Energy Industry Embraces 3D Printing
Oqton’s additive manufacturing software helps oil and gas companies find new growth
3D printing, also known as additive manufacturing, is gaining ground across industries. Oil and gas is no exception. Big players see the potential to reduce inventory costs with on-demand manufacturing based on reliable and repeatable 3D printing workflows. The other major appeal of additive technology lies in the possibility of replacing worn parts that are no longer sold or substituting existing parts with functionally superior designs that would be too expensive or impossible to manufacture with conventional methods.
Oqton, the developer of leading additive manufacturing software today, has been a key partner to companies adopting additive manufacturing. State-of-the-art software is the cornerstone of any cost-effective 3D printing workflow. Oqton’s 3DXpert, for additive designers and operators, and Manufacturing OS, for manufacturing automation and planning, enable the set-up of certified and repeatable manufacturing workflows and complete traceability of parts.
Developed in collaboration with industry leaders like Baker Hughes, the software addresses today’s most complex challenges including aging infrastructure, disruptions to supply chains, data management, quality control, increasing part validation costs and long lead times.
Role of additive manufacturing software
In the energy sector, there are five key software capabilities necessary for an efficient additive manufacturing workflow.
Digital Warehouse allows an OEM to define and make available certified digital assets so that they can be manufactured at any location by any certified supplier. OEMs can manage a different catalog of parts for each customer, and suppliers can use available and certified part designs while protecting their IP.
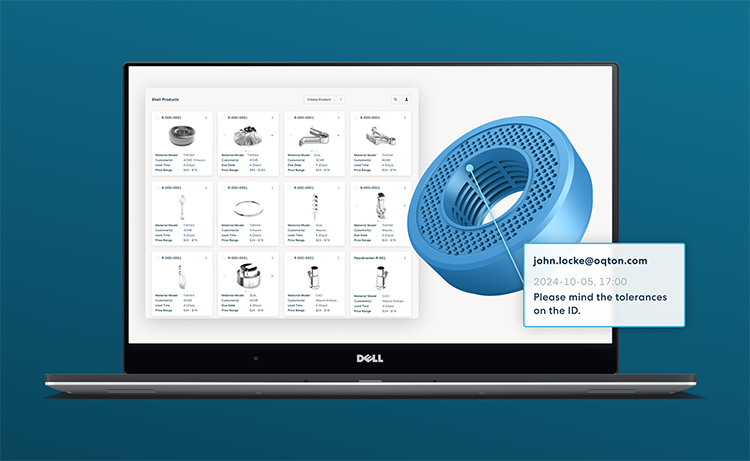
Order Management is an online portal for collaborating with customers. Oil and gas companies can upload a file to get a quote, order parts based on previous orders, or search the Digital Warehouse for the parts they want.
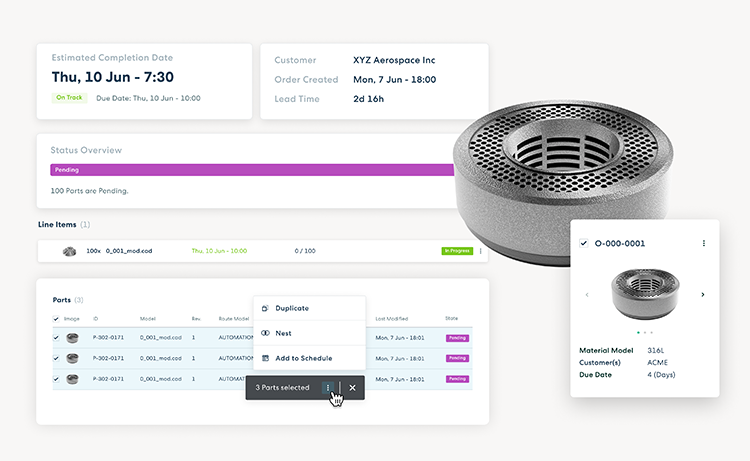
On the portal, users can also configure workflows for different use cases, define the costing and quoting processes, approval steps, required resources and planning of the order availability for each different available manufacturing locations or suppliers.
Engineering Design Solutions. Designers and operators need the right engineering software in order to define a reliable and repeatable manufacturing process. 3DXpert is the leading industrial additive manufacturing solution with a comprehensive toolkit for design, simulation, manufacture and inspection.
MES is a solution supporting additive manufacturing workflows with production order management, scheduling, connectivity with printers, and analytics of factory efficiency.
Monitoring and alerting enables operators to save material and machine time. This solution monitors the print process in real time and sends alerts when anomalies are discovered so that operators can ensure consistent quality. This unlocks significant operational savings and establishes complete traceability per machine, part and layer.
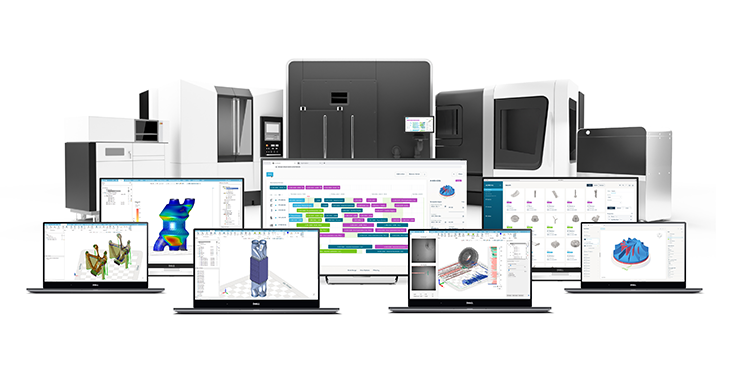
Faster innovation, lower costs
The powerful combination of additive manufacturing and Oqton software brings numerous advantages to the oil and gas industry. One of the most significant is faster innovation. 3D printing allows companies to design and manufacture parts entirely in one location, instead of ordering from multiple suppliers. This speeds up new product development. As a consequence, companies can afford to explore more ideas more quickly and increase the pace of innovation.
Another important advantage of 3D printing stems from its inherently digital nature. It’s simple to gather data about the manufacturing process because everything is connected and tracked digitally. This data, in turn, can be used to optimize manufacturing processes.
Simulation is a perfect example. Simulation technology predicts how a part will behave during the print process, allowing teams to reduce both the risk of errors and the total cost of printing each part. This significantly increases the chances of producing the right part with minimal iterations, saving time and minimizing material waste.
Energy technology company Wärtsilä relied on Oqton’s simulation technology during the development of an innovative 3D-printed pump impeller. Simulation was instrumental in bringing the project to fruition with minimal iterations and material waste.
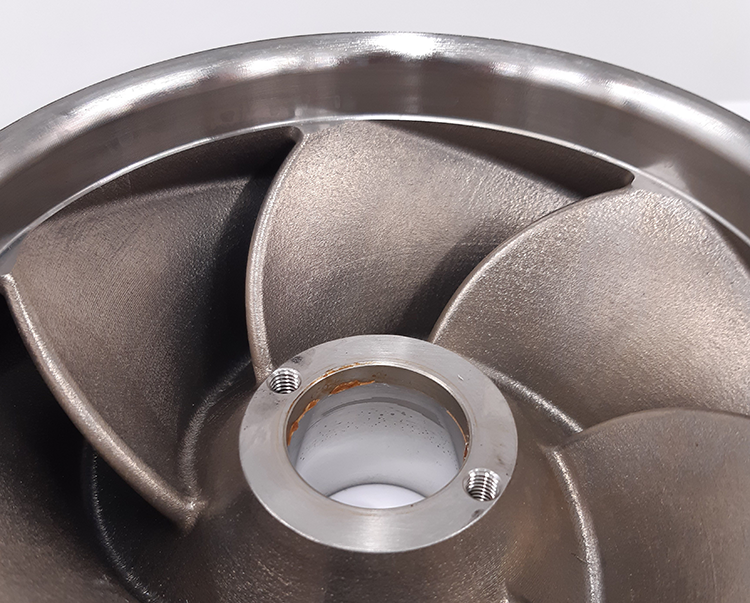
Monitoring is another advantage of the digital nature of manufacturing. 3D printers can be connected to the Internet of Things (IoT) so that engineers can monitor the production process in real time, detect problems as soon as they emerge and automatically implement changes to keep production moving efficiently.
But it’s the prospect of on-demand production that drives most companies to invest in 3D printing. Instead of having a huge physical warehouse, companies can store all the inventory, including the information about part production, in a digital warehouse. When a part breaks, they can order it to be printed or, if they have a machine on-site, they can print it on demand. This shortens lead times, eliminates supply chain stress, and brings manufacturing closer to where parts are needed.
Overall, additive manufacturing offers many ways to reduce costs throughout the supply chain. Additively manufactured parts can often be made in less time and with less labor, both of which have a direct impact on the cost per part. Consider the difference in cost between an assembly that is made from a dozen or more machined parts that must be produced separately and then put together — and a printed part that consolidates all of these elements into one that can be printed in one run, with no need for further assembly.
Widening adoption
Interest in additive manufacturing is growing in the global energy sector, but the applications have not yet reached their full potential. Much of the delay in adoption can be attributed to common misconceptions about the technology, namely that it is too complex to implement consistently.
However, this complexity is no longer a challenge – thanks to software. Oqton Manufacturing OS simplifies workflow planning, tracking and quality control.
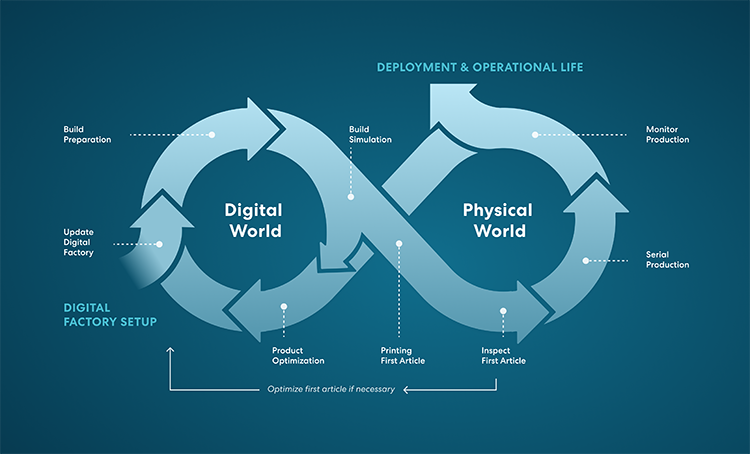
Of course, the energy industry operates in a heavily regulated environment and companies who want to leverage 3D printing must comply with demanding requirements. The American Petroleum Institute (API) has developed two standards for 3D printing in different materials. API Standard 20S (for metals) and API Standard 20T (for polymers) establish basic requirements and process controls for additive manufacturing that delivers parts and components for the oil and gas industry.
Additive manufacturing software works very well with such standards because the requirements can be built into the workflows manufacturers use to manage production. The results of each build are recorded with full traceability to demonstrate qualification at any time.
Oqton achieved an important milestone in the path to using 3D printing for serial production. Together with energy leader Baker Hughes, the company developed an end-to-end AM workflow for the serial production of a Variable Resistance Trim (VRT) component. Built on a fully digital framework, the solution includes simulation, real-time process monitoring, anomaly analysis, and data preparation automation.
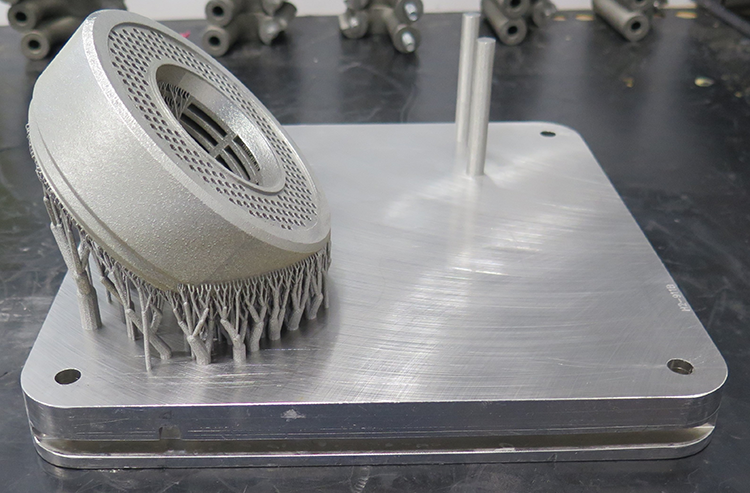
The future of oil & gas
3D printing allows oil & gas companies to innovate faster, make better parts, store parts digitally instead of physically, save money, reduce waste and lower emissions. The key question to ask is not how additive manufacturing will transform the global energy sector, but when.
Companies that wait too long to begin integrating these tools, software and techniques run the risk of not only losing a competitive advantage but missing out on opportunities to reduce total emissions sooner rather than later.