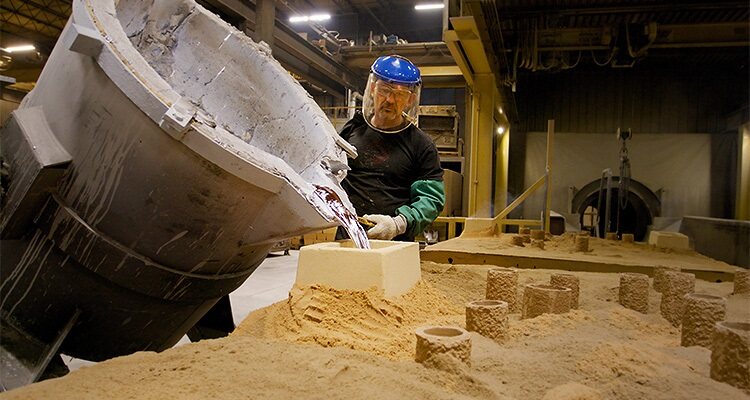
For over 100 years, Wisconsin Aluminum Foundry has been a stronghold of excellence, innovation, and versatility in the casting solutions sector
Wisconsin Aluminum Foundry (WAF) was brought to life by Abraham Schwartz in 1909. The company is still privately held by the Schwartz family, who have continually invested in the business to grow the company to where it is today. “We have a very dedicated workforce that has the family’s passion for customer service and community support engrained in the DNA of the organization,” begins President, Bob Braun. “WAF designed and built aluminum pressure cookers back in the 1930s, and the ‘All-American’ model is considered one of the premier units in the world that we still cast and market out of our consumer product facility in Manitowoc, Wisconsin.” The company is completing the largest expansion in its history this year with the 50,000 square feet permanent mold addition. The foundry is considered one of the largest non-captive nonferrous plants in the country shipping more than one million pounds of finished castings monthly.
The foundry is fortunate enough to have several molding processes under one roof. From air set sand molding and green sand low volume to automated molding lines, static and tilt pour permanent mold and low pressure permanent mold the company can offer a wide array of options to cast parts. “This provides critical flexibility to choose the process best fit for the casting. We currently cast parts that range in weight from one ounce up to 1350 pounds. Volumes range from a couple of parts per year up to over 250,000. Many of our parts require multiple secondary operations including heat treatment, blasting, impregnation, machining, coating, painting, and assembly. The plant thrives on managing all these operations to provide our customer with a ‘line ready’ component.”
For Bob, every day is filled with new opportunities that challenge the team, and according to him, being bored is something he says has never been a concern. “Many of us start early and a common day is 11 hours long. Although everyone has job duties, we work together to address issues and difficult castings to come up with solutions that eventually resolve the problem.” He adds that union team members are often engaged in this problem-solving process.
“There is a huge sense of pride in what we do, and the castings produced by the organization. Our corporate values are: ‘Bring your best,’ ‘engage to succeed together,’ ‘pursue potential,’ and ‘invest in our future.’ I believe that these values sum up who Wisconsin Aluminum Foundry is and how we operate daily,” shares Bob.
When asked about his reflections on the year gone by, Bob says that ‘challenging’ comes to mind. Incoming orders continue to decline. “One of the largest programs is moving to service, which is creating a large void. We need to win new business to replace this loss. Although we are engaged with many customers on new programs, many are in a ‘wait and see’ mode and are not releasing the new jobs.”
One aspect the business is excelling in is its efforts to ramp up interest in apprenticeship schemes. “We have engaged with our local education system at high schools and technical colleges to foster career opportunities at WAF, both in terms of operations and support staff. This collaboration has been ongoing for over 40 years.
“Our engineering manager who has over 25 years started in a ‘school-to-work’ program when he was a sophomore. We have company training programs in our machine shop, and maintenance area along with several in our foundry departments. In 2022, we established a dedicated training area where new employees spend their first two weeks understanding how to read process sheets, finish a casting and get a feel for the foundry environment. This center significantly improved our retention rate for new hires.
“We received the New North Workplace Excellence Award for this project. We are also encouraging diversity and inclusivity across our organization, and, the last major initiative, is to offer a $400 childcare allowance per month to employees. This added benefit has allowed us to attract some of the younger generation to our workforce.”
Bob further stipulates the business works very closely with all its suppliers. “Wherever possible our goal and desire is to be the Tier 1 supplier to the customer. For many years pre-Covid-19, our on-time delivery exceeded 99.5 percent with a short three-week delivery for castings. We have a strong team that manages our suppliers not only on the delivery side but also on quality and operationally. Many of our key suppliers have worked with WAF for decades, which has established dependable loyalty.”
Now looking to the future, Bob outlines that the business is excited about the acquisition of the two other foundries and the large permanent mold addition in Manitowoc. “We need to continue to automate operations to reduce labor and become more efficient. The company has the talent and engineering skills to meet these challenges. I believe that we will keep doing what we have done for the past 114 years and continue to improve and succeed.”
In our closing thoughts, Bob shares sentimentally that with 46 years of history, he does not regret joining WAF as a young man back in 1977. “The Schwartz family have been supportive and great owners who have given us the respect and approval to run the business as we see fit. This has allowed us to be responsive and successful. They have allowed us to also make mistakes, which often teaches you more than success. We work very hard as an organization, but we also take time to socialize and get to know each other through fun activities. We support the community in many ways thanks to the generosity of the family. It has been a great journey through life,” he concludes.