Discover Multy Homes’ mission to create beautiful, functional products from waste streams
There are many companies out there that convert waste into raw material, and there are also many existing companies using recycled raw materials, but there are very few that do both,” begins Rod Anderson, Chief Operating Officer at Multy Home (Multy). “Multy is a very innovative company that has grown from its roots of buying and selling goods, into an end-to-end organization that collects waste, converts waste into raw material, manufactures finished goods, and distributes these to retail spaces.”
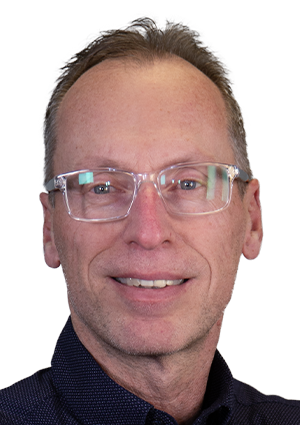
With a unique operating model and the ability to collect and transform waste material, Multy is indeed one of a kind. The company’s tagline, ‘turning waste into wonders’ is more than a marketing exercise, and instead is the motto that fuels the entire organization’s approach to innovation and sustainability.
“Environmental sustainability is at the core of everything we do,” Rod continues. “Every week we consume plastics made from 120 tons of postindustrial waste, 250 tons of waste rubber, and 60 tons of automotive scrap parts. We’re becoming increasingly involved in materials science research, and we now have two PhD polymer scientists within the business to focus on the development of raw materials.
“We do produce a significant percentage of our raw materials, and our trusted partnerships make the rest possible. EPL Plastics is a local company to us, for instance, and as one of the leaders in making recycled plastic resins, we’ve experienced mutual growth and success. We’ve also recently invested in our own manufacturing operations with the help of equipment partners in Europe. Specifically, Next Generation Recycling (NGR) has been invaluable in helping us establish a base for recycled material production in our Canadian operation.”
Elaborating on the company’s history and impressive evolution, Rod continues: “Multy was established in the 1990s by the Erdman family, and who are still very much involved in the business with Derek and Norman Erdman currently at the helm. The company started by selling and distributing industrial products, but the first foray into manufacturing was sparked by a commitment to finding a way to recycle PVC pool liners and transform them into functional flooring.
Product range
“That’s the genesis of the business today; what started out as a mission to reduce the cost of materials and manufacturing has evolved into an ever-growing curiosity around utilizing waste to manufacture world-class products. Making beautiful things from other peoples’ waste is truly part of our DNA and this belief has fueled our expansion into other categories, channels and geographies.
“Our operations now include rubber sheet extrusion, compression molding of flexible rubber products, and injection molding of plastic products. In terms of geographies, we’ve expanded our presence into the European market in recent years with a manufacturing, sales, and distribution base in Poland. In fact, the UK is currently our biggest market outside of North America.”
Turning to Multy’s product portfolio, Rod adds: “100 percent of our domestically manufactured products are made using 100 percent recycled materials and we are continuously working with offshore vendors to increase our recycled content. Our current products fall into one of three categories: functional flooring, lawn and garden accessories, and planter pots. Functional flooring includes products like indoor and outdoor rugs, entrance mats, rubber mats, plastic boot trays, and floor protection products. Our lawn and garden accessories encompass garden edging, deck tiles, pavers, umbrella stands, and privacy screens.
“Lastly, we started producing indoor and outdoor planter pots around eight years ago, and we’ve grown to be a leading provider of plastic planters. Around 70 percent of our plastic products have typically been black in color due to the nature of recycled materials. However, with the evolution of recycled material science, we’re able to offer more consistent colors. We’re now producing planters in yellow, white, blue, and green, for instance, and we’ll continue to evolve our product portfolio in line with developments in recycled raw material science. In fact, the number of SKUs made from REDU materials has tripled between 2024 and 2025 due to our ability to produce an expanded color palette from recycled resins.”
New showroom
Having been a very innovative product company for a long time, Multy is now concentrating on sharing its sustainability and innovation story, especially given its continued emphasis on material science. “To share our message and motivation with the wider community, we’ve recently launched our REDU Materials brand,” Rod reveals. “REDU will provide customers with full traceability of where the raw material came from, the waste used to produce it, what finished goods went into the process, and the distribution journey required to get the product on the shelves. We’re working closely with our suppliers and producers to ensure that materials meet our requirements for REDU branding.
“We can then include REDU branding on products made from recycled materials to emphasize that the product has a positive environmental impact. Although we’re only at the beginning of the REDU brand journey, we hope that in time, consumers will connect REDU and Multy with positive environmental benefits that you wouldn’t typically associate with plastics.”
Multy has also invested in a state-of-the-art showroom, as Rod explains. “The development of a new showroom has been a key project for us over the last year or so and is an excellent vehicle for us to showcase our story, especially as we continue to invest in material science. The showroom stemmed from an idea to create an interactive and immersive experience for our customers and colleagues to learn more about our sustainability story.
Major investments
“The showroom is a very valuable, inspirational, and multipurpose space. As well as the experience itself, the showroom also provides meeting spaces, an 80-seat theater for communication or networking events, and a dedicated place for internal training. It’s a great resource for our employees to be immersed in our products and the as technology that helped create them. Our innovations are made possible by our team of curious, creative, and innovative people. Feedback on the showroom has already been extremely positive, and our employees are more inspired by what they do every day.”
On the topic of investment, Rod is keen to highlight Multy’s positive relationship with its private equity investment partner, Novacap. “Novacap have been very supportive of Multy’s growth and strategic direction, and have supported us through investments in product development, infrastructure, and technology,” he states. “These investments are key to managing our inventory and optimizing our distribution networks as we grow.
“We’ve invested in technology to produce plastic raw materials from waste, as well as in the production of rubber raw material using scrap from the automotive industry’s manufacturing process. We’ve also invested in process monitoring technology to evaluate our own operations, as well as expanding our capacity in both our rubber extrusion and compression molding facilities.”
To finish our conversation, Rod turns his attention to the future. “2025 is a promising year for Multy and our strategy is clear; we’re increasingly investing in material science and production capabilities as we strive to strengthen the foundational parts of our business,” he says. “With the recent addition of our showroom and the REDU business, alongside many other product development and marketing efforts to come, we will continue to share the Multy story.
“When thinking about the next five years, there are our standard goals like doubling the size of the business, introducing new products, and breaking into new markets,” Rod concludes. “However, while those ambitions are important, we’re also concentrating on what we do internally to continuously recycle more, reduce the energy we consume, and minimize our overall environmental footprint.”