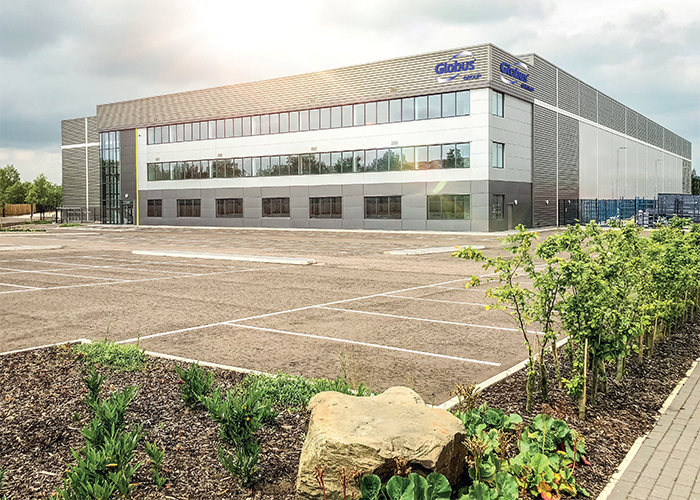
Globus Group
The end to single-use
For almost 30 years, Globus Group (Globus) has delivered innovative, resilient, and reliable PPE products to workers in healthcare and across multiple industrial sectors, from construction and manufacturing, to oil and gas and aerospace. Home to a number of leading brands, including Alpha Solway, Riley and HAIKA, the company mobilized rapidly in early 2020, as it sought to meet the urgent needs of healthcare professionals throughout the Covid-19 pandemic. Now, as normality resumes, Globus is targeting a new challenge: to become a Net Zero business by 2027.
With a date more than 20 years in advance of the UK Government’s official Net Zero target of 2050, there’s no doubting Globus’s ambition. But for Pete Lee, Head of Quality at Globus, the 2027 date is nothing short of necessary. “Taking carbon out of the atmosphere in ten years’ time isn’t good enough,” he tells us. “We need to act now.”
In fact, the relatively short time frame in which Globus hopes to achieve its goal is a key part of its strategy. “Reaching Net Zero is really important to us, and for that reason we need to generate real momentum within our organization to bring our employees along on the journey,” Pete indicates. “If we set our goal as 2050, or even 2040, it’s so far into the future that it doesn’t create any sense of urgency. By settling on a closer date, the aim is to really push ourselves to deliver results and get everything moving right away. Now, everyone throughout Globus recognizes the need to act.”
True to its word, Globus’s sustainability journey is already well underway. It’s more than 18 months since Globus opened two new manufacturing facilities in Golborne, Greater Manchester, and Dumfries, Scotland, in response to the urgent need to deliver life-saving PPE to doctors and nurses in hospitals across the country. At the peak of demand, the company was supplying millions of masks per week to the NHS. At the same time, however, it became apparent that the company was also producing a significant amount of waste, in the form of offcut materials.
“By establishing new factories in the UK, it allowed us to manufacture PPE locally, rather than sourcing from distant parts of the world,” Pete reflects. “On the one hand, that helped us to avoid significant GHG emissions from shipping our products, while also delivering a secure and reliable supply of PPE throughout the pandemic, and creating over 900 jobs. At the same time, in order to ensure our customer’s safety, we do need to use polymeric materials, and some of these have to be single-use. As a result, we’ve had to put a considerable amount of investment into exploring efficient routes to recycle single-use PPE.”
It’s something that’s easier said than done. “There are a number of key challenges to recycling PPE, from how you efficiently collect used PPE on a large site like a hospital, to how do you then bring it back to be recycled in a carbon efficient way to create useful, valuable material again,” Pete notes. “All of the above needs to be completed in a cost-efficient manner.
“Our facilities have been zero-to-landfill from the outset, with all our energy supplied by green tariffs,” he goes on. “But we’re not content with that, particularly if it means that three-quarters of our waste is still being incinerated. We want to move up the recycling scale, and genuinely reduce the amount of waste plastic in the world.”
Successful partnerships
One of the first actions that Globus took was to identify an external partner that could make use of its waste materials. “We identified a company that was purchasing virgin plastic for the production of its products, when instead they could be made from our offcuts,” Pete explains. “We’ve teamed up to make that happen, transporting our waste directly to their factory, where it’s used as a raw material to make absorbent products for the NHS.
“We then invested in a CurtainMelt machine, which is used to melt further waste from the site, turning it into polymer blocks, which are then taken away to be used in the production of new products,” he adds. “In all, these methods have allowed us to reach the point where we operate zero-landfill manufacturing sites, with 75 per cent of all our waste now recycled into new products.”
Globes hopes to increase that figure to 90 per cent within the coming year. “Some of our facemasks have plastic valves or metal nose wire, which makes it complicated,” Pete says. “We’re now developing ways of removing those features in an efficient way. It’s always our aim to move up that league table of recycling, working with our customers to allow single-use PPE to be recycled and given a new lease of life in a circular economy.”
To support its objectives, Globus recently announced the launch of its Knowledge Transfer Partnership with Heriot-Watt University, based in Edinburgh, Scotland. Its goal is to develop a bespoke PPE recycling process using chemical technology, in which plastic polymers are broken down into their constituent parts, to be used in the production of fuel oils. “The team at Heriot Watt have strong expertise in chemical engineering, and cutting-edge facilities with which to experiment and optimize the design of the plant,” Pete insists. “At Globus we understand PPE, how to run manufacturing plants, and we have a huge desire to make cost- and carbon-efficient recycling of PPE a reality. It’s the perfect match.
“We’re also working with further external partners to create recycling routes for gloves, face masks, and other polymer-based PPE products, again using chemical technology,” he continues. “It’s recycling in its purest form, and it’s particularly effective for products that contain more than one material.”
In parallel with its effort to advance revolutionary new recycling methods, Globus is also directing its energy towards product design, as it looks to guarantee that all its UK-manufactured products launched after 2024 qualify as Net Zero. “You can’t be serious about Net Zero if you continue to design and launch new products that don’t support that,” Pete admits. “Our R&D teams are heavily engaged in our sustainability journey, and we’re really changing the way we design products so that they’re able to be recycled readily, and have a longer lifespan.”
As it does so, Globus hopes to add to what is already an impressive roster of product innovations, including the recently launched MX C transparent face mask, designed and manufactured in the UK by Alpha Solway. Specifically tailored for the medical and healthcare sectors, the MX C features a clear anti-fog front panel, positioned to prevent reflection and make lip reading easier. It’s hoped that the masks will enable clearer communication for frontline workers dealing with all patients, but especially those with communication needs.
“Particularly in a healthcare setting, effective communication relies on positive non-verbal elements, such as expression and emotion,” Pete emphasizes. “Miscommunication is a key cause of medical errors, and can be prevented by spotting these critical facial cues. The MX C’s transparent panel allows the wearer to share a friendly smile, making conversation more natural and accessible, and helping patients to more easily understand the information they receive from healthcare professionals.”
Staff contribution
With Alpha Solway manufacturing more than one million MX C masks each week, the importance of a robust supply chain can’t be understated. “Without our suppliers, we cannot succeed in protecting the doctors, nurses, and workers who rely on our products,” Pete notes. “We’re constantly meeting and talking with our suppliers to understand how we can work together to deliver world-class product quality.”
This collaboration is equally important in the pursuit of Globus’s sustainability goals. “We can’t develop and launch Net Zero products without input from our suppliers,” Pete reiterates. “We’re actively working with them on the calculation of a carbon footprint for each of our products. Through that, we’re deepening our understanding of what the most effective actions are that we can take to deliver on our objectives.”
Before we conclude, Pete is keen to underline the invaluable contribution of Globus’s staff and employees. “It’s amazing to see their innovation, creativity, and passion each and every day,” he insists. “At our sites, we have active apprentice schemes to develop the engineers of tomorrow, and a policy of recruiting and developing from within when new roles and opportunities arise. In this exciting and ever-changing business, we want to give everybody the chance to acquire new experience, and to get involved in all the different aspects of our operations.”
Globus is set for an exciting 2022, with launches upcoming for several innovations across its respiratory, protective clothing, gloves, and eyewear ranges. “We continue to pride ourselves in our speed and agility as an organization, along with our commitment to listening to our customers, and delivering solutions to the issues that they raise,” Pete concludes. “In the near future, you’ll see us launching and delivering robust PPE recycling schemes, and you’ll see data on the carbon footprints of our products. We’ll continue to invest and believe in manufacturing local to the markets in which we operate, whether that’s the UK, Europe or USA.”
Globus Group
www.globusgroup.com
Products: Personal protective equipment manufacture