How HBK is reshaping the future of precision technology, automation, and smart sensing solutions
Formed in 2019 through the merger of two market-leading organisations, HBM and Brüel & Kjær, Hottinger Brüel & Kjær (HBK) provides innovative, high-quality solutions in precision test and measurement technology for various industries, including aerospace, automotive, industrials and personal audio. Priding itself on exceptional sensing and insights, HBK empowers innovators to solve some of the obstacles to making the world cleaner, healthier, and more productive, from the electrification of mobility to smart manufacturing.
“HBK was born from two legacy businesses based in Denmark and Germany, which have proud and extensive histories of leveraging physics expertise to solve customer problems,” begins Ben Bryson. “Today, the business is over 3500 people strong, and serves primarily the automotive, aerospace, defense, and machine manufacturing markets. Our precision solutions encompass virtual testing, physical testing, and in-process offerings, with our portfolio including simulators, software, data acquisition, and precision sensors.
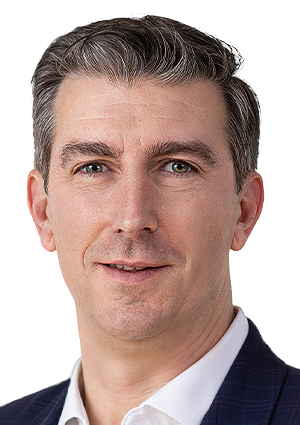
“The strong foundations of both legacy businesses have enabled us to grow organically, but we’ve also completed eight acquisitions during the last five years. While our domain expertise is broad electrical power, force, weight, torque, and sound and vibration, we’ve acquired companies to boost our position sensing capabilities in the robotics and autonomous vehicles environment. The recent acquisition of MicroStrain, for instance, will boost our offering with precision location sensing, with applications including mobile robotics and precision agriculture.”
HBK focuses on delivering peak accuracy and precision across its portfolio. “Our products aim to accelerate product innovation and optimise processes and assets, and the business is set up to leverage four megatrends: virtual testing, digitalization, electrification, and automation,” Ben states. “The first two trends are applicable to machine manufacturing and creating digital sensing. Electrification refers to electrifying mobility such as cars and aircraft, whereas automation focuses on helping customers to automate processes and solutions.
“A strategic element of our business has been to develop our smart sensors and OEM sensors offering, with two of our six growth priorities focused in this area. Smart sensing is the ability to convert analogue sensors into fast, reliable, and performance monitoring sensors at the point of measure, fostering greater efficiency and enabling predictive maintenance. Our domain of expertise, combined with digital sensing capabilities, has seen us create a new product line of IO-Link Smart Sensors, which we launched earlier this year. Offering a phenomenal value proposition, we’re pleased to say that the sensors are already receiving great market feedback.
“OEM sensors, on the other hand, take an existing sensing capability and integrate it into the customers’ hardware. The example I use to best explain this process and its impact is using a strain gauge sensor on an accessory seed planter. This transforms the seed planter into a smart solution, as it can now measure the depth at which the seeds must be planted based on soil condition. At a practical level, it means farmers can accurately plant seeds regardless of differing soil conditions, leading to three-to-four percent yield increases.”
Turning to the company’s structure, Ben explains: “We have a small base in the UK and are part of a FTSE 250, precision engineering company, Spectris plc, which is split into two divisions: Spectris Scientific and Spectris Dynamics, which is the division I manage and represent. At a global level, we have eight manufacturing facilities in strategic locations around the world, and we’re in the process of launching a brand-new facility in Porto, Portugal, to strengthen our existing fiber sensing business. This new site will be a platform to create a European centre of excellence for our strain gauge finishing line as we enhance our capabilities in smart sensing and lean technologies.
“In terms of manufacturing, we have a clear strategy for driving a lean and continuous manufacturing process. My career background encompasses 20 or so years of manufacturing experience at companies like Honeywell, so I’m personally excited and committed to creating lean environments. Not only does lean manufacturing help us to deliver higher quality service from both a quality and reliability point of view, which are both key growth metrics, but it also ensures that we remain as productive and efficient as possible in a competitive landscape.
“We’re applying all the lessons and insights we’ve learned during the implementation of lean processes to our new site in Porto,” he explains. “Alongside this, we’re investing in automation and demonstrating cobots to maximize efficiency in our key facilities, whether that be in our machine shop or in the finishing lines.
“We see automation as highly complementary to creating a positive and engaged workforce. We’re also engaging our employees in our sustainability journey by finding new ways to better run the facility. Over the last year, we’ve invested around €5 million in capital equipment and infrastructure, including a significant investment in solar panels to reduce our energy consumption from the grid. I’m pleased to see the progress we’re making towards our targets of being Net Zero in Scopes 1 and 2 by 2030, and in Scope 3 by 2040.”
With a mission statement to help customers create solutions for a cleaner, healthier, and more productive world, innovation is essential at HBK, where more than 400 employees focus exclusively on research and development. “From engineering test tools to smart sensors and OEM sensing capabilities, we continue to create great products such as our next generation torque (NGT) sensor for the automotive industry, which uses telemetry to pass data between the sensor and recorder,” Ben says.
“We’re committed to spending eight percent of our sales on research and development every year, ensuring these investments deliver value by bringing excellent products to market. In 2025, we plan to launch more new products than ever before, including 85 new sensors, alongside brand-new simulators and software upgrades for existing packages in the virtual testing environment.”
As our conversation closes, Ben reflects on HBK’s journey to date and shares his thoughts on the market’s future. “We’ve always been focused on our customers, and we’ll maintain our customer-centric ethos as the world becomes more integrated and automated,” he says. “As consumer demands increase, our customers will need to produce more products with a higher degree of efficiency. Our key priorities are precision, machine connectivity, maintaining high quality standards, and helping customers to drive automated solutions.
“We also see a future where precision sensors will also incorporate AI philosophies to make them even smarter or more precise, with research suggesting accuracy improvements of up to 120 percent when AI algorithms and machine learning are added. The other growth trends are the electrification of mobility, particularly in aerospace, and the development of products in a virtual world, which will alter the need for physical testing.
“At HBK, we are well placed to secure growth though that cycle,” Ben concludes. “We’ve got the right pedigree and ambition to be successful in harnessing those trends and paradigm changes as we move forward.”