How CEAT has utilized efficiencies to generate substantial growth
Going into its 100th year of operation, CEAT is reaching new heights. As one of the world’s largest tire manufacturers, CEAT now operates in over 110 countries, producing over 140,000 tires a day. This remarkable growth phase can be attributed, in part, to a dramatic increase in overall efficiency across all operational areas. Managing Director and CEO, Arnab Banerjee, details: “We have a strong focus on improvement and are constantly looking for inspiration, whether that comes from customers, competitors or other industries. Whenever we find something of value that isn’t protected by copyright, we study it thoroughly and implement it immediately.”
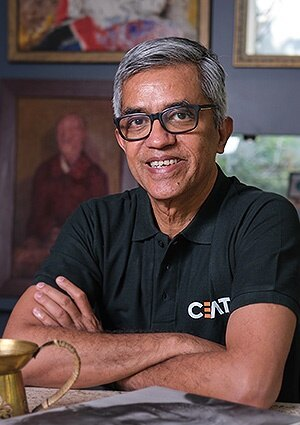
This relentless pursuit of excellence has been recognized by the Japanese Union of Scientists and Engineers, and CEAT has achieved the rare distinction of being the first tire brand to be awarded the prestigious Deming Grand Prize. Part of what makes this accolade so impressive is that it has been achieved by a business that manufactures such a diverse range of products. Arnab expands on the company’s offering: “We operate in all categories, from passenger vehicle and truck tires to scooter and motorcycle tires, and all the way up to earth mover and agricultural tires.”
Each product comes with its own unique needs and requirements. “With electric vehicles (EVs), for example,” Arnab continues, “tire life can be compromised. So, the tire needs to be more durable and also offer very low rolling resistance. Since EVs have fewer moving parts, tires are the main source of noise and therefore need to be produced in a way that minimizes the noise output. Also, when EVs start moving they require a greater amount of torque, so the tires and their patterns must be able to deliver more torque and traction. Range anxiety is also a common focus point in the EV market, and improved rolling resistance can increase the range by eight-to-ten percent.”
Manufacturing such a wide range of diverse products requires efficient processes, as Arnab explains: “Automating a lot of our processes not only enhances our overall efficiency but also minimizes human error. For example, we have mapped out the entire flow of steam and air inside the plant, and we have found a mechanism to detect leakages which can be acted upon immediately. Before this, there were losses that we wouldn’t have been aware of and that were very difficult to detect and locate. A lot of time was wasted in diagnosing the problem. Now we can identify the problem and solve it on the spot.
“Another example of automation is the processing of materials. We buy in a lot of natural rubber, and, as with any natural product, the quality can fluctuate. We have developed algorithms which identify the incoming raw material parameters and adjust the product processes automatically so that the optimum quality is delivered at optimum cost.”
Arnab then highlights how the business’ younger gen-z and millennial employees have played a central role in this process. “With a lot of these Industry 4.0 applications gaining traction, these employees have proven to be very fast learners. When we identify a problem, they are excellent at finding a solution. This has resulted in vast savings in energy costs, scrap reduction, and decreased water consumption, making our plants more efficient and effective.”
The focus on improvement goes beyond just operational benefits but significantly contributes to the company’s sustainability targets as well, with specific measures deployed to improve manufacturing processes. “By 2030,” Arnab says, “we want to reduce our carbon footprint by 50 percent. When we made this decision, we began in earnest by taking several actionable steps. Our boilers, for example, which produce steam, are adaptable to biofuel. Currently, 35 to 40 percent of our plants’ energy needs are met through renewable sources. One of the other big factors in this industry is the product itself. By constantly improving the rolling resistance of our tires, we reduce the amount of energy used whether that’s in the form of fuel in a vehicle with an internal combustion engine or in terms of the range available from a single charge in an EV. The use of sustainable materials in the tire itself is also important.”
Apart from implementing sustainable materials across its products, CEAT has produced an agricultural tire which comprises around 80 percent sustainable material. Implementing these improvements across the business has had such a significant impact that Arnab and his team are looking into how they can adjust their sustainability targets to make them even more ambitious. “We are revising our long-term vision and evaluating when we can reach Net Zero,” he adds.
Looking to the future and maintaining the philosophy of constant improvement, Arnab highlights the extensive investments the company is making towards this goal. “There are more substantial investments into Industry 4.0 solutions, which will not only increase overall efficiency as more processes can be automated, but also lead to reductions in material handling and therefore reduce errors. Automated analytics will also greatly reduce human error in quality assurance. We are also working on closed loop automation systems where the machines can self-correct and communicate with other machines in the production line.
“With such a sharp focus on improvement, Research and Development becomes a foundational pillar in which we are constantly investing. We hold nearly 200 patents and are always seeking to expand the knowledge and technologies we utilize.”
Growing over the course of a century into one of the largest manufacturers of tires in the world, CEAT is capitalizing on its position of strength. Expanding into new markets that promise significant growth opportunities and consolidating its already extensive reach across global markets, the business is set to maintain its momentum as it chases down its bold ambitions in the coming years.