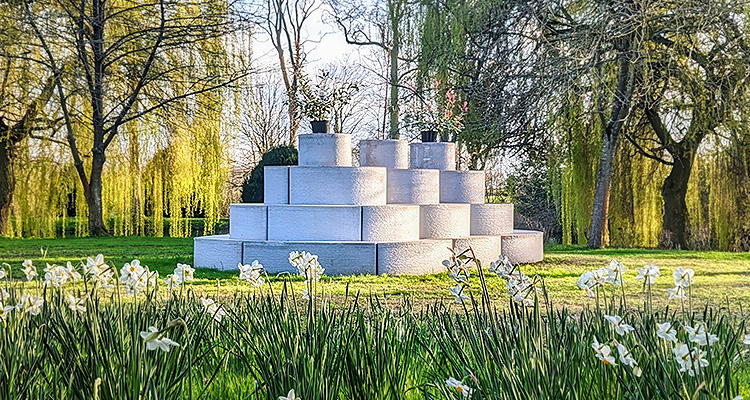
Discover Versarien’s innovative product portfolio, which delivers a positive impact in a variety of industry sectors
Versarien plc (VRS) is an IP-led advanced engineering materials group that utilizes proprietary technology to create innovative engineering solutions. VRS holds more than 120 patents covering areas including the manufacture and use of graphene and related materials (GRMs) in diverse applications. It develops and manufactures advanced materials and products globally through several subsidiaries and has a wide portfolio of high-quality verified products.
Manufacturing Today is introduced to the business by the group’s CEO, Dr Steve Hodge. “The company was incorporated in 2013 and purchased a business called Total Carbide Limited, a leading European manufacturer of sintered tungsten carbide parts primarily for arduous environment applications in the oil and gas industry. VRS was floated on the Alternative Investment Market (AIM) on the London Stock Exchange with an ambition to acquire proprietary technologies coming
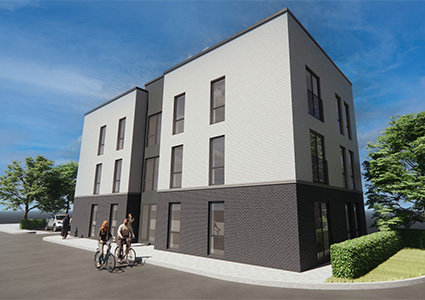
out of UK universities and scale them up. One particular technology was graphene manufacturing. Graphene was first isolated in the UK in 2004 at University of Manchester by two Nobel prize winning scientists, Prof Sir Andre Geim and Prof Sir Kostya Novoselov. In 2014, VRS acquired 2-DTech Limited, the first graphene spin-out from the University of Manchester.
“I joined the business a few years later in 2017 as Head of Research,” he continues, “when VRS acquired Cambridge Graphene Limited, a spin-out company from the Cambridge Graphene Centre at University of Cambridge with GRM ink technology that I co-developed. Over the years, we’ve continued to grow through the acquisition of other advanced materials and technology businesses in strategic areas, in particular entering the energy storage sector through acquisition of Gnanomat S.L. Based in Madrid, Spain, Gnanomat is developing GnanoCaps comprising graphene/metal oxide hybrid materials for the electrodes that bring superior performance compared to current supercapacitor market standards. GnanoCaps also utilize aqueous electrolytes and mitigate environmental concerns associated with leakage, ensuring safe and sustainable operation.
“We also had the opportunity to acquire some technology that originated from Samsung in South Korea. Samsung was one of the early pioneers in graphene, producing roll-to-roll single-atom thick graphene on copper substrates for the electronics industry. Graphene really is the ultimate limit in terms of what can be achieved with computing and will be an enabler for quantum technologies. In fact, it’s the most conductive, thinnest, and strongest material known to man. We’re now seeing the commercialization of single-atom-thick graphene in several very high-end performing applications. The acquisition in late 2020 came with lots of IP and manufacturing equipment. Today, we still have a base in South Korea, but our business model has changed over the last couple of years and we’re now moving to more of a licensing approach. Today, we manufacture advanced materials in the UK and Spain with focused R&D efforts at the universities of Manchester, Cambridge and Ulster where VRS staff are located and then work with other partners overseas who want to license our graphene-manufacturing capabilities and know-how. The graphene market hasn’t yet reached peak maturity and large volume manufacturing in the UK is rather expensive. While graphene is a very lightweight, low-density material, it’s still quite difficult to ship all over the world. You ideally want to manufacture it where it’s going to be needed, which is why we’ve become more collaborative in our approach and licensed out our technology. We’ve got two licensees in South Korea and one in Brazil, with our intention to license in other key regions too. As well as providing expertise on the manufacturing side, we’re also helping our partners grow the market and support their customers,” he shares.
“We’re also developing added value products, targeting different sectors. Graphene is an amazing material, offering something for almost every sector. In the last few years, one area of focus has been construction, an industry that generates massive CO₂ emissions. Eight percent of global emissions come from cement production, so we’re utilizing graphene admixtures that we call CementeneTM and modern methods of construction to find ways to reduce cement usage and to be more innovative, using less material but maintaining or enhancing performance level. Having invested in a robotic-arm printer for developing graphene enhanced cementitious materials, we are now pioneering 3D Construction Printing (3DCP) here in the UK.”
“I joined VRS when it acquired the robot,” adds Ben Harries, Head of 3D Construction Printing, “to assist with efforts to identify applications, design solutions, and to commercialize the technology. In line with our strategy of moving from manufacturing to selling our expertise and licensing, we’re also offering consultancy services for clients who want to integrate 3DCP into their projects. For example, we might work with a client who already has a design and just needs to make it printable, or we might provide a full service from design to production. Equally we might find ourselves assisting with the formulation of a technological strategy or simply offering general advice to various sectors looking to adopt 3DCP. We’re receiving positive feedback from clients on the speed and flexibility of our services, and we are always working to streamline our processes for an even better experience.
“I think 3D printing signals the start of a bigger trend, one of construction automation, and with that comes certain additional benefits. For example, construction is still one of the most dangerous sectors to work in. There is all manner of dangerous equipment and machinery, with hazards all over the place, which can and do cause injury or death. Some of these can only be mitigated and not removed entirely, therefore, introducing more automation takes people out of harm’s way. Other potential benefits of autonomous construction are precision and repeatability, increased speed and reduced waste, and of course the reduced cost and carbon which can come with these things. Whilst it would be wrong to say that 3DCP inherently offers all these benefits, if you have a suitable use case and a thoughtful strategy for implementation, you are well on your way. The benefits will increase as the technology and materials evolve and the regulatory frameworks catch up to be able to support this way of working.
“One of our biggest efforts is in trying to produce printable mixes here in the UK that are lower in carbon, working alongside Balfour Beatty’s Highways division. Combining 3DCP with materials such as graphene could ultimately produce stronger, slimmer structures with lower carbon footprints, so we are in a good position to be thinking about how alternative materials and technologies can help to reduce our impact on the planet.
“Also,” adds Steve, “there is a significant skills shortage in the sector, we’ve got an ageing workforce and we’re losing skills at the top but not replacing them.
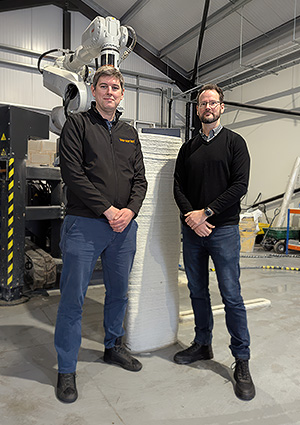
Construction hasn’t really been seen as an exciting industry to work in, but I think with digitization and new automation tools, the sector is becoming quite attractive to the younger generation, which will help to support industry growth and make it more sustainable in the UK.
“We’re still very much in the development phase but we’ve always had to be agile; to pivot and realign ourselves to ensure we’re doing relevant work. We think that by focusing on construction, which has the biggest impact on climate change, we can make a difference with both the materials that we’re using and the technologies,” Steve shares.
“The year ahead is looking quite promising,” he continues. “Our commercial pipeline has never been healthier, and we’ve recently been awarded a large government grant for the work our Gnanomat team is performing. We raised money on the stock market during 2024 and part of that capital was to be put towards purchasing construction testing equipment for our own in-house capability. That has now been commissioned, so we’ll be able to accelerate our graphene-in-concrete testing. The nature of concrete testing is very slow; we must often wait 28 days or more to get results and feedback. So, having in-house capability is a great addition and it allows our staff to develop more skills.”
Indeed, championing innovation is at the core of VRS’ operations and the company has joined BridgeAI, an Innovate UK-funded program with a mission to drive the adoption of AI and machine learning (ML) in sectors of the UK economy with a high potential for growth. In the latest round, which is focused on construction, VRS has set some challenges relating to parametric design and material monitoring, which it sees as two key challenges for 3D Construction Printing.
“It’s a thought-provoking time for advanced materials at the moment,” Steve adds. “Over the last ten years, in Europe we’ve had the EC’s Graphene Flagship initiative which was a ten-year program with one billion euros of funding with the aim to mobilize researchers, academics, industry and national programs to tackle major challenges in science and technology using graphene. We’re entering a new phase where multiple initiatives have come together to create the Innovative Advanced Materials Initiative (IAM-I) and VRS is already signed up as an industry member, aligning with its four key strategic areas of construction, energy, mobility and electronics. The UK’s Henry Royce Institute for Advanced Materials has also recently launched the National Materials Innovation Strategy outlining materials innovation priorities and VRS hopes to be at the forefront and support the UK achieving its innovation and decarbonization ambitions.”
“We’ve been through a period of cost cutting over the last two years, and have divested one of our two mature businesses. The aim, now that we’re fully focused on advanced materials, is to grow the business sustainably. We’re trying to shift from R&D to more commercial sales of our products. We’ve got products to sell and projects to deliver that Ben is driving on the 3DCP side. As we have been R&D intensive, we’ve had to be reliant on some grant funding, but we’re now hopeful that with our healthy commercial pipeline and more projects coming to the table that we can drive the business forward. I want VRS to be one of the world’s leading advanced materials businesses,” he concludes. “I am confident that our strategic direction, combined with our focus on commercializing intellectual property and securing strong partnerships, will help us navigate challenges and deliver robust growth. Our diverse portfolio of technologies is setting the stage for continued success.”