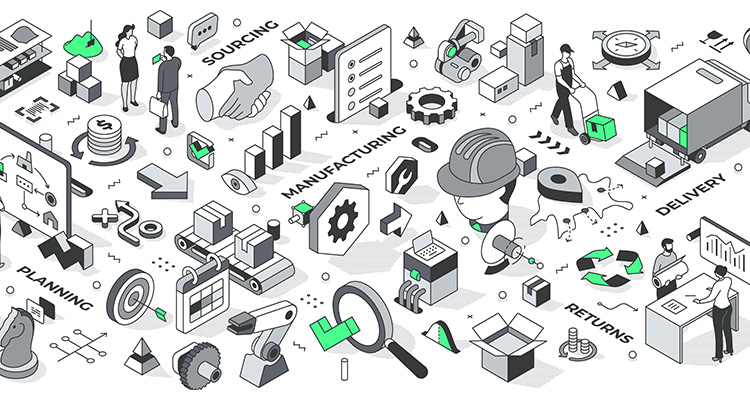
Five steps to a winning inventory strategy in 2025
Forty-nine out of 50 states in the United States require drivers to carry some form of auto insurance. (Live Free or Die, New Hampshire!). Yet the average driver in America files an accident claim only once every 17.9 years. If you’re reading this and you live in the US, chances are you drive, have car insurance – and didn’t make any claims this year. So: is it a ‘smart move’ to stop paying your car insurance bill?
Obviously not! Insurance fees are paid to cover the occasional risk that, hopefully, you don’t end up needing to use. It doesn’t mean it’s wasted; that’s the nature of ‘occasional risk.’ So why do so many executives hang on to the notion that ALL inventory is waste?
Even in a distribution system with 100 percent predictable demand, deterministic transportation lead times, and periodic/batch replenishment, a level of covering inventory is inevitable. Add in variability in demand and uncertain lead times, and you get safety stock. If you don’t use your safety stock, it doesn’t mean it was a waste. You’re buying insurance against the risk of losing demand and potentially that customer you’ve worked so hard to serve.
It’s time to revise our thinking around inventory as something we actively monitor and manage, and not evidence of a crime being committed. Inventory, like insurance, is a choice about risk. Unless you don’t have the right tools, in which case you’re basically a drunk six-year-old losing someone else’s money in a casino. Let’s discuss how to avoid the embarrassment of being a drunk baby gambler.
Inventory strategy and inventory management
Techniques for modeling and optimizing inventory levels given a known set of inputs have been around for decades. But what-if tools for testing alternative inventory strategies remain inaccessible and widely underutilized to this day. A lot of this is because of the basic confusion around management and strategy or planning and design.
Company inventories for raw materials, WIP, and finished goods exist throughout the network. These inventories are tracked and managed by a variety of planning systems. To focus on finished goods, these are typically tracked and managed by an inventory management system that incorporates real-time data and allows for adjustments. However, inventory management approaches typically do NOT support what-if analysis: making adjustments, trying new deployment strategies, and then simulating the results to test out what will happen to service rates before I make those changes.
This is a classic case of selecting the right tool for the right job. Use planning applications or inventory management systems to oversee the day-to-day implementation of your strategic inventory choices. Use a proper supply chain design application to recommend changes and alter strategies as to where your stocking points are, and how to properly balance uncertainty (risk) with your desired service target.
Benefits of creating inventory policies with supply chain design
Supply chain design can help companies quickly get to the bottom of the overall structure and success (or lack thereof) of their inventory strategy. Supply chain design involves pulling together data on your supply chain’s configuration and operations to create a digital ‘model’ of the current system. With this model, you can test changes – small, medium, and big – and measure key metrics: cost, service, sustainability, risk, and more.
- With supply chain design, you can answer inventory policy questions like these:
- What inventory target approach properly balances service and cost?
- What happens if I shift my push/pull boundary up an echelon?
- What SKUs should be stocked in which DCs?
- What happens to last mile delivery (transportation) costs if I change my stocking policies?
- What happens to my system inventory investment and working capital if I shift inbound supplies from overseas to in-country? Is it worth the move?
- What is my ‘perfect order’ service rate after I make a change? What about the per-customer service rate? Is it an order-based service rate or line item fill rate?
Five steps to a winning inventory strategy
Consolidate and unify the relevant supply chain data
The supply chain comprises various elements and factors contributing to streamlined operations within your organization and your inventory planning and management. To model a change to your inventory strategy, you must bring together the relevant data:
- Nodes of your network
- Products to be modeled
- Customers and customer demand
- Order history
- Lead times and/or transportation modes
- Suppliers
Finish the model: structure, policy, and business logic
Once you’ve established your physical supply chain structure, you can incorporate inventory policies and contingency rules. What are your current inventory policies and targets? What are your replenishment and sourcing policies?
Additionally, you’ll want to capture and include expediting and compensatory inventory management practices that your operators use: What happens when a stock out occurs? How are stockouts prioritized? How do I ration inventory when stocks get low? How and when do I expedite resupply?
These kinds of policies are happening in your network whether you know it or not. For future state models to operate properly – model validity – the model has to include the logic about what happens under ‘less than optimal’ conditions.
Does your inventory have unique characteristics that you must consider, like the need for cold storage, shelf space requirements, or pharmaceutical regulations and expiration dates? Specific product types require unique storage characteristics that you must account for.
Inventory right-sizing: base case
Simulate the base case and evaluate the outputs. Are there obvious overstocking situations? Insurance is important, but too much insurance truly IS a waste! Right size the current inventory policies and you may find some low-hanging fruit.
Asking yourself why that fruit is there in the first place can be a valuable project on its own. We’ve seen a surprising number of cases where an objective evaluation of the base case of inventory policies has revealed wrong parameters, old inventory approaches, and even some cases where the inventory management system was installed with basic ‘factory settings’ that were never changed. That’s an embarrassment that’s completely avoidable.
Optimizing inventory strategy with multi-echelon inventory optimization
You’ve optimized your base case. Now look to the future. What ideas have the categories managers talked about trying but haven’t been able to for fear of messing things up? What are the bigger changes that the CFO’s office is suggesting but you’ve dismissed for fear of service degradation?
The planners and managers that run the network have many, many ideas about how to make things better. If only they could stop the plane in mid-air and try things in a safe environment. Take their ideas, apply multi-echelon inventory optimization, or simulation-optimization, to flesh out what a new approach would look like. Constrain the number of SKUs at each node and re-optimize. Unconstrain the number of delivery locations and re-optimize. You can get answers to many different configurations. But you’re not ready to change the network just yet until…
Test inventory optimization recommendations with simulation
It looks good in theory. How does it work in practice? You don’t have to hold your breath and see what happens. Optimization approaches simplify the problem to get answers. Simulation lets you test the answers in a digital model to atone for the various sins of simplification. When you’ve got a safe test environment, you’re free to innovate. It’s that simple.
We find that most companies remain unaware that enterprise scale, SKU/order/shipment level of detail simulation is already available and ready to go. Don’t guess at service rates. Simulate and just read them off of an Excel sheet. You don’t need a PhD or specialized hardware anymore.
Fix the plane while you’re flying it
AI and improved inventory visibility have combined to give you a powerful autopilot capability. If you have good technology and processes, you can hand over more and more of the driving to your system. However, autopilot doesn’t tell you where you’re going. If you let the robots fly the plane or drive the car, you can check the map, change your direction, course correct – or even think about getting a faster plane. Car. Whatever metaphor connects. Anyways, operating the supply chain requires operational discipline. Redesigning and improving the supply chain requires deliberate thought and powerful modeling/what-if capabilities. The best supply chain organizations are good at doing both. Looking ahead at 2025, is your organization ready for that challenge? ■
For a list of the sources used in this article, please contact the editor.
By Don Hicks
Don Hicks is CEO at Optilogic. Optilogic offers cloud-native supply chain design solutions that enable businesses to evaluate trade-offs across financial performance, service levels, and systemic risk to design resilient supply chains even in the most dynamic, challenging environments. Its Cosmic Frog supply chain design solution tackles enterprise data at scale, runs models faster than ever, automatically converts legacy models, and requires no IT footprint. Cosmic Frog is the only supply chain design platform to combine optimization, simulation, and risk engines, and includes a risk score on every scenario.