Explore how AESC is leading the global lithium battery market
From its headquarters in Yokohama, Japan, AESC Group (AESC) has established itself as a global leader in the development and manufacture of high-performance batteries for zero-emission electric vehicles and energy storage systems. Since 2007, the company has been building manufacturing capabilities in the US, UK, Europe, Japan, and China to serve the world’s leading OEMs and energy storage providers. Its advanced technology powers over one million electric vehicles and provides more than 20 gigawatt hours of installed capacity for battery energy systems in over 60 countries.
“There are currently more than one million cars on the road powered by our batteries. It is worth noting that we have a proven safety record, as there has never been any incident with our batteries. Continuing this trajectory, we are now expanding our presence in the US and Europe in response to the growing electric vehicle (EV) market,” opens Knudt Flor, CEO of US and Europe.
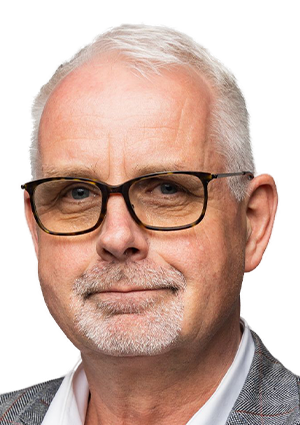
Indeed, the rising popularity of EVs has presented significant opportunities for many businesses. Knudt observes how demand for such vehicles has grown over the past 17 years, since the inception of AESC. “Originally, we were a single supplier to Nissan and offered only one type of battery. Today, there are many different battery types, such as cylindrical, prismatic and pouch, and a variety of new technologies, which have enabled us to gain numerous new customers. For example, we now supply batteries for Renault in France, are building a factory in Spain to serve new customers and have expanded our presence in the US with BMW and Mercedes as our main customers. In the UK, we primarily supply batteries to Nissan currently.
“At the moment, a large portion of our customers require high-technology batteries, and the demand is extremely high in terms of gigawatt hours. In response, we are going to expand our production capacity, starting with the State of Tennessee, where we have a three-gigawatt factory primarily serving Nissan. We are also planning to increase our production capacity in Bowling Green, Kentucky and Florence, South Carolina, with a total of 30 gigawatt hours for each factory, a substantial increase. Likewise, our Sunderland operation in the UK was originally 1.8 gigawatt hours and is now growing to 15.8 extra gigawatt hours. In France, our facility, which supplies Renault, currently has a capacity of nine gigawatt but it will also increase to 24 gigawatt hours. These expansions are a direct reflection of the huge increase in demand in the EV and renewable energy market,” he elaborates.
Zero-defect culture
Going back to his earlier mention of AESC’s impeccable safety record, Knudt lays out the measures in place within the company to uphold such high safety standards. “More than one million cars in the EV market are running on AESC batteries, which I believe is a testament to our proven safety record. For us, safety is all about quality, and quality is achieved through the development of a thorough battery manufacturing process and incredibly tight process control. In line with that, everything we do to ensure quality is based and relies on cutting-edge technology. We leverage a lot of artificial intelligence (AI) and technology in our manufacturing to ensure flawless and repeatable results at scale. Moreover, we foster a zero-defect culture that covers three core areas: product, process, and people. This means that we are not allowed to ship any product with any kind of defect. Every mistake we make internally is treated as a learning opportunity, but we still have a robust quality management system in place to ensure that no defect leaves our facilities. Our zero-defect culture will be implemented in every factory that we build in the future,” he informs.
Quality control 
Knudt sheds light on the ways AI and technology are used within AESC’s manufacturing facilities. “At AESC, our battery manufacturing process is fully automated and carried out using advanced equipment with minimal human involvement. We design our own batteries and take full responsibility for quality management. One of the major challenges in the process is electrode manufacturing, as it is here that the quality of the battery is determined. To produce high-quality batteries, it is essential to have a high yield and to carefully control the quality of the electrodes during the manufacturing process. To that end, we have fully automated quality loops at every step of the process, including X-ray and process control. We use the latest technology and software, including AI, to control the process. Nonetheless, we complement our own software with solutions that already exist in the market to ensure the process is AI-driven and reliable,” he points out.
As our conversation nears its end, Knudt provides an overview of AESC’s approach to sustainability. “As electricity plays a major role in the entire lifecycle of battery manufacturing and usage, we have innovatively designed and operate our gigafactory within the net-zero industrial park, using 100 percent green electricity through a combination of wind and photovoltaic energy as well as energy storage systems. Our long-term goal is to implement this model in every AESC location. While we do not have our own battery recycling facilities at present, our batteries are created with recycling in mind, with the aim of forming partnerships to recycle them. Ultimately, the battery of the future must be fully recyclable in line with the principles of the circular economy, which is essential for success in the market,” he concludes.
Poised to power the electric vehicle revolution, AESC’s unwavering focus on safety and quality has cemented its status as a global battery innovator.