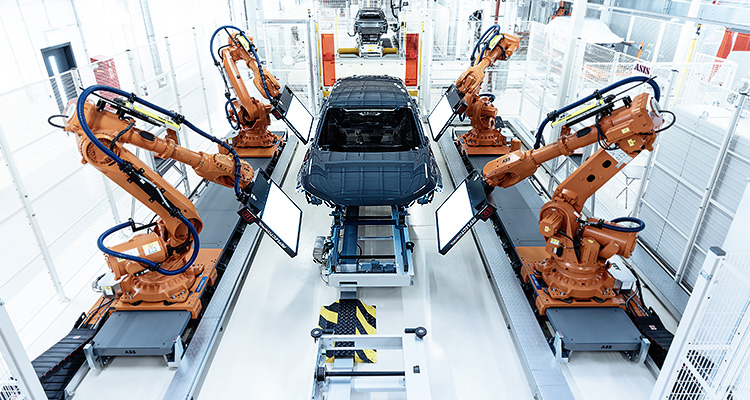
Discover Audi’s ambitious roadmap to achieving e-mobility
Confirming its dedication to sustainability, prestige automaker Audi will gradually expand its electric portfolio. Based on this, Audi is now taking steps to prepare its global facilities to produce all-electric cars, building on its existing global production network to achieve this vision.
The company is bringing its global production sites into the future, investing in existing plants so they are as efficient and flexible as newly built production sites or greenfield plants. Audi wants to make manufacturing flexible and resilient to ensure it will be future proof in the long term. As such, Audi Production has created the 360factory; a vision of the future to help navigate the challenges ahead. The approach places equal emphasis on cost-effectiveness, sustainability, flexibility, and attractiveness.
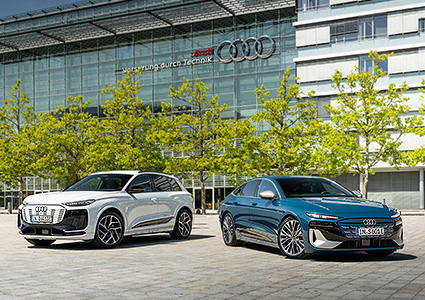
By the end of the decade, Audi will be making electric-drive models at all its production sites worldwide. To achieve this goal, it is relying on highly qualified staff and will make all employees fit for the future. By the end of the decade, all production sites will be producing at least one all-electric vehicle model.
“We use this transformation phase to make our production sites future ready. The Production of the future for us has four main focuses, that’s why we call it Audi 360factory”, says Gerd Walker, Board Member for Production and Logistics at AUDI AG. “The first is flexibility; so, striving to be more flexible in our processes, production, and logistics operations. The second is attractiveness. As part of this commitment, Audi is working on concepts for making the working environment more comfortable for employees and more experienceable for visitors and customers. Our transformation into the 360factory will require the very best minds, even in disciplines not commonly associated with production, such as electronics and software development. The third focus is, of course, sustainability: from our production carbon footprint through to the life cycle of a car. Lastly, the fourth is cost-effectiveness and how we can be more cost efficient in our factories.”
To ensure that the production will be future-ready, Audi wants to improve efficiency in its factories and cut annual factory costs significantly. To achieve this, the premium brand plans to reduce the complexity of its vehicles where it does not benefit the customer. To this end, vehicle development will adopt a streamlined production process from the outset. Audi will also continue to digitalize production and uses Artificial Intelligence to make processes more efficient. Audi has currently identified more than 100 AI use cases in production at different levels of maturity, ranging from idea status to testing and series production. With the Edge Cloud 4 production solution Audi is working on a Cloud based production steering. The solution will make it possible to replace expensive industrial PCs, reducing IT efforts such as software rollouts and operating system changes. “Digitalization and artificial intelligence are enabler for efficient and flexible production. We use these key technologies for the digital transformation in production and logistics on our road to the Audi 360factory,” Gerd Walker adds. Virtual assembly planning saves material resources and make innovative, flexible collaboration possible across locations.
Clear commitment to electric mobility is an important cornerstone of Audi’s sustainability strategy. The company is committed to ensuring sustainability along the entire value chain, assuming responsibility for its employees, the environment, and society, and making sustainable management an integral part of all its decisions and products.
“At Audi, we take a holistic approach to sustainability and resource preservation, exploring efficient water use and biodiversity concerns. By 2025 all our production sites worldwide will be net carbon neutral. Important steps to achieve this goal include generating renewable energy in-house and using innovative technologies to create more circular value chains where resources used are utilized in closed cycles,” says Gerd Walker.
Audi extends this commitment to the circular economy to its supply chain and production processes. The Q6 e-tron series, for example, built in Ingolstadt, is the first fully electric high-volume model manufactured at a German Audi site. Simultaneously, Audi is consolidating new skills and technologies at its company headquarters with the assembly of the newly developed high-voltage (HV) battery for the Premium Platform Electric (PPE). Thanks to the new battery assembly, the company is gradually increasing the vertical range of manufacture for fully electric models and gathering experience for battery module production further down the line.
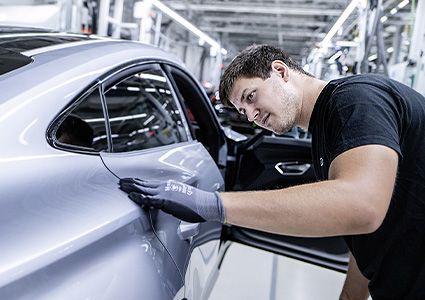
“We decided to locate the battery assembly here, near our electric car production for logistical purposes and to increase the value chain within our factories, which makes sense as they are key components for our electric cars,” Gerd Walker continues. “We have been producing electric cars since 2018, demonstrating not only our capability but also our production flexibility. The Audi Q6 e-tron is the first all-electric model to roll off the production line in Ingolstadt alongside the Audi A6 e-tron, and production of all-electric cars will gradually start in Neckarsulm, San José Chiapa, and Győr too. By the end of this decade, all production sites will be producing at least one all-electric vehicle model. This is an important phase for all sites as we can optimize our processes, incorporating technologies and expertise from other plants.”
To ensure it will be able to respond more flexibly to fluctuations in customer demand or production program, Audi will make its manufacturing processes even more flexible. “We want to structure both product and production, so we get the optimum benefit for our customers,” Gerd Walker explains. Audi produces the Q6 e-tron and the A6 e-tron on one joint assembly line. The Audi A3 and Audi Q2 with combustion engines are being made on another assembly line within the same plant. Electric models will then gradually replace the combustion cars in this production site.
“As I touched on earlier, to create more circular value chains, we use recycled materials where possible, from windshield glass to upholstery fabric. In addition to keeping post-consumer secondary materials in a closed loop, post-industrial materials are also recycled. The primary goal in this regard is to reduce CO2 emissions. With the Aluminum Closed Loop launched in 2017, Audi is demonstrating the responsible handling of aluminum. Aluminum sheet offcuts produced in the press shop are returned to the material cycle. By recycling aluminum waste in this way, the company uses up to 95 percent less energy to produce aluminum than would be necessary for primary aluminum.”
The Audi brand stands for premium quality, the forward-looking and sparing use of resources, and environmentally friendly production. Through its environmental program Mission:Zero, Audi is consolidating all related environmental protection measures.
Since it was founded in 1909, its cars have combined sportiness, cutting-edge design and “Vorsprung durch Technik”. “Audi is a progressive premium brand, well positioned to further push the e-mobility transformation. It’s not purely about selling cars; from infrastructure to digital technology, it’s an entire ecosystem and we want to offer our customers a premium experience. Audi takes its responsibility to people and the planet seriously; not only for employees, but also for the people and the natural world in the regions where our sites are located and beyond,” Gerd Walker concludes. “We promote education and charitable organizations, culture and sports. Through the Audi Environmental Foundation, we are proud to support research into new technologies and scientific methods for a livable future.”