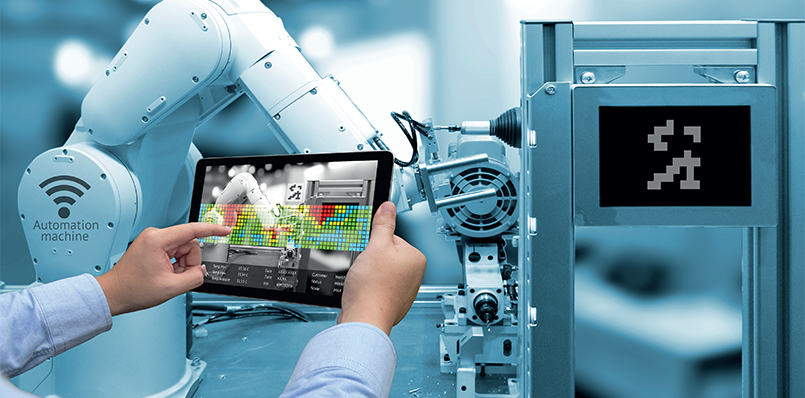
Creating future resilience
Unprecedented, foreseen and unforeseen market shifts have made it critical for manufacturers to be equipped for change. From the automotive industry experiencing a shortage of semiconductor chips to the price of raw materials such as lumber skyrocketing due to an unexpected increase in demand, it is difficult to pinpoint which industry has been hurt the most.
Before the pandemic, manufacturers were already struggling to meet demand and unable to quickly pivot as that demand changed. Covid and events such as the Suez Canal blockage didn’t create new manufacturing issues, but rather exacerbated problems that already existed. Now, people are wondering how manufacturers will use the events and lessons learned from the past year to move forward. One answer – technology. Manufacturers need to let go of their legacy, manual processes to digitally transform the plant floor and use data to build future resilience.
IIoT for efficiency
The Industrial Internet of Things (IIoT) is the network of physical objects in a manufacturing environment (machines, sensors, etc.) that are digitally connected to each other and exchange data. The data exchanged through the machines, such as movements or abnormalities, assesses the health of each machine and can be compiled in the cloud in real-time.
Before IIoT, employees physically monitored these machines themselves and tracked any data or unusual behavior by hand, resulting in more overhead and increased risk of human error. Machines and production lines can fail because of human error or because manual monitoring only took place daily, weekly or monthly when these problems occur more quickly than that. If a machine is performing unusually, manufacturers that utilize IIoT can easily address the issue, saving them money and time.
The use of wireless technology, mobile devices and the ability to access key operational data complements IIoT and greatly improves efficiency. Plant status, alarms or dashboards shared in real-time on plant floor displays or on mobile devices gives operators the ability to receive information immediately and act on it quickly.
As companies begin to digitize their manufacturing processes, IIoT is helping manufacturing adjust and better plan in a more efficient way. It is estimated that 60 percent of global manufacturing companies will use connected device data for analysis in the coming year, which is evidence that IIoT is already driving unprecedented disruption in an industry notoriously for slow technology adoption.
IIoT for predictive maintenance
In addition to improving efficiency for manufacturers, IIoT also helps manufacturers predict and prevent maintenance issues. Too often, manufacturers are in reaction mode, spending unplanned time to fix an issue with a machine that has morphed into a large and costly headache. Since IIoT provides manufacturers with machine data in real time, they are able to predict when maintenance will be needed and quickly pivot to fix abnormalities before they become larger, more costly issues.
An example of the benefits of predictive maintenance can be seen with MPI Corporation, a group of Indianabased companies that handle flat roll material servicing and distribution, metal stamping, heat treating and other finishing processes. At one of the company’s plants, a piece of machinery would occasionally shift out of position and eventually break. It would take that production line offline for days in order to cool the equipment, replace the belt, and bring the machine back up to operating temperature. Once MPI installed an IIoT solution, sensors would monitor if the machinery was beginning to shift and share that data with the manufacturer. As a result, the team could quickly fix the machine, eliminating unplanned downtime and major issues before it was too late.
Not implementing IIoT will cost you
Manufacturers will pay the price for not having an IIoT system in place. If better manufacturing efficiency and predictive maintenance are not strong enough reasons for manufacturers to implement IIoT, what about the money they could potentially save by having these solutions in place? When issues arise on the plant floor, there are large impacts and ripple effects from unplanned downtime and equipment repair.
If a machine is out of service for days, on average, it can cost a manufacturer anywhere from $20,000 – $100,000 per day. Companies can potentially lose $150,000 or more for an issue that could have been solved with an IIoT solution that costs a fraction of that. A recent report found that manufacturers who had an IIoT solution in place experienced a 30 percent reduction in unplanned downtime cost and repairs.
Unfortunately, recalls are becoming a more common occurrence for companies in all industries, from food and beverage to automotive and more. In addition to the cost of fixing faulty products, companies can lose customer loyalty. While that may not be easily quantifiable, it is a serious and sometimes a permanent hit to the bottom line that should be considered. With an IIoT solution in place, manufacturers are able to catch quality discrepancies before a faulty product can hit the market, saving companies thousands and perhaps millions of dollars by lowering or eliminating the cost of poor quality.
Why are manufacturers hesitant?
With benefits like increased efficiency, predictive maintenance and reduced cost for potential risks, why are manufacturers still hesitant to implement IIoT technology? For one, manufacturers are extremely pragmatic. Over the past year, there has been hype around IIoT and digitizing the plant floor, but manufacturers want proof of where IIoT can be cost effective and practical for their specific needs. More case studies and success stories are needed for manufacturers to buy in. Additionally, manufacturers have been reluctant to implement IIoT on their plant floors because they have traditionally focused on Lean initiatives and optimizing the processes they can see, rather than looking ahead. Market shifts from this past year have proven that manufacturers need to create plans and consider all scenarios that could negatively impact manufacturing production in order to create future resilience. Lastly, manufacturers believe that they already have employees whose job it is to monitor machines and record data. IIoT is complementary – it is not displacing jobs. IIoT helps automate processes so experienced employees can focus on more complex issues and new business processes.
The future of IIoT and smart manufacturing
Right now, manufacturing plants are running over 100 percent of previous output levels and need to focus on efficiency and the technologies that will help them automate. The plant floor is changing and for manufacturers to keep up with demand and remain agile, they will need to adapt. Manufacturers who can identify areas of their plant that are error prone or have costly outages, will benefit from implementing IIoT and will see a strong ROI. In order for companies to build future resiliency, they need to invest in smart manufacturing solutions, like IIoT, that automate processes, receive data in real time and quickly highlight machine abnormalities before they become costly.
Ben Stewart
Ben Stewart is VP of Product Strategy at Plex Systems. Plex Systems, Inc.® delivers the first smart manufacturing platform that empowers the world’s leading innovators to make awesome products. Plex gives process and discrete manufacturers the ability to connect, automate, track and analyze every aspect of their business – from the shop floor to the top floor – to drive business transformation.
www.plex.com