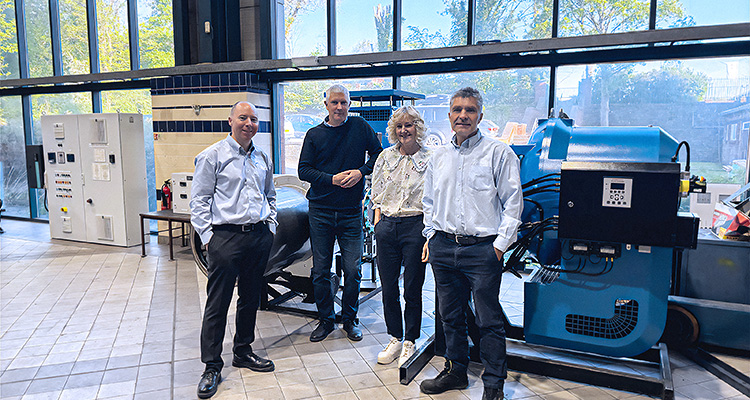
Dunphy Combustion’s burners heat factories worldwide while cutting emissions beyond regulatory requirements
Dunphy Combustion (Dunphy), a respected family-owned business based in Rochdale, specializes in designing, manufacturing and servicing industrial combustion equipment. The company supplies industrial burners, digital burner control systems, packaged boiler plant rooms, and associated gas boosters. Exporting these solutions worldwide, and every stage of the process – from initial design and manufacturing to installation and ongoing maintenance – is handled in-house. Sharon Kuligowski, Managing Director, shares insights into Dunphy’s background.
“My father, Malcom Dunphy, established the company in 1964. He began his career as an electrical engineer at SuperJet Oil and Gas Burners, which was one of four burner manufacturers in Rochdale and among 60 in the UK at that time. Using his electrical engineering skills, he began servicing burners and eventually decided to create and sell one of his own. This was during a significant transition in the industry, moving from coal-fired boiler systems to heavy fuel oil and diesel gas oil. In the 1970s, there was another major shift with the adoption of natural gas, which marked a pivotal moment in the start of our business as we know it today. My father worked tirelessly until his passing in 2013, leaving behind a legacy of innovation. For the past 17 years, Eddie Kuligowski, our Commercial Director, and I have been deeply involved in steering the company forward,” she recounts.
Over the years, the company has evolved alongside the industry, continuously refining its mission while honouring its heritage to guide current operations. “Throughout our journey, we’ve always stayed at the forefront of innovation. My father invented the axial airflow burner and designed the original T Series burner range, which is still in use today. In my humble opinion, the T Series remains the best airflow burner on the market due to its exceptional laminar flow, something our competitors have not been able to replicate. We were the first to develop touchscreen boiler control panels and to achieve low emissions combustion. Other innovations include the first multi-nozzle low NOx oil burner head. Notably, we received the Queen’s Award for Innovation in 1998 and again in 2010 for our advancements in low emissions combustion. More recently, we have expanded into hydrogen burners. This year, we were honored with the King’s Award for our multi-fuel burner, a highly advanced low NOx burner specifically designed for demanding industrial applications. This innovative burner can seamlessly switch between hydrogen and natural gas, addressing critical safety and performance challenges. In line with our commitment to innovation, we constantly explore new ways to reduce carbon emissions,” Sharon enlightens.
Recently, Dunphy has consolidated its partnership with Bosch, enabling the development of more innovative and sustainable solutions tailored to the multinational’s needs. “We have created a range of burners specifically designed to work with Bosch’s boilers and capable of operating on both natural gas and hydrogen. One of Bosch’s key criteria during the design phase of these burners was to ensure that emissions from the gas were below 80 milligrams for hydrogen, which we have successfully achieved with this design. It is worth noting that the legislative requirements in Europe demand a limit of 100 milligrams per normal cubic meter for natural gas and 137 milligrams per normal cubic meter for hydrogen, so we are significantly below these standards,” Sharon affirms.
In line with its commitment to sustainability, Dunphy now offers a full range of burners for biogas. “While biogas itself is not unique, our ability to simultaneously fire it with other fuels to minimize carbon footprints truly sets us apart. The site may utilize biogas generated through anaerobic digestion, waste, or even human waste, making it a completely green energy source. If a site does not produce enough biogas to meet its demand, we can supplement it with natural gas or gas oil, which gives them flexibility,” Sharon explains.
Matt Brierley, Operations Director, joins the conversation to highlight Dunphy’s Blue Jay project. “Essentially, the Blue Jay Project was a complete energy center solution that we built within our factory, comprising of two 15 t/hr steam boilers, dual fuel ATEX rated burners (Ethanol and natural gas) and all the peripheral components required to complete a turnkey energy center. One notable aspect of the project involved an innovative approach to steam recovery. Although the technology itself is not entirely new, a solution for high-pressure steam recovery from the various processes was adopted. Typically, many sites flash off steam at the process end and return it as a condense back to the hotwell or pressurized de-aerator at approximately 100 degrees Celsius. In this project, the condense was kept at pressure and using special pumps at the process end, the high pressure/temperature condense was pumped back to the energy center and injected directly into the boiler. This approach recovered the flash steam energy which can account for up to 15 percent. This relatively simple approach will result in significant savings, estimated to be £550,000 per year. The whole package then undertook a full factory acceptance test (FAT) and snagging session with the end client, before being fully disassembled, and then reconstructed onsite,” he reveals.
Its adoption of modular manufacturing is a testament to Dunphy’s dedication to continuously exploring new approaches and technologies that can advance its capabilities. “Many years ago, we introduced a shop floor data collection system that integrates seamlessly with our ERP system. As part of that, we have touch screens dotted throughout the facility, allowing employees to access information and utilize scan-on/scan-off features to ensure traceability. We are always on the lookout for new technologies to boost efficiency across the company,” Matt ends.
Dunphy’s legacy of pioneering innovation stretches back over half a century, from its founder’s invention of the industry-defining axial airflow burner to its latest King’s Award winning burners. Today, the family-owned business continues to push the boundaries of sustainable combustion technology, empowering clients around the world to navigate the evolving energy landscape with its cutting-edge solutions and unparalleled expertise.