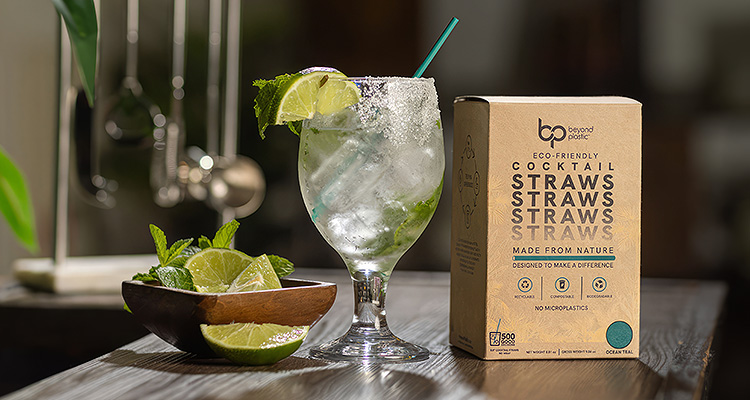
Beyond Plastic: Biodegradable Polymers for a Green Future
Beyond Plastic was started to create fully biodegradable polymers using a revolutionary production and harvesting process that sources high-quality, industrial grade polyhydroxyalkanoate (PHA). Based in Southern California, the founders of Beyond Plastic combine nearly 50 years of beverage experience with major brand success stories. Together, they share a passion for transforming the plastics industry, freeing it from the environmentally harmful products they’ve seen throughout the years. Both want to blaze a path where future generations truly experience a world that goes beyond plastic.
“PHA is similar in some ways to polylactic acid (PLA),” begins Fred Pinczuk, CTO. “People are probably more familiar with PLAs as they’ve been around for longer and are mostly used for food packaging. PHAs, on the other hand, have predominantly been used for medical applications and it’s only relatively recently that there have been attempts to shift the material over to packaging use.
“PLA is a biopolymer made from renewable resources such as corn, sugarcane, and cassava. PHA, however, can be produced from a variety of sources, including bacteria, algae, and plant oils. Compared to PLA, PHA is both compostable and biodegradable in marine environments. While PLA is industrial compostable, it may stay for up to a thousand years in the marine environment. PHA is a very interesting material. It can be as soft and amorphous as rubber or as hard as acrylic.”
PHAs are a class of biodegradable polymers that can be obtained from naturally biosynthesized materials and carbon-rich renewable resources, resulting in far fewer emissions and energy consumption than traditional plastics derived from fossil fuels. A PHA biopolymer is a polymer that is produced by a living organism, such as a plant or microbe. These polymers can be composed of sugars, proteins, or nucleic acids, and they are the building blocks of many of the materials found in nature. A biopolymer-compounded material is made by combining biopolymers with other substances, such as inorganic compounds into biodegradable packaging materials.
“We work with a variety of brands that provide clean material in different states, whether amorphous or crystalline. We then blend the raw material, used for injection or blow molding for example, to make products suitable for a variety of packaging applications,” Fred explains.
“The material resembles plastic and behaves like it. Most importantly, it is 100 percent recyclable. The problem is whether the infrastructure exists to support that recyclability. I can’t speak for the UK, but the US recycling industry is very fragmented from state to state. Even in the more progressive states, like California, essentially only a couple of plastics are recycled, and the remainder are sent to landfill or incinerators. This leads to environmental contamination through the release of microplastics.”
When PHAs are discarded into the environment however, they can be broken down by microorganisms that are naturally present in the soil or compost. This process is an important part of the global carbon cycle, as it helps to recycle the carbon contained in these materials back into the environment. The rate of decomposition will vary depending on several factors, including the type of material, the presence of other nutrients, and the environmental conditions.
“From printer filament to drinking straws and bottle caps, Beyond Plastic is setting extremely high standards when it comes to bioplastics. Our PHA-based bioplastic is a revolutionary green alternative to traditional plastic, as it can completely biodegrade without leaving behind any harmful footprint. We’re great proponents of recycling and while we fully endorse recycling, truth be told, as a nation, we don’t have a great track record. Until we’re much more effective recyclers, having fully biodegradable alternatives in place can mitigate environmental contamination should the products be discarded.”
Combining the latest technological advances with expertise and capabilities, Beyond Plastic works with manufacturers to finetune production equipment. The company trials machinery and suggests modifications and customizations to make the equipment and production process commercially viable.
“We’re making strides in commercialization but there are barriers to entry. Alongside the availability of specialty equipment and a lack of mandatory laws, cost is an issue. PHA is still in its infancy and as such, comes at a premium. Currently, these materials are marketed to manufacturers as a way to address the plastic waste challenge, rather than as a cost-saving exercise. That said, with greater adoption, which will inevitably come in the next few years, manufacturers will be able to enhance efficiency and output and therefore, reduce cost. With the right equipment and modifications, there’s no reason why manufacturers can’t run petrochemical and PHA plastics alongside each other as an interim solution,” he elaborates.
Fred is a beverage industry expert and has worked extensively with co-polymers for extrusion systems and sensitive materials products, such as wines and fruit juices. From equipment review and recommendation to system layout and implementation, he specializes in new product line start up and provides cost effective technical solutions to get products on the shelf at the lowest possible cost.
“We do much of the R&D work ourselves. Our PHA filament started out as a simple extrusion process, and mainly from a desire to understand the material’s properties and behaviors rather than to commercialize it. From there, we focused on refining our processes and trialing alternative applications. In terms of our compression molding, we’ve been able to innovate more quickly because of all the learning that has come before. We’ve evolved the applications and continue to do so. We have commercialized a custom 38 mm bottle closure that meets all standards for TUV Austria composting as well as their Marine Biodegradability certification. The closure is compatible with standard beverage offerings with the benefits of added packaging performance while raising the conservation effort and value. Our next innovation is likely to be in firm reforming solutions, such as coffee cup lids,” Fred enthuses.
To support its precision innovation, Beyond Plastic works closely with suppliers, such as Movacolor. With over 30 years’ experience in developing tailor-made dosing solutions for the plastics manufacturing industry, Movacolor’s mission is to support plastic producers in achieving their sustainability goals by means of its unique modular dosing and blending concept. “Movacolor is a great supplier of ours. The company is responsive and willing to custom create solutions to meet our emerging and precise needs,” Fred adds.
“Since I’ve been working on this project, it’s become increasingly clear that we need to educate people on the possibilities and potential of PHA use in products. From the raw material to the finished product, Beyond Plastic is the link enabling commercialization and accelerating its application. Many of our suppliers are based in Asia, so, looking to the future, we’ll probably expand closer to our supply source to enable mass manufacturing. We’re talking to one of the largest cosmetic suppliers in the world right now, looking at how we can replace cosmetic tubes with sustainable solutions. While there has been a shift in the cosmetics industry,” he concludes, “the packaging side of things is still a big issue and that’s where PHA can really come into its own. It can replace non-recyclable packaging with a biodegradable alternative that offers the same appeal and identical functionality.”
www.beyondplastic.com