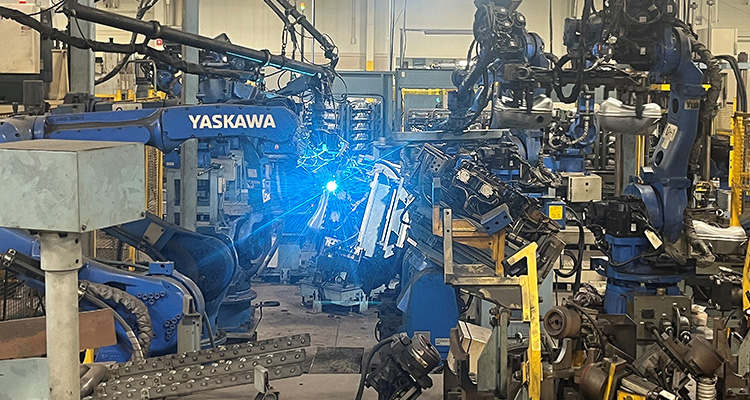
Discover how Newman Technology leverages its industry relationships to provide more efficient and sustainable products
For over 25 years, Newman Technology has produced quality parts and developed solutions for the motor vehicle markets. One of the top suppliers of exhaust, door frame, and exterior trim products in North America, the company is renowned for its commitment to quality, innovation, and continuous improvement. Poised for further expansion across North America, Newman Technology has already experienced significant growth through the spirited dedication of its associates and the pioneering vision of its leadership. Bob Reed, Senior Vice President and Plant Manager, elaborates on the scope of Newman Technology’s manufacturing abilities.
“Our company serves as the North American subsidiary of Japanese manufacturer Sankei Giken Kogyo (Sankei), based in Tokyo. Founded in 1987 on Newman Street in Mansfield, Ohio, we moved to our current location on Cairns Road in Mansfield in 1989. Beginning with a facility spanning less than 100,000 square feet, we have since grown to a footprint of well over one million square feet of manufacturing space, with locations in Ohio, Alabama, and Mexico. Historically, our role within the manufacturing industry was that of a Tier 1 automotive supplier, focusing on exhaust systems, door sash systems, as well as exterior trim and underbody frame assemblies. Additionally, we boast full design and development capabilities in our Ohio R&D Center, such as full exhaust testing. Our core manufacturing expertise is in stamping (including stainless, high-strength steel and aluminum), tube bending, co-extrusion, roll forming, and full ranges of mig, tig, and laser welding,” he begins.
Vice President of Planning and Development, Brian Baker, sheds light on Newman Technology’s approach to research and development when it comes to creating innovative products. “With design and engineering teams meeting monthly with our top management to review ideas for new and improved products and processes, our R&D procedure is thorough and robust. Our teams identify the niche where each idea fits, develop target metrics and schedules for achievements, and follow up with monthly progress reports. From the outset, our North American R&D has been dedicated to refining our existing designs and technologies, while our parent company in Japan has focused on pioneering brand-new parts and processes. In recent years, we have shifted our efforts towards original designs for alternative products, drawing upon our nearly 40 years of manufacturing experience to create innovative products that are both consumer and manufacturing friendly. Moreover, we adopt a common sense approach to leverage our existing technologies across various applications to enhance the quality, manufacturability, and cost-effectiveness of our new products.
“Lately, we have been collaborating with Sankei and another company in Japan to develop parts using a lightweight and strong resin bubble foam for automotive applications focused on insulation and noise reduction. We are also exploring ways to leverage the lightweight and durable properties of this material to apply to products in the warehousing and container industries at a significantly reduced cost. Furthermore, in partnership with a Lithuania-based company, we have been developing products that utilize millimeter-wave technology for radar applications, thereby improving their performance in all sorts of adverse weather conditions,” he informs.
Alongside its focus on innovation and R&D, Newman Technology is constantly exploring new manufacturing technologies to adopt. “By working with our engineers and supply partners, we strive to find innovative ways to implement new technologies, particularly automation, into our operations. One of our most notable accomplishments involves automating some of our less value-added processes, such as loading finished parts into shipping containers at the end of the production line. Prior to automation, our exhaust systems, which measure over 20 feet long, necessitated two team members to manually load, verify, and count each part into the rack. We have since been able to streamline that process by implementing automation at the final station of our production line, thus reducing the need for manpower while enhancing accuracy in part identification and labelling, optimizing cycle times, and mitigating the risk of human error. Additionally, we are on the verge of introducing collaborative robots that can safely work alongside our human employees to perform various tasks, including sealer application and weld grinding,” says Brian.
Technology and sustainability are two subjects at the heart of many conversations in the manufacturing milieu. Brian addresses both of them in discussing how Newman Technology is working to assist the widespread transition to electric vehicles. “Although the industry transition plans tend to be more conceptual than set in stone, we are well aware that the transition is just around the corner, and it is a big deal for us. To offset some of the anticipated effects it will have on our business, we are working on strategies to diversify our product base while maintaining our core product competencies. Throughout the transition phase from internal combustion engine (ICE) vehicles to battery electric vehicles (BEVs), we aim to continue manufacturing and improving our ICE-related products. At the same time, we are making the necessary investments to adapt and position ourselves for future success by developing the capability to fabricate products utilizing high-strength, lightweight materials,” he reveals.
True partnerships
Newman Technology’s eagerness to rapidly embrace new technologies and cater to emerging trends has been empowered by partnerships that have been pivotal to its growth and innovation over the years. “Throughout our history, we have fostered too many crucial collaborative relationships with both our customers and suppliers to be able to only highlight a few of them. Each of these partnerships has brought unique benefits to our organization. In that same respect, our affiliation with our parent company in Japan has been instrumental in enabling us to integrate its top offerings in manufacturing and product technologies with the unique requirements of our local market. Sankei has always provided us with the flexibility to tailor our systems, programs, and investments to what works best for us in North America. We truly learn from each other and promote communication, coordination, and mutual collaboration to drive the most optimal results for our respective regions.
“When it comes to our supply chain, we prioritize and rely on consistency, communication, and true partnership. All our expectations are outlined in the Supplier Quality Manual that we share with each of our suppliers and review with them during onboarding. To strengthen our supply chain relationships, we hold monthly meetings with key suppliers to review their performance in quality and delivery. Likewise, these meetings are an opportunity for them to feed back to us on how we are performing for them, suggest any changes or ideas they might have, and work with us to implement improvements. We also help train supplier staff to gain a better understanding of our company culture and values, which ultimately empowers them to operate as efficiently as possible while respecting our company values. Through these efforts, we aim to provide and maintain robust systems for production and quality as well as to ensure timely open communication to develop mutual cooperation and coordination,” Brian states.
Continuous improvement
Poised for further expansion across North America, Newman Technology harnesses cutting-edge technologies and collaborative partnerships to fulfill its mission of delivering unparalleled solutions for the automotive sector. From the use of lightweight materials to advanced automation, the company’s continuous pursuit of improvement positions it at the forefront of the manufacturing industry.