Discover how SPP Pumps’ advanced pumps shape a sustainable industrial landscape
For close to 150 years, SPP Pumps (SPP) has been a top manufacturer of centrifugal pumps and associated systems, and a global leader in design, supply, and servicing of pumps and high-quality equipment for a wide range of applications and industries. As a UK-based pump manufacturer, its precision-engineered pumps and associated systems are installed both domestically and internationally, providing crucial high integrity services. SPP’s services cater to diverse sectors such as oil and gas, industrial water and wastewater treatment, power generation, construction, mining, and large industrial plants. Alok Kirloskar, Managing Director, tells us more about the company’s journey.
“Next year, SPP will celebrate its 150th anniversary, having been in business since 1875,” he opens. “While our main focus has historically been on fire and water
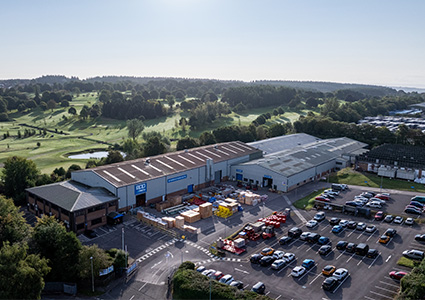
pumps for key applications, we now also specialize in process pumps. When we talk about water pumps, we generally refer to those used in heating, ventilation and air conditioning (HVAC) applications in buildings and data centers, city water supply, power plant cooling applications and seawater lift applications for offshore platforms.
“We have a unique product called a Multistage Multi-Outlet (MSMO) pump that has been used in many high-rise buildings and tunnels around the world. This pump allows us to supply water to different zones of a building using a single pump, resulting in significant space savings, a reduced number of pumps, and a simplified building structure as water tanks and pumphouses are no longer required on multiple floors. Furthermore, we have also expanded into process and industrial applications, including pumps for petrochemicals and new segments such as sustainable aviation fuel and hydrogen,” he continues.
Bob Tichband, Chief Operating Officer, joins the conversation to inform us of SPP’s recent strategic investments in machines and machining capabilities. “As a proud British manufacturer, we are committed to supporting our local communities, our people, and their development. Equally, machining is crucial to us as a pump manufacturer, which is why we have our own machine shop. However, we faced challenges in recruiting machinists and encountered issues with our old and outdated machinery. To address these problems, we invested in new CNC machines, with a particular focus on shaft manufacture and other critical activities.
“Notably, we integrated this investment with our apprenticeship program, which is a top priority of ours. We purposely ensured that all new machine tools had the same control system as the ones used in our apprentices’ offsite training, allowing apprentices to operate the machines from day one instead of simply shadowing more experienced employees. By embracing this approach, we are accelerating the development of our apprentices and effectively addressing the skills gap within our organization. It has proven a win-win arrangement, enabling us to bring more machining in-house and reducing the need for subcontracting. From a cultural point of view, investing in new machinery has paid off, earning us recognition from the British Pump Manufacturers Association (BPMA) and the Energy Industry Council (EIC). The machines we have invested in have made such a significant difference that there will be a continued program of investment in this area going forward,” he elaborates.
Beyond key investments in machinery, of which Bob is particularly proud, SPP has also invested in Industry 4.0 technologies and approaches to enhance efficiency, as Alok points out. “Automation is not directly applicable to our business since we manufacture large, often custom-made products with an average component size ranging from 500 kilograms to a ton, making them quite substantial and unsuitable for batch production on an assembly line. Nevertheless, a core element of Industry 4.0 involves sensors and data collection from these sensors. While we may not employ robotics for automated mass production, we utilize sensors along with our own software which we have developed in-house, called Phoenix. This software comprehensively tracks the hours required for each job, the personnel involved, the location, operations, and duration of machine usage for a specific task. It runs in the background, handling tasks such as planning and resource allocation, making it a true Industry 4.0 solution where software and sensors handle the operational logic. Still, due to the size of our components, the physical work still needs to be done manually,” he says.
On the topic, Bob adds: “Artificial intelligence (AI) is also something we are beginning to adopt and invest in, with strategic plans to integrate it further. We are consistently pushing boundaries in the development of our products, positioning ourselves at the forefront of the industries in which we are active. I would say that we are one of the largest pump companies in the world – if not the biggest – in fire protection. Additionally, we are extremely innovative in the water sector, with a particular focus on pump efficiency, energy reduction, and positive contributions to the environment through our product development.”
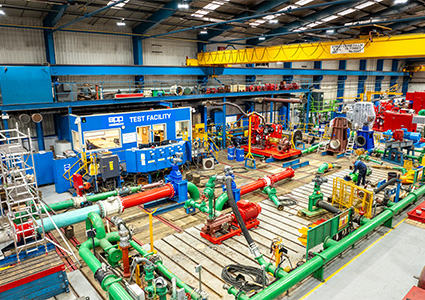
When it comes to sustainability, SPP has implemented a wide range of improvements within its factory to minimize its carbon footprint. “At the moment, we are formulating our road map to carbon neutrality by identifying practical measures and steps we can take to reduce both the carbon emissions generated by our processes and the embedded carbon in our products. As sustainability is a big focus area for us, we have implemented numerous measures to ensure that we are only using energy from renewable sources. In addition, we are actively improving aspects such as factory lighting, which has been switched entirely to energy-efficient LED lighting, not only enhancing efficiency but also creating a far superior work environment for our factory staff. Our focus now is on identifying products or projects that we can create to significantly reduce our carbon footprint and make a positive impact on the environment,” explains Bob.
Alok goes on to provide us with concrete examples of such sustainable products developed by SPP. “A great illustration of that is our pump as turbine, which we supply to the water companies, allowing us to reverse the pump’s operation and feed power back into the grid for these companies. I believe it is an excellent product that has not only proven successful for us at SPP but has also tremendously benefited water companies by demonstrating exceptional performance in highly demanding situations and environments. Another environmentally conscious product in development is a less damaging pump (LDP) designed to ensure that fish, particularly eels, can move upstream without harm, as the specially designed pumps operate at a slow speed. As a result, we contribute to the preservation of wildlife, which is crucial for the overall well-being of the environment,” he ends.
As SPP approaches its 150th year of engineering excellence, it continues to pioneer innovative solutions that deliver unparalleled reliability, efficiency, and sustainability across diverse industries. From investments in new machinery to fish-friendly pumps, SPP’s commitment to technological advancement and environmental stewardship solidifies its legacy as a global leader in centrifugal pump technology.