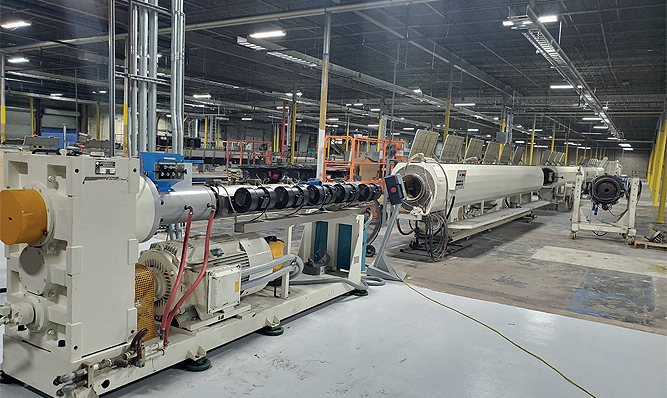
Flying W Plastics
Putting the W in world-class
A manufacturer of polyethylene pipe products since 1984, Flying W Plastics is preparing to double its capabilities with the opening of a brand-new production facility
At Flying W Plastics, quality reigns supreme. In the business of manufacturing polyethylene plastic pipes for more than 35 years, reliable high quality has been key to the firm’s longevity. Selecting only prime grades of polyethylene resin from reputable resin manufacturers, all material used in the production of Flying W products passes through the company’s Quality Control laboratory before it is put into use. The lab then tests all finished goods to ensure they comply with applicable manufacturing standards, before being labelled with identity codes to allow for complete traceability through production and delivery. It is a level of detail that permeates all areas of the organization.
“Flying W Plastics manufactures its products to comply with, or exceed, the highest industry standards available,” explains company President Doug Morris. “We take pride in our products and make every reasonable effort to ensure that when they arrive in the field, they perform as expected, last as expected, and meet or exceed the expectations of our customers. Further to this, our lab, facility, and records are inspected by NSF at a minimum of twice per year to ensure our products meet their high standards, as well as our own.”
With sizes and specifications to meet diverse project needs, Flying W pipe products cover a range of commercial and industrial applications, including water and sewer, gas collection and gathering, telecommunications, electrical conduit, geothermal, power plants, and landfill. The products are sold through a vast network of distributors, many of which are national and international companies. At present, Flying W’s production capabilities exceed five million pounds of finished goods per month across ten production lines. Sizes manufactured include ½ inch through to 20 inches, but this is all about to change. Following the recent purchase of a 169,000 square foot facility in Jacksonville, Florida, Flying W is preparing for a major expansion to its manufacturing capabilities.
“While our business is concentrated in the eastern half of the United States, we ship products to every state in the continental US, to Canada, and several other countries. The new Jacksonville facility adds five production lines to what we already have available to us, creating an additional 70 million pounds capacity annually to help serve our wider customer base,” Doug states. “The new JAX facility will also allow us to produce 24-inch pipes, as well as generating 45 to 50 new jobs as we start manufacturing 24 hours a day, seven days a week. The geographical advantages of the new facility mean that we will be able to utilize the Jacksonville port, which will allow us to move into the Caribbean market where inclement weather, such as hurricanes, has led to a growing need for infrastructure to be buried underground, which often requires HDPE plastics.”
Among the groundbreaking new equipment on show at the Jacksonville facility when it opens its doors in late September will be KraussMaffei extruder technology. Offering high output and increased efficiency, the extruder will go a long way towards doubling Flying W’s production within just one year.
“We did a lot of research and it means we can now look forward to using some of the industry’s best technology in Jacksonville,” Doug remarks. “The new KraussMaffei equipment processes twice the amount of plastic we are used to, so we’ll be taking a huge leap forward in that area. We currently have 11 or 12 lines up here at our existing West Virginia facility, yet the five lines down in Jacksonville will manufacture the same amount of product, and probably more, because the new lines are simply more efficient.”
A forward-thinking company not only in its use of modern technology, but also in its commitment to environmentally friendly practices, Flying W is proud to manufacture sustainable piping solutions for the 21st century. At the center of the company’s positive green credentials is the fact that all Flying W products are manufactured from high density polyethylene (HDPE).
“Starting with a leak-free joint for pressure systems, HDPE pipe is the greenest choice for municipal water, sewer, and storm water applications,” Doug asserts. “A lower environmental footprint is the hallmark for HDPE pipe. Starting with its low energy requirements for manufacturing, and continuing throughout transportation and installation phases, the energy needed to completely install a HDPE pipe system pales in comparison to the economic and environmental cost of pipes from various metals or concrete. HDPE pipe’s resistance to corrosion and abrasion will also create a longer utility life for generations to come. This translates into direct consumer savings and strong enhancement of our environment.”
Strong levels of trust
Deemed to be an ‘essential business’ during the early stages of this year’s Covid-19 pandemic, Flying W has operated without interruption throughout 2020. However, in a year like no other, the business has been forced to make a number of operational changes that are likely to remain in place for the foreseeable future. As far as Doug is concerned, none of these changes have been more important than the procedures put in place to protect the company’s valued employees and clients.
“People are our most important asset,” he professes. “We have multiple long tenure employees that have successfully participated in our profit-sharing programs and they continue to bring new innovations to the table and contribute to many process improvements.
“Put simply, we wouldn’t be where we are without them,” Doug adds, “and that’s why we have done so much to protect them at work this year. As a result, not one person has been sick with the virus. Our managers have done a great job getting their teams to adapt to these unprecedented times and, for example, have facilitated a switch over from 18-inch production to 12-inch production, which we can do 30 per cent quicker.
“Our whole team has really stepped up to the plate at a time when we’ve needed them most. We benefit from a strong relationship and when they see me worried about something, they put it upon themselves to come up with solutions. I can sleep at night knowing that the team here is always doing their best. I can take my family out and refresh my mind knowing that this business is under control. When you have great people in your organization that you trust, it just makes everything roll.”
As well as supporting its close network of wholesalers throughout the pandemic, Flying W has also been looking at the potential for new projects with metal conduit, infrastructure for fiber optics, and golf course irrigation. Though the global downturn brought on by Coronavirus has impacted some of Flying W’s business activities, the company has used the lull to prepare itself for the future.
“Some areas of interest for us were really coming up big in 2019 but there is not really a sector that hasn’t flattened out since the pandemic,” Doug admits. “Consequently, our goal has been to tighten up the ship and be ready for when business comes back. I don’t know any company that has been going gangbusters this year, but we have stayed committed, we’ve got good people, and we’re on track with the Jacksonville project. We will certainly appreciate the good times whenever they come because it has been a struggle, but we’ve put ourselves in a position to succeed.”
As Coronavirus complications continue, and with the US presidential elections on the horizon, Flying W is aware that uncertainty may plague the business world for the rest of 2020, but Doug argues that it’s nothing the firm can’t tackle. “From our base in West Virginia, we continue to grow and adapt,” he says. “Throughout the pandemic, we’ve been able to jump from one thing to the next, performing maintenance on the plant, cleaning, streamlining, and making the most of slower times so that our efficiencies are in good shape for when everything gets back to normal.
“Looking beyond this year, we see brighter times ahead,” Doug declares. “I want companies to want our products. I would love to develop some flexible, specialty products and take them from infancy into production. As a business, we will be comfortable getting to $100 million or $150 million in revenue so that we can take care of our people and they can take care of themselves.”
Flying W Plastics
Products: Polyethylene pipe products
www.fwplastics.com/products