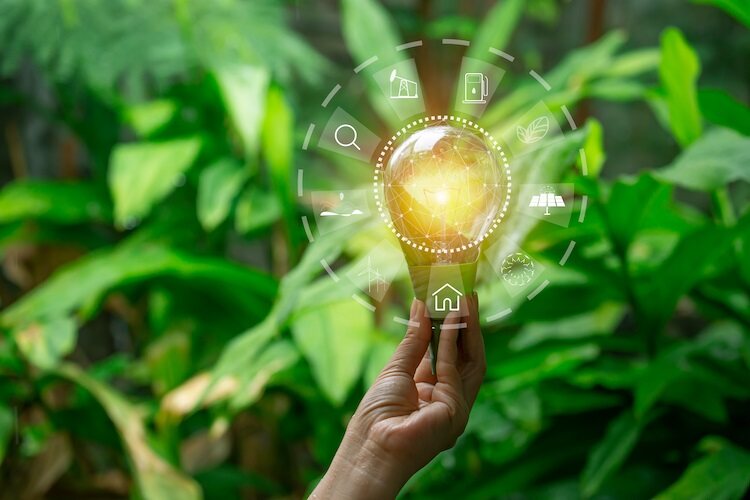
Harnessing the real power of collaboration across industries: how innovation in manufacturing can help reshape the future of energy
Dr Tom Mason shares his thoughts on why and how strategic innovation in manufacturing is the secret to unlocking the full potential of hydrogen fuel cells; driving down costs, facilitating scalability, attracting investment, and ultimately reshaping the future of energy on a global scale.
The immense potential of hydrogen fuel cells is something researchers and engineers have been attempting to unlock since the concept first appeared on the scene in the 1800s.
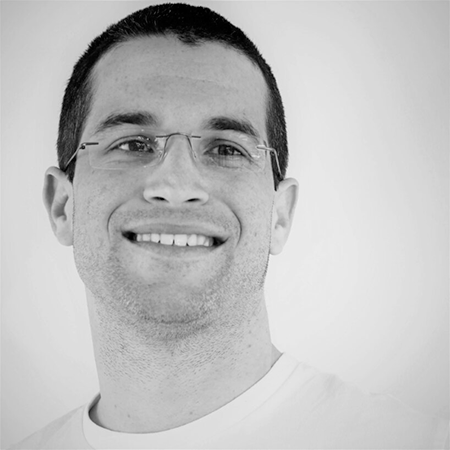
The technology has the ability to provide clean, efficient energy generation with zero emissions, promising to completely transform a host of industries and contribute to a far greener future. But we’re still a way from making this a reality.
As of now, there are numerous companies around the world working on fuel cell technology, ranging from start-ups to established corporations, and even many smaller and niche companies that are focusing on specific applications or technologies within the sector. The obstacles they’re facing differ to some extent, but as a whole, the industry is struggling to make fuel cells economically competitive.
One of the main reasons for this is that the vast majority of these companies haven’t been able to produce fuel cells at a large enough scale to make them cheap enough for widespread use – mainly because it requires a massive investment in manufacturing.
Traditional fuel cell stacks are made up of a multitude of complex components including bipolar plates, endplates, a compression system, a coolant gasket, current collectors, and end gaskets. Each of these components is bespoke to the traditional fuel cell and therefore is either manufactured on an individual line, or more often in completely separate supply chains. In essence, companies in the fuel cell industry often find themselves needing to invest hundreds of millions, and in some cases billions, of pounds to manufacture and sell tens or hundreds of thousands of fuel cells annually.
As such, it’s perhaps not surprising that since the highs of 2021, the industry has seen a collapse in value on the public markets, with established leading North American players taking significant tumbles in valuation. This shift in turn has seen investors lose confidence in these companies’ ability to make money.
A novel approach to fuel cell manufacturing
Thankfully, there are other companies harnessing the power of innovation in manufacturing, and as a result, are standing in a better position. Here, the cost advantage comes from manufacturing fuel cells in a completely revolutionary way by:
- A simplified bill of materials: The Printed Circuit Board Fuel Cell (PCBFC™) is a fuel cell stack that’s constructed using printed circuit board (PCB) technology, which is commonly used in electronics manufacturing. The separate functions are all provided by the PCB, thereby reducing the supply chain to a single factory. As well as fewer factories, manufacturers and reliability issues, the actual component cost of manufacture is also significantly reduced compared to traditional fuel cell constructions. The result is more cost-effective and scalable compared to traditional manufacturing methods.
- Using an already established high volume manufacturing industry: The intricate manufacturing process of fuel cell components demands specialized factories and precision production lines, each tailored to perform highly specific tasks and procedures. Naturally, establishing such facilities means significant capital expenditure, often amounting to tens of millions of pounds. However, in the case of manufacturing the PCBFC™, capital investment is virtually zero. This is because the PCBFC™ leverages existing contract manufacturing capabilities, high-volume PCB industry infrastructure, and supply chains.
- Scaling the only fuel cell gigawatt supply chain: Traditional fuel cell manufacturers face significant challenges when scaling up their capacity. Expanding production requires substantial reinvestment, as doubling the fuel cell capacity necessitates duplicating manufacturing facilities. This means investing in additional facilities, equipment, and staff, incurring both significant costs and considerable time delays. However, those leveraging PCB technology can achieve rapid and cost-effective scalability. Utilizing existing PCB facilities worldwide, they can expand their production capacity within a matter of days, avoiding the need for extensive reinvestment and minimizing time penalties.
Challenges remaining
There are manufacturing innovations that are already clearly solving these issues, with Bramble Energy’s own PCBFC™ being just one example. But for hydrogen fuel cells to gain widespread adoption and true economic viability, further hurdles are yet to be overcome.
For example, issues remain around getting enough of a specific component called the electrolyte – though this component is becoming more widely available as the industry grows. And there are still some concerns about the stability of the supply of materials like Platinum Group Metals (PGM), which are used in fuel cells, though again, this has stabilized since COVID.
PFAS, chemicals found in various industrial applications, including fuel cell manufacturing, are also facing increased scrutiny due to environmental and health concerns. A proposed ban on PFAS usage could disrupt the supply chain for crucial materials, particularly membranes essential for fuel cell operation; a disruption that threatens to impede production and innovation within the industry.
There’s also the issue around the lengthy lead times associated with test stand setup. Test stands are vital for evaluating the performance and reliability of fuel cell systems, but with lead times of 18 months or more, setting up new testing facilities is slow and unresponsive to market dynamics. This process not only delays technology development, but also limits the industry’s ability to adapt to changing demands and emerging advancements.
Another key challenge is the long lead times associated with delivering equipment to end users and final installations, slowing down the pace of implementation and adoption. The impact is not restricted to smaller players, in fact, there are even industry giants at the forefront of hydrogen technology development, who are grappling with massive order backlogs compared to their current production capacity; a backlog that really underscores the disconnect between demand and supply. These delays fuel the perception that hydrogen technology will always be a future prospect rather than being ready for widespread adoption today – another issue deterring potential investors.
Manufacturing’s role in a more sustainable future
These remaining challenges highlight the urgent need to address the bottlenecks in hydrogen technology adoption. Not only does the industry need further innovation in manufacturing, but investments in expanding production capacity, streamlining supply chains, and accelerating infrastructure deployment are also vital.
Collaborative initiatives between governments, private sector entities, and research institutions are all essential to drive innovation, enhance manufacturing efficiency, and scale up production to meet growing demand, while regulatory frameworks and policy incentives also play a crucial role in supporting investment in hydrogen infrastructure.
While there’s much to be done, the bottom line is this: The potential of hydrogen technology to revolutionize the energy landscape is undeniable. Advancements are ongoing and adoption rates are increasing, but industry maturity and widespread adoption aren’t expected until we’re well into the mid-2030s. To get there, we need manufacturing’s continued investment and innovation behind it. High volume manufacturing techniques are the key to driving down the cost of any hardware product, and fuel cells are no different. Only with this support can we drive the transition to a cleaner, greener, and more prosperous society for generations to come.
For a list of the sources used in this article, please contact the editor.
Dr Tom Mason is CEO of Bramble Energy, an innovator in fuel cell technology, solving key challenges in the production of hydrogen fuel cells including lead times, up-front investment, manufacturing cost and scalability.
Founded in 2016 in the research labs at Imperial College of London and University College of London, Bramble Energy – through revolutionary fuel cell design and manufacturing techniques – has developed the unique printed circuit board (PCB) fuel cell – the PCBFC™. A patent protected fuel cell that can be manufactured in almost all printed circuit board (PCB) factories worldwide.
After raising significant capital in 2020, Bramble Energy has rapidly grown from a team of just three to 60+ and is fast becoming the leading hydrogen fuel cell provider for a cleaner and more sustainable world.