Exel Composites’ sustainable solutions are making waves in industries worldwide
Based in Finland, Exel Composites Plc (Exel) primarily serves as one of the largest manufacturers of composite profiles and tubes, leveraging pultrusion and pull-winding technologies. As a forerunner in pultrusion technology, Exel’s innovative composite solutions cater to diverse customers across a wide range of industries, including wind power, transportation, and building and infrastructure.
Kim Sjödahl, Senior Vice President of Technology and Sustainability, shares detailed insights into the company’s operations. “Exel is currently the only company
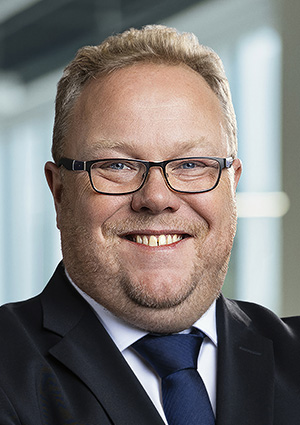
dedicated to pultrusion with this size and global reach. Interestingly, it only began focusing on pultrusion in the early 1990s, as it was originally manufacturing numerous different types of products. Established in the 1960s, Exel initially specialized in explosive electrics, producing detonators and, later, hearing protectors which complemented the detonators very well,” he begins.
Diverse product portfolio
“In the early 1970s, we began producing composites, mostly for sporting goods, with ski poles as our breakthrough product at the time. Notably, we sourced carbon fiber from Mitsubishi Chemical Group, making us the first company to use carbon fiber in Europe. We started experimenting with it and successfully used it to create our ski poles. After trying our hand at manufacturing various objects, we decided to specialize in composites and sporting goods. From the late 1990s, we were operating as an original equipment manufacturer (OEM) for industrial components. Today, our composite products are used in a wide range of applications including wind energy, electrical insulations, automotive, transportation, and numerous consumer goods like broom handles and telescopes. Our diverse product range is a result of our commitment to our processes and materials, rather than specific end-uses, which allows our customers to utilize our products in a variety of ways,” he adds.
Although its products are versatile enough to be used in countless applications, Exel is most active within four distinct industries. Kim sheds light on the company’s offerings to each sector. “Most of our products are components designed for final assembly across various sectors. For example, in the building and construction segment – one of our most crucial sectors – we offer different types of facade profiles for buildings, roof components and windows, along with windowsills, window and door frames, window sashes, and more. In the transportation sector, primarily for buses and trains, we produce interior and exterior panels, roof trims, interior coves, luggage compartments, and handrails, among other components.
Green technologies
“Meanwhile, for electrical applications, we provide various types of insulators, such as hanging insulators, fuse cutouts, insulating ladders, electrical motor components, and countless more. Lastly, we are particularly active in the wind industry, supplying carbon fiber spar caps, cable trays, and different types of ladders, while also engaging in various kitting and assembly projects,” Kim elaborates.
At the heart of Exel’s manufacturing process lies a strong emphasis on eco-friendly practices, which aligns with its ethos. “Sustainability is really important to us, and we view it as a driver for new technologies. Since we specialize in composites, which in many cases have lower greenhouse gas emissions than alternative materials, we can manufacture products with reduced carbon emissions. Moreover, composites enable the development of numerous technologies that are used in green or sustainable products like wind turbine blades, which have had components made from composite materials for a long time. The large size and efficiency of today’s wind turbine blades would not be achievable without pultruded composite materials to make its components, such as carbon flat spar caps. This structural reinforcement was first developed by Dr John Hartley, Exel’s Global Head of R&D for Wind. By producing components essential to the operation of wind turbines, we contribute to the generation of green energy. Therefore, we are committed to directing more of our resources towards green technologies and collaborating with customers who rely on these sustainable components.
“To achieve our goal of being carbon neutral by 2050, we are collaborating extensively with our suppliers to decrease the carbon footprint of our products. Exel is looking at new and alternative raw materials to achieve this, including biobased resins and biofibers, among others,” Kim enlightens.
Composite materials present a significant challenge for recycling initiatives due to their complex composition and structure, which makes separation difficult, especially considering the strong bonding between the components. To address this, Exel partnered with the Kimura project in Finland, which spearheads the development of a circular economy model for composite products by implementing open-loop recycling techniques to transform composite waste into cement. Exel contributes actively to further develop this process and provides waste in the form of composite materials that Kimura can efficiently crush and utilize for cement production through co-processing, without generating any residual ash. Manufacturing cement using alternative fuels and raw materials enables energy recovery, as the organic components in the resins generate heat energy during combustion. This reduces the reliance on fossil fuels in cement kiln operations, as well as reducing the need for virgin raw materials as the waste glass fibers replace them.
Exel’s R&D expertise, collaborative approach, and global footprint sets it apart from the competition. Its composite solutions help customers save resources, reduce products’ weight, improve performance and energy efficiency, and decrease total lifetime costs. Exel strives to be the first choice for sustainable composite solutions globally.