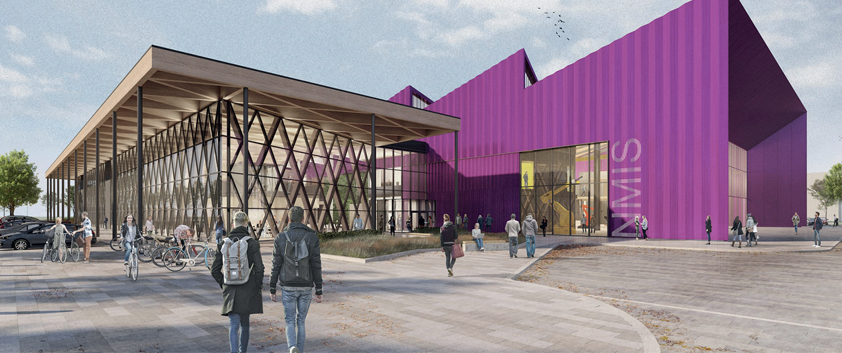
Connections and collaboration
For a manufacturing company to thrive, it’s widely accepted that its operations must be lean – both efficient and cost competitive – and agile – quick to respond to market demands.
The manufacturing industry has met and overcome major challenges in recent years; from fluctuating prices in oil and raw materials to varying currency exchange rates, and now as with many sectors, it has been negatively impacted by Covid-19. The pandemic has vastly disrupted consumer trends for demand and consumption alongside the supply and capability of companies to deliver effective goods to the market. However, the unprecedented challenge of the pandemic has required companies to reinterpret the situation, allowing for new product development opportunities, enabling them to diversify and explore new markets.
Companies have seized upon this prospect and tapped into new markets to expand their product offering, venturing into new areas where there was not an apparent concern before. For example, the expansion into the production of products that assist with social distancing, and the development of ventilators and Personal Protective Equipment (PPE) have all created opportunities for new design prospects and manufacturing routes. These are allowing companies to expand on their product offering while helping address a variety of Covid-19 related challenges.
Preparing for the future
The looming issue of plastic pollution and global warming are still matters that need to be addressed and more companies than ever are required to account for circular economy considerations in their product development; not just for cost and waste saving purposes, but in response to demand for transparency throughout the life-cycle of their products.
Amidst consumer and governmental pressures, undoubtedly there will be an increased demand for product traceability; to easily source where a product comes from, its journey, the source of the material, and importantly what happens at the end of its useful life. Companies will need to trace their manufactured products right through design, manufacturing, installation and maintenance, to decommissioning or end-of-life.
In the face of climate change and amidst increasing consumer expectations, further incorporation of this into legislation in the future is likely. It is reasonable to expect that eventually companies will require an end of life route mapped out for any manufactured product. Can it be maintained, repurposed, or recycled? If there is no other option but for a product to go to landfill after its use, there must be a robust justification as to why.
Although many companies are adopting circular practices as part of their business models, for the majority, it will take the introduction of such legislation to see that change fully take place. As the discussion on this continues, it will be interesting to see where the responsibility ultimately sits.
During a product development project there are multiple key players involved, but who will be legally accountable, ensuring that products have a responsible end of life plan; will it be the company that owns the product, the owner of the IP, the design consultancy or the manufacturer? As this discussion evolves, there will undoubtedly need to be a collaborative approach between the public and private sector, not only for the benefit of the planet but also for the companies involved.
We have already seen the introduction of legislation to encourage more sustainable operations across some sectors, such as oil and gas, where changing attitudes about the environmentally detrimental aspects of the industry has resulted in multiple companies investing in areas such as offshore renewables. There was a measured change in approach taking place prior to the recent disruption caused by Covid-19. Longer term, this may act as an opportunity to re-shape our thinking in the transition towards cleaner energy sources.
The demand for end-to end-sustainability
Similarly, manufacturers will need to re-adjust to increasingly sustainable approaches and invest in cleaner energy to meet the ever-increasing criteria set by companies and their customers. Customers are increasing their knowledge on how factories are using energy and how efficient they are when it comes to where their products are being produced. Companies based in the UK will potentially be more inclined to manufacture locally to respond to drivers regarding the environmental impact of freight or shipping, and mitigating potential risks from using overseas imports, which have been highlighted in a critical way during the pandemic.
To meet expectations regarding sustainable practices, embracing technology and innovation within UK manufacturing will continue to be of vital importance. By adapting processes and operations, re-shaping supply chains and embracing assistive technologies, such as augmented reality (AR) and virtual reality (VR), the manufacturing industry can take steps in recovering from the current crisis, and prepare for future challenges that may lie ahead.
Now more than ever, it is vital that companies are better informed in their product development. A great innovation must be matched by intelligent design, manufacturing and materials expertise. There is no one size fits all solution to manufacturing a part; there are numerous processes and materials that can be considered to ensure that the part meets sector regulations in a sustainable and cost effective manner while meeting demands in quality. To grow and innovate from sector to sector, it is vital that companies continue to build connections and collaborations in order to develop new solutions that meet the world’s ever evolving needs.
Hannah Leslie
Hannah Leslie is a Knowledge Exchange Associate within the Design Engineering Team at the University of Strathclyde’s Advanced Forming Research Centre (AFRC), part of the National Manufacturing Institute Scotland (NMIS). The National Manufacturing Institute Scotland is a group of industry-led manufacturing research and development facilities where research, industry and the public-sector work together to transform skills, productivity and innovation to attract investment and make Scotland a global leader in advanced manufacturing. The University of Strathclyde’s Advanced Forming Research Centre (AFRC) and Lightweight Manufacturing Centre (LMC) are specialist technology centers within NMIS.
www.nmis.scot/get-in-touch/