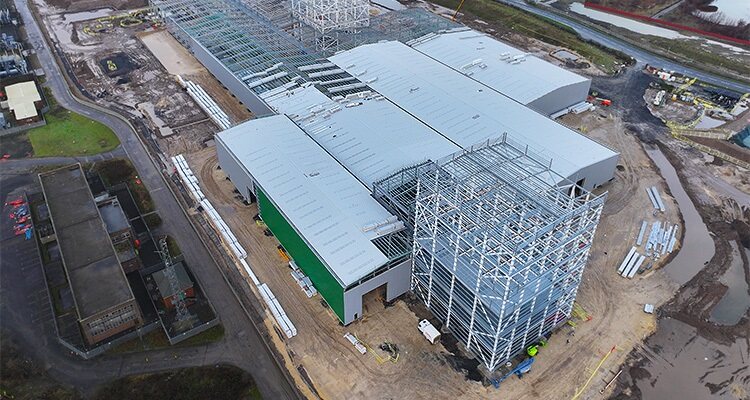
How JDR Cables, a world-class provider of subsea technologies and services, supports the global offshore energy industry
JDR Cable Systems (JDR) was established in the early 1990s,” begins James Young, Chief Strategy & Compliance Officer. “Originally, the company started out providing industrial hoses and couplings and then moved into offshore and subsea equipment, notably for subsea commercial divers, in line with the boom in the offshore oil and gas market. The key thing for us as a business in those very early days was providing high-quality products, because essentially, our products were a lifeline to the user. From breathing apparatus to communications control, we had to focus on quality from day one. We diversified into assisting the industry with the control of subsea valves and equipment, producing subsea production umbilicals (SPU). Many of those original subsea cables still control the oil and gas assets today and fulfil a crucial safety function.”
JDR’s SPUs are designed to operate long-term in challenging and dynamic subsea environments. The products provide critical power, control and monitoring links, connecting multiple elements of an offshore oil and gas field.
“In the operation of offshore energy production, a subsurface isolation valve is used to safely manage pipelines and these valves are controlled by the SPUs made here in the UK, which orchestrates safe shutdown of the pipeline, and the well, should there be an incident. These types of control umbilical were widely implemented following the tragic Piper Alpha disaster in 1988. Hence, these umbilical control systems are there for safety, which is the fundamental consideration in the manufacture of all our products.
“In around 2005, we took the decision to enter the offshore renewable energy cable market, including wind and some wave and tidal applications. We decided to leave the commercial diving market as it was too contracted, and we took the business decision to refocus our efforts on these emerging new energy markets. When we first started our offshore wind cable projects, the cable voltage was around 33,000 volts. All the power from the wind turbines at the Greater Gabbard Wind Farm, for example, is collected by our cables at 33,000 volts. From these early wind farm arrays, we took the lead in the development of 66,000-volt array cable technology. By doubling the voltage, you are essentially doubling the amount of power for the same copper or aluminum conductor cross section. The reason that’s so important is it enables the use of much larger turbines offshore, whilst still driving down the cost of offshore renewable energy.”
Ahead of the curve
“We’ve actually just finished manufacturing a prototype aluminum 132,000-volt cable, which is the next size up,” adds Mark Braybrooke, COO. “We have the materials available to start the copper version and are moving forward with qualification of these next generation array cables which should finish in April 2024. Interestingly, the standards for the accessories to support these advanced array cables need to catch up. There’s no definitive decision on some aspects of the connectors, so to qualify the cable system we need to wait for those other technologies to be agreed. In certain marketplaces, there is considerable client interest in stepping up to those greater capacity cables.”
“If you look at more recent projects under construction, such as Dogger Bank in the North Sea,” James continues, “they’re starting to use 15 and 16 megawatt turbines, which require the 66,000-volt cables. In the next five years or so, that’s likely to be increased to between 18 and 20 megawatt turbines, which will require the 132,000-volt cable and accessory technologies. We’re just ahead of the market in bringing those products through, which will benefit the energy consumer in the longer term by reducing the cost of offshore wind infrastructure.”
In 2022, JDR announced plans to open a new subsea cable manufacturing facility in Cambois, near Blythe, Northumberland. “It’s progressing well,” elaborates James. “The main steel work has been erected and much of the factory roof has now been installed. The machinery’s been ordered ahead of schedule and installation will commence in a few months’ time. We’re right in the middle of construction and we’re essentially building on the site of two disused coal-fired power stations. We’re building off the existing physical foundations, which is a fantastic sustainability story. Our high voltage cable manufacturing facility will serve the offshore renewable energy industry and the transition to Net Zero, and we are looking forward to starting operations next year.”
Delivering cost efficiencies
JDR has also carried out significant manufacturing facility upgrades across its existing sites. “The team at Hartlepool is just about to make their longest, single-length power cable,” Mark adds. “It’s a 66,000-volt, 800-square-milimeter aluminum cable that is 14 and a half kilometers long. You can’t underestimate the challenge involved in producing such a product. It’s been completed live in between projects and has been delivered successfully, right first time. So, it’s a great result.”
The vast scale of this type of machinery is significant and this investment both in Cambois and Hartlepool is indicative of JDR’s commitment to adding greater capacity and capability. “We’re currently the market leader in floating wind array cables,” Mark continues. “This and further expansion allow us to continue that trend and make larger cables in longer lengths. Likewise, it sets us up ready for expansion into the higher voltage export cable market. These cables are used to transmit large amounts of power from offshore substations back to shore. The market will also need larger volumes of these critical infrastructure cables going forward. So, we plan to keep building on our cable technologies to deliver what the market needs in terms of higher voltage export or array cables.”
The custom-designed manufacturing facility in Hartlepool, on the North-East UK coast is ideally positioned for subsea cable offshore wind projects and facilitates simultaneous production. Without the need for transhipping, JDR can reduce timelines and provide real cost efficiencies.
Seizing opportunities
A significant milestone was when JDR won the contract for the Hywind Tampen project, consisting of 11 wind turbines developed by Equinor. This is the first large scale floating offshore wind project to power oil and gas platforms, a far more technically challenging and less mature technology than traditional fixed-foundation offshore wind. Cables pose a particular challenge due to the high dynamic stress they must withstand, however JDR has already established itself as a leader in this fledgling sub-sector.
“We’re looking to decarbonize the production of cables for both offshore oil and gas energy projects, as well as offshore wind,” James continues. “We also want to minimize the amount of greenhouse gases that we’re emitting in our operations. As such, we decided not to include a gas supply to our new Cambois facility, and we have developed the facility to operate on just electricity. With a few offshore wind farms being constructed off the coast, we’re hoping to be able to secure power purchase agreements with those developers once these new renewable energy plants are operational.”
JDR has always been a company with high growth ambitions. “Often, in the markets in which we operate,” James continues, “we’ve come from nowhere. While we entered the offshore wind market relatively early on, for example, we were still a new subsea power cable player. There were more established companies that had provided subsea cables for decades, so we have always been a nimble dynamic company moving into these marketplaces as opportunities arise to support customers with their offshore energy projects.
Global footprint
“We’re able to lead the pack in terms of innovation. This year is about completing the new facility, and next year, we will focus on delivering the 66,000 and 132,000-volt cables to offshore wind developers, helping to create the infrastructure needed to pave the way for the energy transition. The next stage for us is to be a key player in the export cable market, moving into higher voltage longer length infrastructure cables to enable energy exchange between different producing countries, which I’m sure will play a part in the next decade of our expansion. We’ve always been a global company and leading exporter. With a footprint here in in the UK as well as a service base in Houston, Texas, we export our products to projects around the world.”
“Likewise, our new facility,” concludes Mark, “will be a great asset for the local area and economy; one that supports UK manufacturing and also the ability for the UK to protect its own energy interests offshore.”