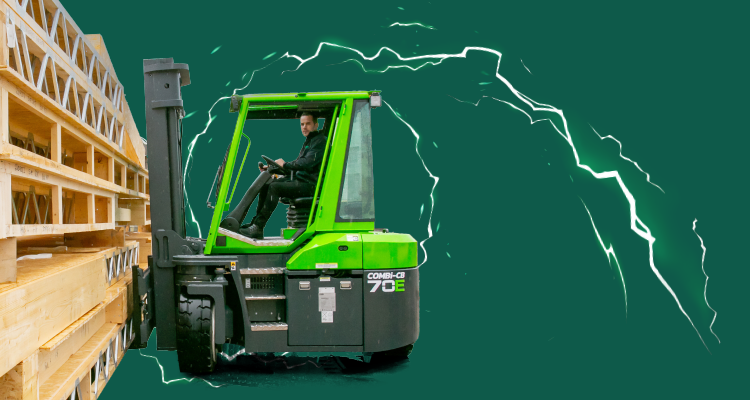
From its Irish roots to global success, discover how Combilift became a driving force in logistics
Celebrating its 25th anniversary, Combilift stands as the foremost global manufacturer of multi-directional forklifts, renowned for its expertise in long-load handling solutions. With an impressive array of products including multi-directional forklifts, side loaders, stackers, straddle carriers, container loaders and more, Combilift caters to diverse material handling needs. Although originating from Ireland, the company’s reach currently extends to over 85 countries, firmly establishing its position as an international leader. Through innovative design and a commitment to quality, Combilift continues to revolutionize the industry, empowering businesses worldwide to optimize their operations and enhance efficiency in handling challenging loads. Paul Short, President of North America, shares the organization’s journey with us.
“Combilift was established in 1998 by Robert Moffett and Martin McVicar and emerged from their collaboration at Moffett Engineering Ltd, a business founded by Robert and his family. Following the sale of Moffett Engineering in 1987, Robert and Martin – who had been the head of research and development (R&D) at Moffett Engineering – joined forces. Together, they conceived the idea of the Combilift – a multi-directional engine-powered forklift. Today, Robert and Martin remain actively involved as owners of the company, which is headquartered in Ireland with full manufacturing and design capabilities. Due to Ireland’s relatively small market size, Combilift was strongly focused on exports from the beginning as the local market alone couldn’t sustain the growth of the business. Indeed, the owners recognized the need to explore international markets, build relationships, and find customers who could benefit from their solutions. Therefore, we have made significant investments in the countries we ship to, establishing a presence with dedicated personnel on the ground. We have also cultivated a robust dealer network, providing excellent service from the factory level down to the dealers. The recognition we got as Manufacturer of the Year in the export category underscores the importance of export success. We received valuable support from Enterprise Ireland, a government agency promoting Irish export products, further bolstering our achievements in international markets. Today, we have 800 employees working at our manufacturing plant in Monaghan, Ireland and an additional 150 worldwide,” he begins.
Combilift’s customer-centric and innovative approach has effectively tackled storage challenges since its inception. As the company celebrates its 25th anniversary, Paul reflects on Combilift’s remarkable journey. “From humble beginnings as a small start-up 25 years ago, we have evolved into a substantial employer in Monaghan, a predominantly rural area. Our achievements, including notable awards received over the years, highlight our progress. We take pride in the fact that many of our current employees have been with us from the beginning, a testament to our business stability and longevity. The owners remain committed to the company’s future, indicating a long road ahead for Combilift with our current setup. With the owners still heavily involved in our operations, we are headed for even more growth, which is already evident in our production numbers. Last year, we manufactured just under 9000 units at our factory, while there are 80,000 units in operation worldwide, with 27,000 of them located in the US alone. In terms of product development, we have launched five new products this year, the latest of which were premiered at Combilift headquarters at an exclusive event that marked Combilift’s 25th year in business. The COMBi-CUBE was the first product launched this year at the LogiMAT International Intralogistics show in April. This new electric model features Combilift’s unique dynamic 360 steering that enables seamless directional change while on the move, making it the most maneuverable counterbalance forklift on the market. Ligna, the international timber and woodworking show that took place in May, saw the launch of another new model truck: the COMBi-CB15 5E. The new COMBi-CB15 5E is a further addition to Combilift’s ever-growing range of electric models and boasts the distinction of being the shortest 15,500 lb. capacity counterbalance truck on the market whilst also benefitting from multidirectional ability, enabling the versatile space-saving handling of both long and bulky loads. In September, the Combi-AGT was unveiled at Fabtech, North America’s largest metal forming, fabricating, welding and finishing event. The Combi-AGT is a 4-wheel electric stand-on model, and it is the world’s first autonomous side loader with the option to operate manually. On September 25th, Combilift announced its move into the offshore wind sector with the launch of a new product designed to meet the load-handling demands of large-scale offshore wind manufacturers. The Combi-LC Blade, designed at Combilift’s HQ and Manufacturing plant in Ireland, in collaboration with Siemens Gamesa, allows for the movement of wind turbine blades and towers through production stages and onto storage locations. The last of our launches was the Combi-Connect, a telematic software product that provides customers with greater levels of insight into fleet management and usage, providing real-time data on fleet performance, including location tracking, usage analytics, and maintenance alerts,” he details.
Paul delves into the optimization strategies employed at the Monaghan manufacturing plant to make it more economically and sustainably efficient. “Our facility is 500,000 square feet and was purpose-built for manufacturing our equipment. Completed in 2018, it was meticulously designed to maximize manufacturing efficiency. Thus, the facility provides ample room for expanding production, potentially doubling our machine output. Moreover, sustainability is a top priority for us in terms of facility capabilities. We have incorporated solar panels, a biomass burner for water heating, and numerous skylights to maximize natural daylight for our workforce, reducing reliance on artificial lighting. In regions like Ireland and the UK, where winter days can be dark, we have implemented LED lights that are sensitive to the ambient lighting conditions. These lights do not immediately switch on at full brightness but adapt gradually as the day gets darker, ensuring a consistent level of illumination throughout,” he adds.
In addition to investing in the development of its manufacturing plant, Combilift allocates resources each year towards new equipment and developing new products. “About seven percent of our annual turnover is dedicated to reinvestment. This has led to new product development, including advancements in our electric and warehouse trucks. One notable ongoing project that has been in progress for the past three to four years is the development of an autonomous vehicle. As part of that, we recently launched the Combi-AGT, marking a significant milestone. In addition, we have been expanding our range of larger electric trucks and our transition to electric-powered forklifts has been noteworthy, with 70 percent of our current production being electric models. Our approach revolves around actively listening to our customers, understanding their challenges, and then developing products that address their needs in the long run. Combilift is owned by two engineers who are passionate about research and development and problem-solving. As a result, when we encounter customers facing challenges or problems, our focus shifts towards new product development and research within our dedicated R&D department. Here, our owners and team dedicate their time and expertise to shaping innovative products and ideas,” he enlightens.
Considering Combilift’s remarkable achievements in manufacturing electric models, Paul offers insightful perspectives on the progress of electric vehicles and the dynamics of the market. “Electric vehicles have gained significant traction in the forklift industry due to their suitability for conversion. These settings allow for the availability of dedicated charging stations that can conveniently accommodate overnight charging during regular duty cycles. In contrast, vehicles that cover longer distances face challenges in predicting the location of charging stations, making ICE-powered forklifts a more practical choice. Converting to electric power within warehouse settings, where power infrastructure is readily available, is common and straightforward. Furthermore, the shift towards electric forklifts is driven by customer demand, as it benefits the environment, operator comfort, and employee well-being by reducing noise and air pollutants. Technological advancements in motor controllers, charging systems, and batteries have improved runtimes, making electric forklifts more comparable to their engine-powered counterparts. While electric vehicles on the road have gained attention in the past decade, the adoption of electric power in forklifts has been a successful trend for a much longer time,” he ends.
Combilift’s enduring legacy as a pioneer in long load handling, coupled with its exceptional engineering expertise and global partnerships, positions it to continue driving customized innovations that enhance logistics efficiency on a global scale. With a steadfast commitment to agility and sustainability, Combilift sets the stage for further industry-leading achievements.
www.combilift.com