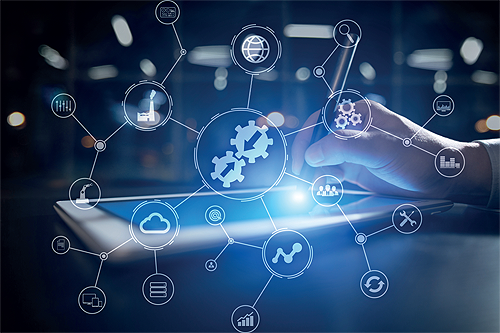
Get with the system
Manufacturing SMEs often retain outdated equipment, IT hardware and software systems as several generations of more efficient, secure upgrades are introduced. While inertia and an unwillingness to master new systems and processes both play their part in failing to upgrade, cost-savings and risk are the main drivers.
However, it is invariably a false economy, with huge financial costs, security compromises, commercial consequences and operational barriers for those who continue to use legacy systems.
According to a 2017 study by global professional services company, Avande, they make up an average 31 per cent of any organization’s technology. Meanwhile, UK manufacturing lags far behind global pack leaders in adopting leading edge automation in the workplace.
Industry leaders have repeatedly voiced their concerns at their inability to replace legacy applications with new digital initiatives. In 2017, the International Federation of Robotics reported that South Korea boasted 710 industrial robots per 10,000 manufacturing employees, compared to Britain’s 74, underlining how slow we are to adopt leading edge production equipment and systems. boost staff happiness, drive top level people to your door and encourage innovation rather than stifle it.
The challenge, then, is how to change or replace existing systems with minimal disruption and downtime. Deciding which route is best is not easy. Manufacturers must consider how to keep delivering in the now – operating as normal to meet current organizational needs – whilst planning for future requirements, with upgrades, integrations or migrations.
There is an array of options to consider, which vary depending on the performance of current systems, the type of software products preferred (i.e. off-the-shelf, bespoke, cloud hosted) and the scale of the business, both today and what’s planned for the future.
When deciding what to do with legacy IT, ask the following questions:
- What do existing systems currently offer the company and how long will they be valuable?
- Do they still provide the responsiveness, outputs and speeds of delivery required?
- Are the costs of running and maintaining them sustainable?
- Does sufficient support still exist for them?
- Can the systems be integrated with newer technology for desired improvements?
Approaches to legacy upgrades can vary based on the stage and status of existing frameworks. There are times where it can be faster and more effective to completely replace a system, rather than waiting longer to decide how to integrate the old with the new. However, depending on the state and age of your current systems, it may be that a total rip-out-and-replace isn’t needed.
For example, adopting a modular approach allows organizations to rebuild legacy systems in phases. By separating the existing system into modular components, organizations are provided with the ability to review business needs, processes and workflows against each module during a rebuild, with an iterative and incremental upgrade path. This particular approach can also help to remove complexities that come with large-scale systems with convoluted business logic.
System extensions can also be a viable alternative to ripping out and replacing legacy systems. By introducing automated workflows over existing systems, organizations can benefit from a richer user interface with additional functionality without having to replace the existing software or databases.
While this sort of gradual introduction could well be a lower risk strategy, a complete replacement of legacy systems may be non-negotiable in some cases – for instance, when it is agreed that the old system is too expensive and/or poses too many risks to the business. In these circumstances, replacing the systems completely could be faster and more cost effective.
Deciding which solution and approach is right for legacy technology upgrade projects will depend on the expertise within your team, the resources available and your business goals, as well as the complexities, time frames and your budget. There is no ‘one size fits all’ for manufacturing businesses however, when planning for such technology projects, organizations should keep in mind how the solution will support both short and long term scalability plans, tie back to wider business strategies, and provide the ability to react to growing and evolving business needs.
Philip Rashleigh
Philip Rashleigh is Audacia’s technical director. Audacia is a Leeds and London-based software development company, specializing in the design, development and delivery of scalable and robust, business-critical software systems. Audacia has established a reputation as a critical technology partner with long-standing relationships; helping customers automate their processes by delivering intuitive and reliable technology solutions.
www.audacia.co.uk