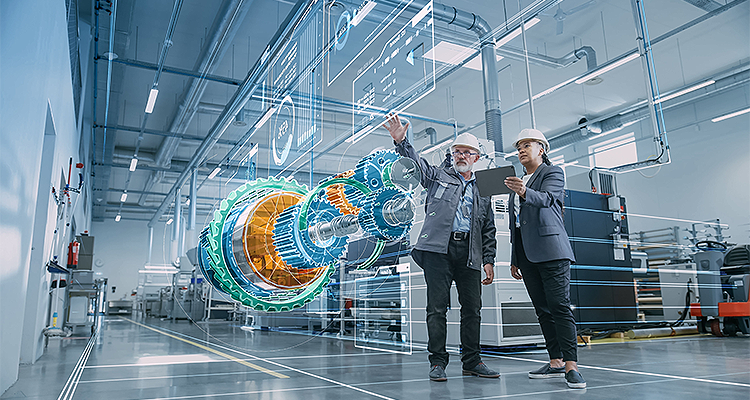
Digital automation has the power to transform, but humans must remain at its heart
The concept of digital automation is nothing new within the manufacturing sector – but is it being used to its full potential? And what role does the human workforce have to play in its advancement? Keith Tilley, CEO of workflow automation specialist, Intoware, explains.
We’ve all borne witness to the digitization revolution in recent years, watching more and more of the items for which we used to rely on paper, moving over into cyberspace. From photographs to important company documents, digitization is bringing improved safeguarding and accessibility to the way business is done.
However, it’s easy to confuse this process with digitalization – a term that sounds very similar but means something entirely different.
Digitization on its own won’t transform a business – but digitalization will. And that’s where the true power of digital automation processes comes in.
Driving innovation
Digitalization is when an organization’s data is processed through advanced digital technologies, such as our own WorkfloPlus, and used for the purposes of digital transformation within a business.
Digitized data is captured and processed, presenting a wealth of data that allows a company to analyse its systems and processes and, in turn, drive major change within the way it operates.
The pioneering researcher on digital transformation, George Westerman, summarizes it perfectly, saying: “When digital transformation is done right, it’s like a caterpillar turning into a butterfly, but when done wrong, all you have is a really fast caterpillar.”
It’s something we’re seeing play out now, as the world watches the fast-paced development of AI with bated breath.
For manufacturers, it’s important to take the time to understand the many possibilities that lie on the other side of digitalization, and the benefits that harnessing data to create new automated processes can bring to the sector.
However, it’s also equally important to ensure that digitalization considers the needs and requirements of the real people working within the business day-to-day – a task that can be easier said than done, when not approached correctly.
Workforce input
The buy-in and support of the workforce is a critical yet often overlooked factor when businesses are undertaking digitalization and implementing automated workflows and processes.
The potential benefits and time and cost efficiencies that automation can offer are often counteracted if the employees using the technology feel disengaged or frustrated with it.
So, it’s important to make sure they’re connected from the outset by involving the workforce in the creation and development of digital workflows and processes.
We encourage our customers to gather insight from their employees to help shape the creation of automated workflows.
Experienced team members often have their own ways of doing things and can help improve processes by sharing their experiences during the development phase, be it time-saving initiatives, record keeping techniques, or ways to boost customer satisfaction.
By involving employees in this process, companies can reap the productivity benefits that come when new technology assists and supports real working practices and methods and be assured that their team feels connected and welcomes digital transformation into the working day.
Powerful potential
When introduced in this way, with real people at its heart, digital automation holds a wealth of enormous potential for the manufacturing sector.
Digital processes can be created and rolled out across mobile devices, including via wearable technology, and the data captured and stored securely to allow for further evolution of systems and processes within the business.
From machinery set up and installation, to maintenance, repair and operations, digital workflows have the power to improve productivity and reduce machine downtime, streamlining processes to ensure they are standardized and fully compliant at every stage, with data collection and reporting happening in real-time.
Step-by-step digital guides and the ability to document images within the system means audit trails are captured and recorded, and evidence is available at the touch of a button if recommendations for equipment upgrades or fixes are made by technicians.
And, third-party maintenance procedures can also be inputted, with reporting tools established to provide transparency and upkeep supplier warranties.
Harnessing expertise
Another important benefit that comes from combining digital automation with people power is the ability to harness the expertise and experience of the workforce, for the purposes of training and developing the next generation.
The invaluable insights that employees who have been with a company for years have stored in their minds can be captured and translated into digital instructions and processes.
This data can then support with the training of new workers, ensuring that as the workforce naturally turns over with age, the important knowledge and expertise of those valued members of the team is retained and passed on through the generations.
In turn, creating a truly connected workforce that brings the digital and human minds together.
For a list of the sources used in this article, please contact the editor.
Keith Tilley
www.intoware.com
Intoware is at the forefront of digital workflow automation. Its flagship product WorkfloPlus was the first software developed for mobile use to take advantage of both Mixed and Augmented Reality. Accessed via mobile, tablet, desktop and wearables, WorkfloPlus empowers connected workers to save companies time and money whilst ensuring quality and accountability.