-term strategic vision while maintaining a family-like culture that truly cares for employees. On the training front, we invest in upskilling programs, particularly in the latest technological innovations which are a critical focus for our future. Indeed, our new facilities meet Industry 4.0 standards, integrating connected machines, robotics, and human collaboration. As a result of this shift, the skills we require have slightly changed. Data science, for example, is now essential to transform operational data into actionable knowledge. Given that finding individuals with those skills can be difficult, our strategy has mostly consisted in recruiting people with the right mindset and attitude, and then developing their technical expertise internally,” he concludes.
Merging innovation, technical expertise, and community engagement to drive mobility forward, Halewood embodies Ford’s legacy and future.