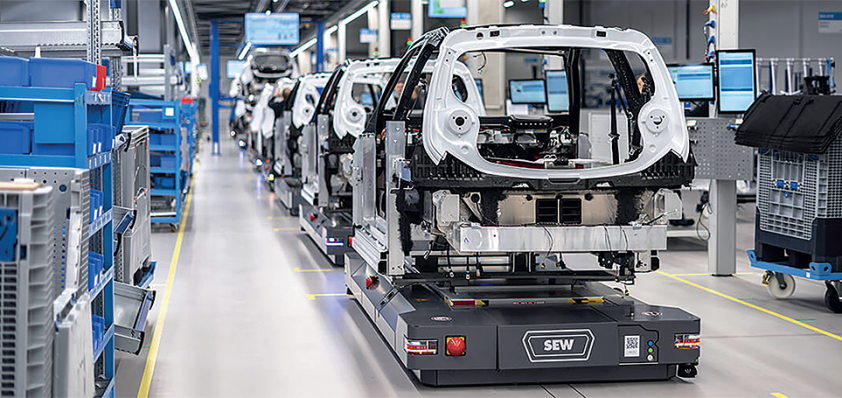
Bright sparks
Industry analysts at Bloomberg New Energy Finance claimed that 2020 is set to be the ‘year of the electric car’, with UK electric vehicles (EV) sales forecasted to increase by 64 per cent of all vehicles sold from 2019. This change is being driven by multiple forces including, but not limited to, government initiatives for greener transportation, industry innovation to find more sustainable solutions and consumers growing more conscientious of their environmental footprint.
In a bid to reduce CO2 emission levels, governments are moving to ban internal combustion (IC) engines, which currently account for 40 per cent of oil consumption in Europe. Sales of new IC engines will be discontinued from 2040 in the UK and France; possibly even earlier than that, with more emphasis being placed on EV. In the UK specifically, the use or purchase of EVs are also being heavily incentivised to drive adoption.
At the same time, more EV models and concepts are being launched by industry players: General Motors (GM), Volvo, Jaguar Land Rover and Aston Martin are some of brands that have announced their intention to be ‘all electric’ in the not too distant future. Something that’s very much welcomed by consumers – battery electric vehicle demand surged by a huge 21.8 per cent in 2019.
A race to keep up with the surge in demand for electric vehicles
To cope with the surge in EV demand, within the next three years we’ll need the UK to launch its first full-scale gigafactory for battery production. This is according to the Harwell-based Faraday Institution, a research institute backed by the government to ensure a steady supply of batteries in the future.
However, simply replacing oil with electric batteries isn’t enough to produce lower emissions from electric cars. Achieving these results will require a redesign of the car’s components. An electric vehicle comes with a whole set of new challenges.
There are conflicting considerations: Mileage and battery weight; safety and lightweight, and customer experience and affordability. The best way to solve those conflicts is to break with traditional workflows and harness technology such as artificial intelligence (AI).
Here are some of the approaches transforming how the automotive manufacturing industry is making electric vehicles and the resulting environmental benefits.
Power: A challenge to perception and to process
At present, the biggest challenge to the electrification of vehicles is the battery and the whole vehicle architecture. Manufacturers need to both find a way to integrate the battery in the car and produce a car that enables the battery to be as powerful as possible, in the most cost-efficient way. The cost of the battery is predicted to fall as production capabilities increase, but this will require funding for at least eight full-sized gigafactories to be built over the next 20 years. Because of this, manufacturers need to save costs in other parts of the production process to afford these investments.
One way is related to how engines are put together. IC engines are currently cast in metal – whether iron, steel or aluminium alloy, which is then milled and drilled – often in two or three sections and joined together. Electric motors have fewer parts than IC engines. They are lighter, less complex, and have lower stresses on the materials. This opens up new process opportunities for the use of lighter materials, for less energy-intensive production and for the adoption of different techniques, including additive manufacturing or 3D printing.
Additive manufacturing can dispense with conventional tooling, as minimal milling or drilling is required. It is particularly well suited to EV batteries for a number of reasons. For example, it offers new geometries that conventional manufacturing methods can’t produce, which can lead to lighter parts. Also, it allows for part consolidation, which results in less bolts and screws, leading to easier assembly and disassembly in the case of replacement or upgrade. Lastly, ‘on-demand’ manufacturing can reduce the need for inventory, spare parts, and localised production.
Multi-material printing capabilities provide opportunities for innovative end products, made of multiple materials that become part of each other. Sensors, batteries, electronics and microelectromechanical systems (MEMS) can also be embedded directly into components.
Sustainability: Consumption and recycling for the most environmentally friendly materials
Sustainability applies as much to manufacturing processes as to materials – their sources and use, reuse and recycling – and to products themselves. When building electric vehicles, there is already a strong focus on recycling, recyclability, circular design and closed loop manufacturing.
The European Union’s End-of-Life Vehicle (ELV) Directive 2000/53/EC sets recovery targets for the recycling of vehicles and components, encourages manufacturers to design their vehicles with part reuse and recycling in mind, and restricts the use of certain heavy metals in new vehicle manufacturing processes. In the case of some plastics such as polyethylene terephthalate (PET), a commonly recyclable plastic resin, recycling of RPET (recycled plastic bottles) has been found to use 70 per cent less energy than virgin fibre production. Elsewhere, additive manufacturing can save as much as 94 per cent of the material by using Rapid Deposition Process (RDP), instead of conventional billet milling and fabrication.
We’re already seeing circular design put into practice. For example, Jaguar Land Rover is designing vehicles that recycle aluminium from old cars into the manufacture of new cars. The development for the second phase of the ‘closed-loop strategy’ has begun with preproduction of Jaguar iPace SUVs that had been destined to be scrapped. Once the batteries have been removed and either recycled or placed into a ‘second life’, sensors in the advanced scrap process identify aluminium, which is then recovered, melted and reformed to use in the production of new cars.
Weight and see: The power of generative design
The engine is the heaviest item in an IC-powered vehicle; in the case of electric vehicles, it is the battery. The bigger the battery, the more power it can store and the longer the range (or higher the speed) it can have. The relationship between weight and range/power is even more impactful in electric cars than in IC vehicles. Small weight savings can make a big difference to performance.
Any weight saving can be used to increase the size of the battery, the car’s performance and reduce how often it needs charging. Materials are inevitably the first thing considered, when it comes to reducing weight – and improving overall vehicle performance and through-life costs.
Lightweighting can be achieved either by switching to a lighter material 15or by reducing the amount of material used in the design. Generative design gives vehicle manufacturers a proven way to improve fuel economy by replacing components with a variety of lightweight, recyclable materials, such as aluminium, magnesium, or PLA plastics. It also enables manufacturers to consolidate components into fewer parts.
Electric motors do not just permit different car layouts, they require them. The shape of battery packs – long, wide and flat – facilitate designs with a lower centre of gravity and allow designers to spread weight across the car’s structure rather more than is the case with IC powered vehicles, where the weight of the engine is in one specific place. Thus, load-bearing structures don’t need to be as strong and can be made lighter. A lighter structure means the car consumes less energy.
Closing thoughts
The move to reduce the carbon footprint of the automotive industry has driven greater innovation in the design and manufacture of vehicles. Electrification is an opportunity to explore different materials and techniques, which will revolutionise the production of electric vehicles and bring the industry closer to achieving sustainability milestones.
Advanced light-weighting approaches through generative design will be pivotal to improving power consumption and the range of electric vehicles, while different materials and compositions will improve the structure of electric cars. A circular approach has huge potential in an industry like automotive, where the manufacturers have the power to impact the entire design and manufacturing approach, creating a workflow that favours recycling and closed loop manufacturing.
Electrification is already playing a pivotal role in accelerating overall innovation in the car industry and automotive manufacturers being supported from government, consumers and the wider industry to continue driving this change.
Zoé Bezpalko
Zoé Bezpalko is Sustainability Strategy Manager at Autodesk. Autodesk makes software for people who make things. If you’ve ever driven a high-performance car, admired a towering skyscraper, used a smartphone, or watched a great film, chances are you’ve experienced what millions of Autodesk customers are doing with our software. Autodesk gives you the power to make anything.
www.autodesk.co.uk