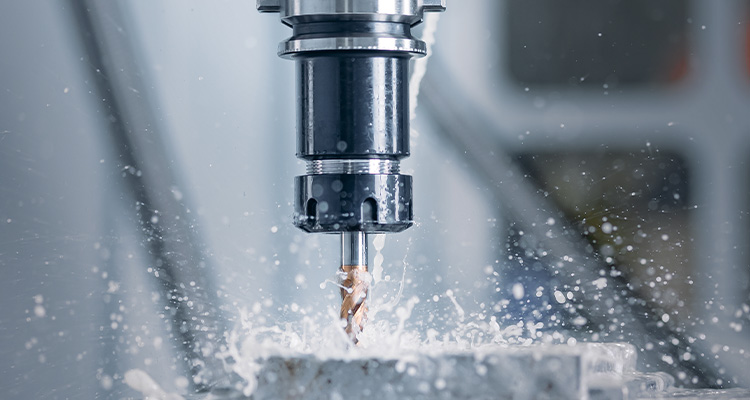
How innovation is forging a new era of precision manufacturing.
The machine tool industry stands on the cusp of a new frontier. With global manufacturing under pressure to deliver more – faster, cleaner, and smarter – demand for more efficient solutions is reshaping the sector.
From AI-powered optimization to ultra-hard coatings and circular economy practices, the evolution of cutting tools is at the center of this shift. In an industry long associated with tradition and reliability, change is now coming thick and fast – and the implications are profound.
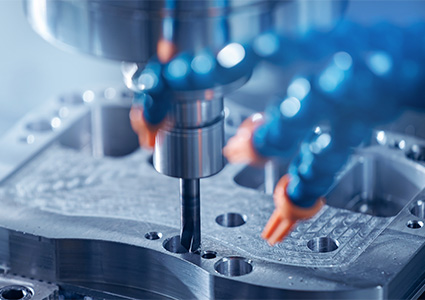
A market demanding more
As industrial output rebounds post-pandemic and reshoring efforts take hold, manufacturers are being asked to do more with less. Trump’s tariffs on steel and automotive, rising material costs, labor shortages, and energy volatility are prompting businesses to re-evaluate every process, every asset – and that includes cutting tools. No longer seen as mere consumables, modern tools are now viewed as performance enablers.
This growing appetite for high-performance tooling isn’t just about speed or precision anymore. It’s about achieving long-term efficiency gains, reducing waste, extending tool life, and embedding sustainability across operations. That shift in thinking is opening the door to a wave of new technologies-and forcing traditional manufacturers to rethink their approach or risk being left behind.
Intelligent tools:
AI in the driver’s seat
Arguably, the most disruptive development in the machine tool sector is the arrival of artificial intelligence. Smart tooling, powered by AI-driven software, is now playing a central role in shaping how tools are used, tracked, and maintained.
Toolpath optimization has become a mainstream conversation, with AI helping manufacturers to create more efficient cutting routines that shorten cycle times and reduce wear on the equipment. But it’s not just about the cutting action itself. The real leap forward is in intelligent inventory and lifecycle management.
Modern systems integrate tool tracking with material requirements planning (MRP), using data from sensors and QR codes to build a full picture of tool usage across the floor. These systems forecast demand, automate reordering, and even flag performance drops before they become problems. The result? A factory that runs smoother, with fewer delays, better-quality parts, and reduced cost per component.
As data becomes a strategic asset, the cutting tool becomes more than a tool – it becomes a node in the connected manufacturing ecosystem.
Coatings that push the limits
The materials arms race continues, with coatings playing a vital role in tool performance. New generations of ultra-hard coatings – some incorporating exotic elements or refined crystalline structures – are extending tool life to unprecedented levels.
Advancements in PCD (polycrystalline diamond) coatings, in particular, are enabling faster speeds and improved wear resistance. Tools are staying sharper for longer, reducing the need for replacements and increasing machine uptime. For sectors like aerospace and automotive, where tolerances are tight and materials are tough, this makes a measurable difference to throughput and cost.
But this isn’t just about harder coatings – it’s also about smarter design. Precision-engineered geometries and multi-layered coatings are giving manufacturers the ability to cut faster, cleaner, and more consistently, with less manual intervention.
Sustainability at the center
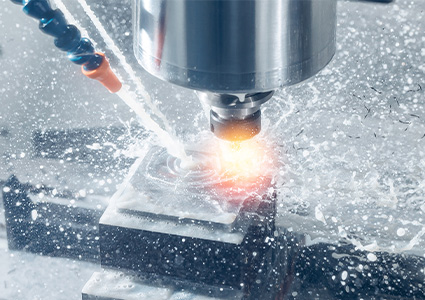
Sustainability isn’t a nice-to-have anymore – it’s non-negotiable. As legislation tightens and public scrutiny grows, manufacturers are turning to the machine tool sector for answers. The shift is clear: more businesses are looking for partners that can offer circular solutions.
We’ve seen a growing interest in refurbishment, recycling, and reduced-waste practices. PCD tooling, for instance, can be refurbished multiple times – re-tipped, re-brazed, and re-sharpened – before finally being recycled. At Exactaform, our own operators are trained to evaluate each tool’s potential for recovery, helping customers extend tool life and reduce their environmental impact.
On-site energy reduction is another major trend. Whether it’s installing solar panels, heat recovery systems, or LED lighting, manufacturers are doubling down on their commitment to low-impact operations. It’s not just about ticking ESG boxes – it’s about futureproofing the business.
Continuous improvement or continuous catch-up?
One thing’s certain: the pace of innovation is not slowing down. Companies that invest in cutting-edge machine tool technologies now will not only gain a competitive edge – but they’ll be also setting the benchmark for what’s possible.
This new age of machine tools is defined by agility, intelligence, and responsibility. It’s about integrating digital technologies with materials science and sustainability to produce solutions that don’t just meet the needs of today’s market but anticipate tomorrow’s.
From AI and automation to advanced coatings and closed-loop recycling, the cutting tool sector is rapidly transforming from a cost center into a cornerstone of smart manufacturing. Those who embrace this shift will unlock higher productivity, better quality, and a lighter environmental footprint.
Jamie White
Jamie White is MD at Exactaform. Exactaform was founded 45 years ago in Coventry, UK by John Inglis, an experienced designer and manufacturer of precision cutting tools. Exactaform has grown into a global supplier with state-of-the-art facilities, largely servicing the aerospace and automotive spaces, including industry leaders such as BAE, Airbus, GE Aviation, and Redbull. Under the leadership of Managing Director Jamie White, Exactaform remains the UK’s largest supplier of PCD tooling while diversifying its portfolio to include carbide and HSS solutions. This evolution upholds John’s vision and commitment to innovation in the cutting tools industry.