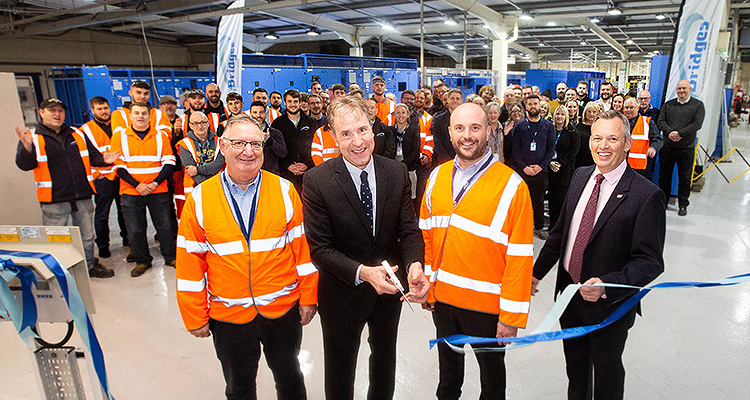
How Bridges Electrical Engineers has fostered an employee-focused culture amid successful growth
From its early days as a family business in the 1970s, Bridges Electrical Engineers (Bridges) has grown to be a trusted, high performance engineering technology company with a well-established client base. Offering comprehensive in-house design, manufacturing, project management and installation services, Bridges works with a broad range of commercial and industrial customers in the water treatment, power, and energy sectors.
“Bridges is a privately owned family business that was originally founded in 1973 by John and Judith Bridges,” opens Chris Maddox, People and Client Director. “Fifty years on, their vision of being ‘better, not bigger’ is as true today as when we started, with a purpose to ‘engineer sustainable assets which our valued customers are proud to own and operate.’ We achieve this through our core values: safe people, happy people and sustainable business.

“From humble beginnings we’ve grown to employ more than 250 people, delivering an annual turnover of over £40 million. Our project managers and installation teams operate across England and Wales via five regional offices, utilizing the latest techniques in off-site manufactured solutions to complement on-site installations.
“Our clients, especially those in the water industry, are constantly striving to maximize efficiency, so we deploy systems and methods to optimize site installations without compromising quality. For our water customers, the more work undertaken away from a live operational site, the less risk there is to clean water or wastewater treatment process. We’ve developed LeanSite, for instance, which is a range of small, standardized solutions and modular components that are assembled under factory quality controls. These have been designed to enhance the efficiency and ease of installation for our site installation teams.”
Bridges boasts a vast range of products and services designed to meet customer requirements and carbon commitments. “Our project portfolio ranges from site surveys and electrical inspection works through to turnkey delivery of projects in excess of £10 million,” Chris elaborates. “Through investment in digital technologies, particularly point-cloud scanning and digital design, our in-house teams can provide fully integrated mechanical, electrical, instrumentation, lighting, and control panel designs.
“Recognizing the limitations of site working, we introduced Design for Manufacture and Assembly (DfMA), leading to the adoption of modern methods of construction and off-site manufacturing. By using parametric intelligent component databases, coupled with our one-millimeter-in-100-meters accurate digital site surveys, we design at a fabrication level of detail and confidently build our off-site solutions tailored to site specific needs.
Company philosophy
“Since our inception, we have embraced the ethos of ‘better, not bigger’ and earned a reputation for being committed to offering high-quality integrated services to support our customers,” he continues. “The ‘all under one roof’ approach is an extension of this philosophy, as we strive to provide comprehensive services from directly employed in-house teams. The principal aims are to streamline project delivery, enhance communication, reduce costs, and maintain high standards throughout the entire project lifecycle.”
This concept is housed within Engineering House, Bridges’ head office in Midsomer Norton near Bath. “Our 60,000-square-foot manufacturing facility is split into two main workshops,” Chris explains. “The first is for our control panels and motor control centers, which is also home to the production of our LeanSite assemblies. The second workshop is our off-site build and package plant assemblies’ facility where we produce kiosk-based products, chemical dosing, and skid mounted assemblies. Supporting this production is our drinking water inspectorate, DWI-approved stainless steel fabrication facility, where we have two welding bays and ancillary equipment.”
Commenting on wider industry challenges, Chris shares: “At Bridges, we are acutely aware of the national engineering skills shortage and have been leading the way in the provision of apprenticeships and unique training solutions to develop our own teams and support the wider industry. We’re members of The 5% Club, a voluntary code to ensure at least five percent of employees are participating in apprenticeship schemes. In addition to apprenticeships, we run skills bootcamps to provide structured learning aligned with industry skills shortages. Through grant funding we operate five-to-eight-week courses specifically developed to help unemployed people enter the employment market and restart their careers in engineering.
“We’re particularly proud of Taylor Stephens, one of our Production Managers and a former Apprentice who won Technician of the Year in the Young Engineer Awards, hosted by the Pump Centre at last years’ Water Equipment Show in Telford. In an interview about winning the award, Taylor was asked where he sees himself in five years, to which he replied, ‘I’d like to be stood here congratulating one of my apprentices on winning this very award.’ As a proud mentor of new apprentices, Taylor’s short but succinct answer perfectly summarizes Bridges’ attitude to encouraging employee development and fostering a positive workplace culture where employees thrive and support one another.”
Award winners
As part of its commitment to developing employee skills, Bridges established an Engineering Academy in 2022. “We established our Engineering Academy, a learning and development center for technical site skills to offer a diverse range of programs to support early learners or new entrants to the sector, as well as seasoned professionals looking to further strengthen their skills,” he confirms. “The center has practical training bays, apparatus to develop electrical and mechanical skills, classrooms for traditional teaching, and test facilities to provide competence assessments.
“The facility has been assessed by OFSTED and is also certified to deliver CompEx Foundation (the global certification scheme for electrical and mechanical installers and designers working in potentially explosive atmospheres) and APM (Association of Project Managers) fundamentals courses. Through all our training and development programs we strive to offer our employees careers, not just jobs, within a culture of care and growth to support our people at every stage of their careers.”
Testament to this, Bridges was named on Sunday Times’ Best Places to Work 2024 list, with the publication commenting on Bridges’ ‘exceptional commitment to creating a positive workplace culture’ through ‘robust support systems, clear communication, opportunities for growth, and a strong sense of community.’
“We were incredibly proud to receive such an accolade, and the fact that we were one of just two engineering businesses listed in the UK made it even more special,” Chris reflects. “While we have grown and expanded, we’ve worked hard to maintain a positive, inclusive culture and sense of community across the business, where people are visible, feel heard, and are aligned to our common goal.”
Future opportunities
In ending, Chris explains why 2024 has seen Bridges further its market share within the UK regulated water sector. “The regulated water sector is at the start of a new, five-year investment period referred to as AMP8,” he says. “With a record program valued at £88 billion, this will be the largest capital investment period since the sector’s privatization, and we look forward to working collaboratively with our customers across the sector supporting them with their programs.
“We’ve also been awarded the MEICA package for the first large-scale water storage reservoir in the UK since Havant Thickett Reservoir in the 1990s. We’re very excited about this project, as it will play a key role in protecting internationally important chalk rivers by securing a new sustainable source of water for the region.
“Further afield, I anticipate Bridges expanding its market share as we further diversify our project and product portfolio,” Chris concludes. “Through our people, we have the foundations, pedigree, and reputation as a leader and innovator in the engineering solutions market.”