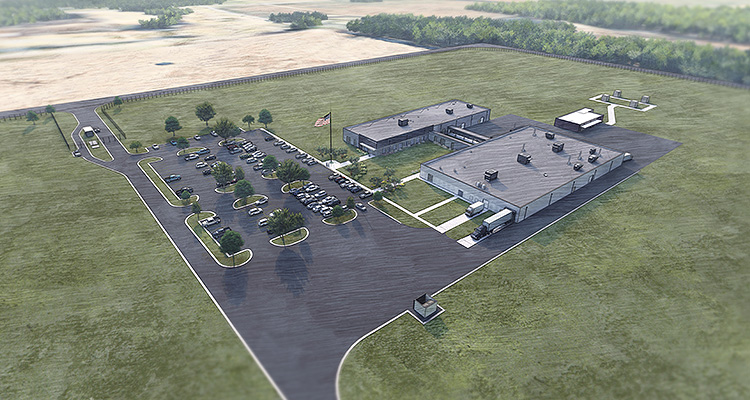
How EaglePicher Technologies continues to push boundaries in battery and energetics manufacturing
Founded in 1843, EaglePicher Technologies (EaglePicher) is a defense and aerospace company with a long history. Director of Operations for Energetics, Jantzen Westfall, describes the journey: “We started out as a lead mining company, eventually entering the battery market in 1922. In the 1940s, we were awarded our first special-purpose battery contract. We eventually merged with another group and created EaglePicher, and after an EaglePicher battery was launched into space aboard NASA’s Explorer 1 satellite in 1958, our specialty battery business really took off.
“For a long time, the company was owned by private equity. In 2023, the business was purchased by a private company out of Chicago, Illinois, called Tuthill. Since then, we’ve started to reshape the culture and the way the organization functions.
“We make a lot of different batteries, from thermal and lithium-ion batteries to energetic devices. In energetics, we primarily support the defense industry, working directly with the government as well as with Raytheon, Lockheed Martin, and Northrop Grumman to supply various programs they have. Our Aerospace group produces lithium-ion for the space and aviation industries.”
Operating in such a fast-paced environment where technology is evolving every day, incorporating automation and other smart technologies is essential to stay ahead of the competition. Jantzen elaborates: “One of our latest automation projects is in our energetics department. We have developed and started building a fully automated production line. It utilizes robotic arms to make one of the smallest parts we make. The product is the size of the end of a pencil and goes into a 30-millimeter smart round munition. Using data including the number of rotations and distance traveled, the device uses formulas to determine when to explode as it approaches its target. The production line will produce 250,000 of these components in a year, in a single shift.”
This is a trend that is reflected across the organization, as Jantzen explains: “Automation is a priority for us at the moment. Working directly with the government means a lot of our products and processes are heavily regulated. There are a lot of approval procedures to go through before these developments can be implemented.
“The type of products that we make are critically important. For example, some of our components are integrated into equipment designed to save lives. If the component fails, then that life isn’t saved. So, it can be difficult to adjust production processes, but we’re working our way through and installing as much automation as possible, especially within new product development.
“We’ve also invested upwards of $1 million in different presses and crimpers that we use in our manufacturing process. This new equipment will increase quality, efficiencies, and throughput, while simplifying the manufacturing processes used by our operators. We’re aiming to implement a lot of that equipment this year.
“In November of 2024 we broke ground on a new energetics facility, which should be ready in 2026 and will increase our capabilities. This represents an investment of over $30 million. Alongside this project, we are also currently building another facility in Kansas. These investments will not only help us be more efficient but will also help facilitate the scaling up of new products.
“As the company continues to take a more innovative approach to manufacturing, we are instilling the correct expectations and accountability into our daily practices, as well as rewards for all the exceptional things our employees are doing. For example, we have implemented a performance sharing initiative, which has never been done at EaglePicher.” As well as providing big opportunities, introducing new facilities and integrating new equipment will also present some challenges, as Jantzen outlines: “As we expand our horizons and increase the range of products that we make, one of the biggest hurdles that I see for energetics is putting all the pieces together – from the supply chain and engineering to operations. We want to make sure that moving into the new facility is a timely and smooth process because any disruption would hurt a lot of different programs within the government.”
Jantzen then concludes with the company’s goals for the coming years: “For energetics in particular, the biggest thing for me is actualizing the big potential for organic growth. Last year, the energetics side of the business produced around $30 million. I believe over the next three to five years we will at least double this figure. To achieve this, having the right culture and the right business practices, and instilling the Lean Six Sigma principles, will be key. Having the right equipment will also be central because we operate with very tight tolerances.”
Manufacturing Today looks forward to catching up with Jantzen and the team in the future. It looks set to implement further advances and continue to be a role model as an innovator and leader in the battery manufacturing space.