Considering alternative manufacturing methods can yield promising results
Advanced manufacturers must sometimes compromise the use of improved part designs or advanced materials to best accommodate their existing machining methods. But as Kirk Gino Abolafia of Voxel Innovations explains, as critical industries demand higher volumes of parts and increased usage of advanced materials, perhaps it’s time for manufacturers to consider alternative manufacturing technologies that can catch up with the ever-growing needs of the markets they serve.
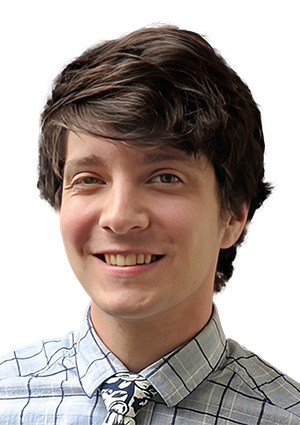
Advanced manufacturers often rely on established, conventional manufacturing methods for their predictability, practicality, and profitability – however, this reliance can sometimes hinder crucial advancements to part designs, improvements of material removal rates, or new business opportunities and applications.
Specifically, improving part designs for critical industries can be especially challenging for manufacturers, as they must balance the usage of advanced materials, increasingly complex features, tighter tolerances, and smoother surface qualities. For example, aerospace manufacturers are seeking to lightweight aircraft components with exotic materials to improve fuel efficiency, and medical device manufacturers are increasingly miniaturizing implantable surgical devices to reduce patient discomfort. Although these advanced part designs can improve lives, their existence can also cause internal friction in advanced manufacturing companies between machinists, engineers, and upper management considering the challenging, or near-impossible, features that they must produce in high volumes using conventional material removal methods.
This has created a sort of ‘schism’ in advanced manufacturing that must be repaired – between the aspirations of design engineers and the inherent limitations of the conventional machining processes. Rather than seeking a solution by tweaking part designs or material usage to accommodate existing machining methods, manufacturers should instead consider alternative machining methods that may be capable of producing advanced-material parts with tighter tolerances and higher repeatability.
An example of one such technology that may bridge this metaphorical gap is pulsed electrochemical machining (PECM), a non-contact and non-thermal material removal method that may be capable of the miniaturized features (including thin walls and high-aspect ratio micro-hole drilling), superfinished surfaces, and advanced-material machining capability that manufacturers need to produce the next generation of advanced components for critical industries without compromising part materials or design concepts.
Manufacturers should carefully consider how and why non-conventional manufacturing processes work before making any further investment. PECM, for instance, removes material without the use of contact or heat, and works on a fundamentally different level than conventional processes. Processes like PECM can be best understood by observing its key components:
The Cathode, also called the electrode, is the custom-designed tool shaped as the inverse of the desired geometry on the workpiece. It is lowered onto the workpiece during machining, but never comes into contact with it – separated by a microscopic gap called the inter-electrode gap (IEG).
The Anode, or the workpiece, can be any conductive material, however PECM is most applicable on tough-to-machine metals commonly found in the aerospace and medical device industries, including nickel superalloys. PECM can technically be used on bar stock or raw plates but is more useful when machining near-net shape parts that are stamped, rough machined, etc.
The electrolytic fluid acts as both the catalyst for the electrochemical reaction to take place, as well as a flushing agent that removes both waste products and heat from the workpiece area. These two critical functions are performed simultaneously as the fluid is flushed into the IEG.
The power supply supplies the electrolytic fluid with the necessary current to conduct the electrochemical reaction; this current is correlated with PECM’s material removal rate.
PECM works by breaking down the chemical bonds of the metal atoms on the workpiece surface into metal hydroxides. These byproducts are created in the electrolytic fluid, which is then flushed away, leaving no heat-affected zones and a superfinished surface quality.
Note: this is only a summary of PECM technology – for a more in-depth analysis on how PECM removes materials atom-by-atom using an electrochemical reaction, click the link at the end of the piece.
As alternative machining methods have unique capabilities and advantages over conventional processes, so too do they have special impediments and disadvantages manufacturers should consider. With PECM, for instance, many of its most definitive traits can act as inherent limitations to the technology:
PECM’s lack of contact or heat allows stress-free machining on features otherwise sensitive to thermal distortion or tool vibration, such as thin walls. PECM is capable of producing <0.075mm or <0.003” thick walls with a 20:1 aspect ratio.
However, PECM is not cost-effective compared to conventional processes when tasked with machining simplistic geometries that may require a high amount of material removal, especially if the workpiece is a piece of bar stock or is not a near-net shape.
PECM’s lack of contact or heat also creates little-to-no tool wear, allowing high repeatability (down to <10um), making PECM optimal for high-volume production.
However, designing a tool requires a complex and iterative engineering process that may not be ideal for short term work but better fit for a job shop.
PECM is concerned with a material’s conductive properties, rather than its toughness, allowing it to machine nickel superalloys at a similar rate to copper – especially useful for advanced materials used in the aerospace and medical device industries.
However, its capabilities are limited only to conductive materials; PECM cannot machine plastics, polymers, or anything else non-conductive.
A custom-designed cathode can machine dozens of features or parts simultaneously, and so long as there is sufficient amperage, the material removal rate is not affected by this parallel processing.
However, developing the tooling capable of parallel processing can be cost-prohibitive for low-volume and prototyping work.
Manufacturers must be mindful that with each unique benefit of a given material removal process comes a unique drawback that requires additional consideration – such as being mindful of the electrical conductivity of the workpiece material, with PECM or weighing additional or unexpected NRE costs.
Engineers often make compromises to best adhere to the constraints of the machining processes to close the ‘advanced manufacturing gap’ – but sometimes, it may be best for the machining processes themselves to evolve and adapt to new challenges and market demands, and new technologies like PECM may be just the right candidate to enact that very change. ■
Kirk Gino Abolafia
Kirk Gino Abolafia is the technical marketing and sales manager for Voxel Innovations, an advanced manufacturing company located in Raleigh, NC that specializes in the development of pulsed electrochemical machining (PECM) for applications in the energy, aerospace, and medical device industries.