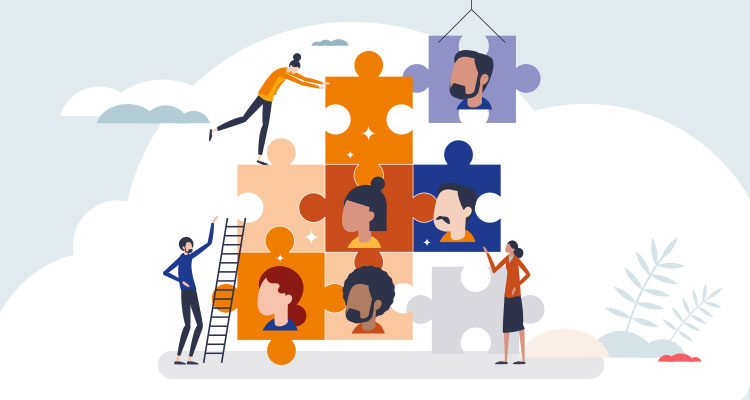
Bridging the labor gap in US manufacturing.
The US manufacturing sector, a $2.3 trillion cornerstone of the economy, faces a severe labor shortage that threatens its ability to meet demand and remain competitive. Finding the right workers is yesterday’s, today’s, and tomorrow’s problem. Manufacturing was hit hard during the pandemic and struggled to recover. However, now that it has recovered roughly to pre-pandemic levels manufacturers are struggling to return to growth, largely due to a talent gap. Lack of appropriately skilled workers could result in 2.1 million unfilled jobs by 2030, a gap that could cost as much as $1 trillion annually by that same year.
External factors like mass deportations and tariffs further complicate the landscape. Manufacturing has historically been heavily reliant on immigrant workers, especially in hard-to-fill roles. This is part of the untold story of the pandemic, as not only did it slow down movement in the US, but it also brought global migration flows to a grinding halt. This put immigrant-reliant sectors like manufacturing even further behind than other businesses and industries when it came to the shortage of skilled workers. The current policies leading to deportations reduce this critical labor pool, while tariffs increase costs for manufacturers, leaving fewer resources for workforce development. Addressing these challenges requires innovative strategies to attract, develop, and retain talent.
The scope of the manufacturing labor shortage
The labor shortage is not just about numbers, it’s about skills. While advances in automation and smart manufacturing can go some lengths to reducing the number of workers necessary it is not enough. Workers are still needed, especially for skilled workers to operate and maintain complex machinery. Counterintuitively, the same advances that slightly reduce the number of workers needed in fact makes the labor shortage harder to address because many job seekers lack these specialized skills.
Compounding this issue is the retirement of baby boomers, who at their peak were the largest generation, so there simply are not enough people to replace them as they age out of the workforce. These overlapping factors, fewer migrants and Baby Boomers retiring with not enough people in younger generations to replace them, place a major strain on available labor. Additionally, perception plays a role in further shrinking the available workforce. Despite modern manufacturing being clean, high-tech, and innovative, many still view it as low-paying and physically demanding work. This image discourages younger generations from pursuing careers in the field.
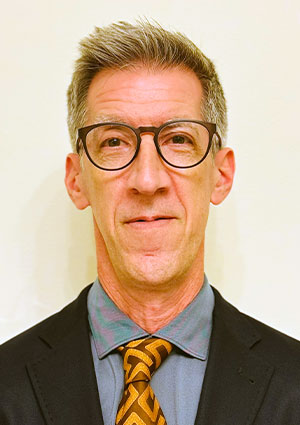
Strategies for closing the gap
Manufacturers face many barriers to growth and success as they must balance meeting workforce needs in the short-term with preparation for longer term challenges. Innovative approaches are required to do so, as advances in technology mean newer products and newer ways of manufacturing them emerge seemingly every day. However, these demands cannot be met solely through technological innovation, so manufacturers must ensure they have labor solutions that help them continue not only to meet demand but to thrive. The extent to which the industry can adopt the expensive machinery, and costly installation has been crimped by the aforementioned years of sluggish growth due to the labor sector, and again the adoption of innovative production methods only further strains the need for skilled workers.
Giving workers necessary skills
For the manufacturing industry to address the labor shortage, not just to recover but to lay the foundation for sustained growth, leaders must invest in their workers, improving the skills of the workers they have while working to attract and train new talent. The upskilling and reskilling of workers must be a priority, and the same programs implemented to do this can be extended to bringing in and training new workers. Apprenticeship programs and on-the-job-training tailored to retraining can broaden the pool of workers able to operate advanced technologies like robotics and AI systems, innovations that can greatly improve productivity and output if the necessary skilled operators can be found. Furthermore cross-training workers across multiple roles can help increase flexibility during peak periods, when certain positions may be in higher demand. These strategies not only fill immediate skill gaps but also build a more adaptable workforce capable of meeting future challenges.
Perhaps more important than the reskilling and upskilling of the existing workforce is rebranding to attract new talent. Baby Boomers aging out of the workforce already means there will be a shortage baked into the demographic shift, with not enough younger workers to replace them. This is amplified by outdated perceptions of manufacturing careers. By focusing on apprenticeships and training programs that give workers the necessary skills to operate the advanced AI and automated technologies that are increasingly part of the manufacturing process, leaders can begin shifting that perception while attracting and training new talent.
Attracting new workers while retaining existing ones
Furthermore, the outreach must meet younger workers where they are. First and foremost, this means working to change the perception of manufacturing and doing so by attracting talent through the social media and job-seeking platforms used by Gen Z and millennials. Additionally, especially on social media, this outreach must be coupled with emphasizing career growth opportunities in the manufacturing industry. This can be done by highlighting industry success stories of individuals who worked their way up the ladder, and through emphasizing the growing role of new technologies in modernizing manufacturing facilities. By reshaping the narrative around manufacturing careers, companies can appeal to a broader pool of candidates who may not have previously considered the industry.
Attracting new and upskilling existing talent will only work if leaders also focus on talent retention. A tight labor market, not only in manufacturing but in many industries, means competitive wages and benefits must be offered to keep workers from going elsewhere. Here, again, the same apprenticeship and cross-training programs can be tailored to help. Mentorship programs and leadership training can connect apprentices and new employees with more experienced workers. Through this business leaders can institute a model which puts in place clear pathways to advancement. While workers are learning new and improving old skills, well-made programs can help them see how the gained skills and experience can lead to career advancement within the industry.
Furthermore, industry leaders must understand the new normal. Remote and flexible work options proliferated during and after the pandemic, and while many positions in manufacturing are not compatible with remote work, instituting more flexible scheduling can go far in attracting and maintaining the necessary skilled workers. Retaining existing employees is often more cost-effective than recruiting new ones, making retention strategies essential for long-term success.
Streamlining employment-based immigration
While upskilling domestic workers is essential, immigration reform offers manufacturers an immediate opportunity to address critical labor shortages by tapping into global talent pools. As mentioned previously, with Baby Boomers retiring there simply are not enough domestic workers available to meet the need. Manufacturing has long relied on immigrant workers, and this will not change anytime soon. Industry leaders must work with government leaders to streamline the employment-based visa process. These programs already exist and are widely used, but such collaboration can reduce bureaucratic delays and eliminate redundant documentation requirements. Such expediting of the process will make it faster and easier to attract workers from abroad, make it more cost-effective for businesses as they will more quickly reap the benefits of those workers coming in, and make it more attractive for prospective employees who may be daunted by a long and tedious process.
Furthermore, just as new technologies are changing the way manufacturing is done, new visa categories must be introduced, tailored to meet the specific needs of modern manufacturing. Those proposed under the CHIPS Act to increase semiconductor production are a good example of where to start. By working with government leaders to raise awareness of the specific jobs and skills needed to build a modern manufacturing workforce, business leaders can help build a speedy and reliable pathway for the necessary skilled workers to come where the jobs are. Streamlining immigration processes would allow manufacturers to fill critical roles more efficiently while ensuring access to skilled foreign workers who can complement domestic talent.
Conclusion
The labor shortage in US manufacturing is a complex challenge – but it’s also an opportunity for transformation. By investing in workforce development, rebranding careers in manufacturing, improving retention practices, and streamlining immigration processes, companies can secure a sustainable future for the industry. Manufacturing drives innovation and economic growth across the nation. Solving this crisis isn’t just about filling jobs; it’s about ensuring that American manufacturing remains a global leader in productivity and innovation for decades to come. For manufacturers navigating today’s labor challenges, taking bold action on multiple fronts is no longer optional – it’s essential.
John Dorer
John Dorer is a Global Mobility Executive with a focus on Employer Sponsored Green Card solutions, and the CEO of EB-3 Staffing Solutions for Employers. Headquartered in New York City, eb3.work is the leading company in the US that provides effective solutions in addressing the country’s chronic and growing unskilled and entry-level labor shortage by connecting employers with foreign nationals seeking to work legally in the United States. eb3.work leverages its proprietary business processes and technology to assist qualifying US companies and foreign national workers in navigating the complex US immigration system.