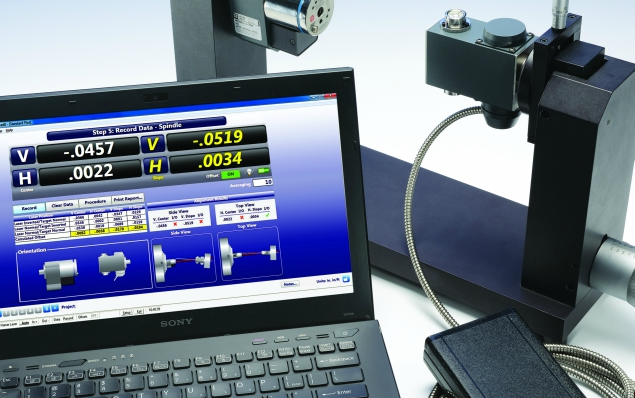
Hamar Laser
Hamar Laser has been a worldwide leader in laser alignment technology for 50 years, solving alignment problems from simple shaft alignments to complex multi-axis alignment applications integrated into automated control systems. “We epitomize the classic American story,”President Rod Hamar says. “My father, Martin Hamar, was part of a team that invented the first laser alignment system while working at PerkinElmer, a large company that didn’t want to pursue it. In 1967, he decided to go out on his own and launch a company to perfect that system and market it with a customer-focused design.”
Hamar never stopped innovating and today Hamar Laser continues to maintain its R&D focus to stay on the cutting-edge of the industry. “Laser alignment is all we do; we work very hard at it,” Rod Hamar says. “We eat, sleep and breathe accuracy but at the same time, relish a challenging application. We have seen countless unique and challenging applications over the 50 years we’ve been in business and it’s a rare day indeed when we are stumped.”
Hamar Laser’s geometry accuracy is the highest in the industry and surpasses competing systems. Ruggedness and durability are also part of their designs that are as innovative as they are long lived with systems that last up to 20 years. Hamar Laser serves the aerospace, automotive, machine tool, power generation, plastics, ship building, food processing, pulp and paper, and steel manufacturing industries with state-of-the-art precision lasers that are accurate, fast and easy to use.
The company built its reputation providing lasers that reduce machine downtime and improve part quality. “Our lasers offer 60-70 percent time savings over traditional methods with much higher accuracy for aligning machinery and that adds to the bottom line with reduced downtime and scrap rates,” Hamar notes.
Manufacturing Processes
Hamar’s lasers are also used in manufacturing applications, such as machine tools and aerospace. A Chicago-based airplane manufacturer, one of Hamar Laser’s larger customers, uses its lasers for machine tool maintenance and aircraft assembly.
“Our laser alignment technology is used in the manufacturing process to keep the wings aligned as components are added,” Hamar says. “They are also used to align the plane’s flap and aileron spherical hinge bearings, which reduced the crew from 8 people working 2 shifts to 2 people aligning these bearings in 2 hours. Our customer’s ROI was less than 3 months!”
Machine Maintenance
Hamar Laser’s alignment systems reduce the time it takes for periodic calibration checks of a manufacturing company’s machines, enabling a proactive approach to maintenance. “Unfortunately, maintenance departments are the ‘stepchildren’ of many manufacturing facilities,” Hamar says. “They don’t get money or praise! Maintenance is a tough world to live in because it’s frequently at war with production to take the machines offline. Anything we can do to reduce machine downtime pays off very quickly.”
“So instead of putting off machine calibration checks, faster alignments mean maintenance techs can do a better job of tracking their machines’ accuracy, and better predict the time when the machine needs to go offline,” Hamar continues. “Planned maintenance is always less painful than emergency maintenance! This is even more critical on large, expensive machine tools, where our lasers’ advantages really shine and where traditional methods like granite squares, levels and straight edges are really painful to use.”
Machine Crashes
With the company’s lasers, customers can perform a quick check right after a machine crash to reduce downtime. “In a matter of about 1 hour, you can do a quick alignment check of all the machine’s axes after a crash and either take the machine offline or have the confidence to start making parts again,” Hamar says. “This is just not possible with traditional methods and is also far better than waiting for the machine’s manufacturer to send their techs.”
Faster Parts Setup
“Another kind of savings that is often overlooked is reducing the time it takes to set parts up before machining,” Hamar says. “If you take the time to properly align your machines, the operator’s going to spend less time setting up your parts. That can add up to big costs savings over the course of a year.”
Machines Versus Parts
Hamar Laser exhibits at the International Manufacturing Technology Show (IMTS) in Chicago and finds it surprising that most of the companies in the measurement pavilion focus on measuring parts as opposed to measuring machines that make the parts. “The big machine tool manufacturers talk about positioning accuracy and repeatability and that’s it,” Hamar says. “There are hundreds of companies that focus on measuring the parts, but only four or five companies focus on measuring the machines that make the parts, so there seems to be a disconnect in the industry’s approach to improving quality.”
Hamar sees a lack of emphasis on machine geometry with machine tool builders and customers. “There are 21 degrees of freedom or 21 possible errors in a 3-axis machine tool. Only 3 of them are linear and the other 18 are geometric. Straightness and squareness specs, however, are often very hard to find when viewing a machine tool’s specs. It doesn’t take a PhD to see that there is a problem of focus.”
“By focusing on the linear positioning and measuring the parts after they are made, machine geometry, the primary source of part quality problems, is often being ignored, which is hardly a recipe for improving part quality,” he continues. “The main impediments to measuring machine geometry are that it takes too much time and is much too complex. Eliminate these and it becomes easy to measure and track a machine’s geometry on a much more consistent basis, resulting in improved part quality and reduced downtime. This is precisely what our products are designed to do!”
Moving forward, the company is seeing an upsurge in maintenance related inquiries as the economy seems to strengthen, Hamar says. Business at Hamar Laser has increased nicely in 2017 and the company plans to continue to innovate and improve their products. “We spent the last couple of years working on our manufacturing processes to improve our throughput and quality,” Hamar says. “With that behind us, we will be focusing on newer products and expect several new products to come out this year.”