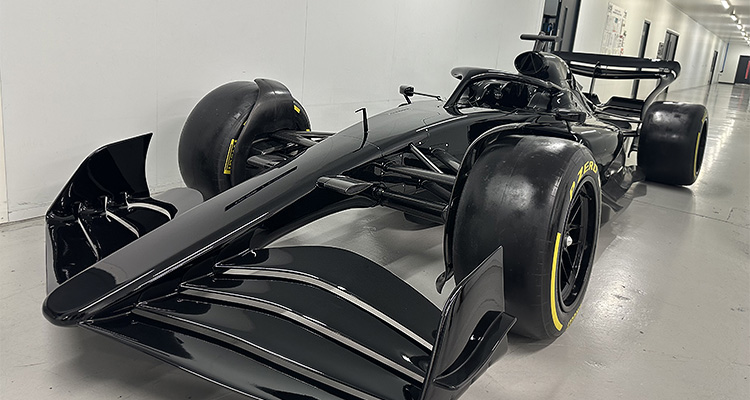
How KS Composites has stayed ahead of the curve for 40 years
KS Composites is a class-leading, turnkey composites solution provider. Managing Director, Jamie Smith, shares the company’s history: “The business was founded in 1985 by my father, Kelvin Smith. The company remains independent and family-run as it heads into its fifth decade. We have always relentlessly pursued the design, development, and manufacture of composite solutions, while continuously performing at the pinnacle of the industry. We operate across a variety of sectors and apply our engineering-led strategic approach to all projects. Our brand ethos and core philosophy of innovation, experience, and excellence have never been truer than they are today.”
Jamie continues, expanding on what drove him to join the family business: “As a keen karter, it was inevitable that I would join the company, given our heavy
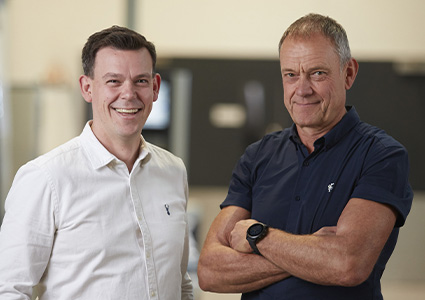
involvement in motorsport. Growing up, I was always around the business, and with my father as my chief mechanic for karting, I had no choice but to follow him around the shop floor. Working with family has its challenges, but I believe it creates a bond that fosters openness, which can easily drive success.”
As the company approaches its 40th anniversary, Jamie goes on to highlight some of the elements that have contributed to its longevity: “I believe our success has been driven by a few key factors. First and foremost, our commitment to innovation has kept us ahead in the highly competitive composites industry. We continually invest in advanced manufacturing techniques, materials, and processes to ensure we deliver cutting-edge solutions to our clients.
“Secondly, our dedication to quality and precision has been a cornerstone of our reputation. From motor sports to aerospace, we work with industries where performance and reliability are non-negotiable, and our ability to consistently meet and exceed expectations has earned us long-term partnerships. Another crucial factor is our adaptability. Over the years, we’ve evolved with market demands, embracing new technologies and diversifying our capabilities while maintaining our core expertise.
“Lastly, our people are at the heart of our success. We have an incredibly skilled and passionate team, and by fostering a culture of collaboration, continuous learning, and problem-solving, we’ve built a workforce that drives the company forward. Ultimately, it’s this combination of innovation, quality, adaptability, and talent that has enabled KS Composites to thrive for so long.”
Jamie then introduces the latest addition to KS Composites’ portfolio of products and services: “I’m excited to talk about our latest project, a groundbreaking wind propulsion system designed to revolutionize marine transportation. In conjunction with GT Wings and A20 Manufacturing, we’re leveraging our expertise in advanced composites to develop an innovative, high-performance wing sail: the AirWing. The technology will significantly enhance fuel efficiency and reduce emissions for commercial shipping.
“This system uses cutting-edge aerodynamic design and lightweight composite materials to harness wind power more effectively than traditional sails. Unlike conventional soft sails, the AirWing offers superior efficiency, automated control, and adaptability to varying wind conditions, making it a viable solution for large-scale commercial vessels.
“From a sustainability perspective, the impact is substantial. The shipping industry accounts for nearly three percent of global carbon emissions; the AirWing system has the potential to reduce fuel consumption by up to 30 percent, depending on the vessel and route. By integrating wind-assisted propulsion, we’re helping to lower dependency on fossil fuels and support the industry’s transition toward net-zero emissions.
“At KS Composites, we are committed to engineering solutions that drive sustainability without compromising performance. This technology aligns with global efforts to decarbonize maritime transport and represents a significant step forward in making shipping cleaner, greener, and more efficient.”
On the topic of sustainability, Jamie then highlights the company’s approach to the integration of more sustainable bio-polymers: “As part of our commitment to sustainability and reducing our environmental impact, we have enlisted the expertise of Auditel, a leading cost, procurement, and carbon solutions consultancy, to help us on our journey to Net Zero. Working closely with them, we are identifying key areas where we can improve energy efficiency, reduce carbon emissions, and implement sustainable practices across our operations.
“We also work closely with our materials supplier, SHD Composites, and are actively exploring the integration of bio-based materials and resins into polymer composites to enhance sustainability without compromising performance. Bio-based resins, derived from renewable sources like plant oils, can replace conventional petroleum-based resins, reducing carbon footprint and reliance on fossil fuels.
“These resins can be combined with natural fiber reinforcements, such as flax or hemp, to create lightweight, high-strength composites suitable for various applications. The key advantages include improved environmental impact, enhanced recyclability, and potential biodegradability. Additionally, bio-based composites often offer comparable mechanical properties to traditional materials while reducing overall lifecycle emissions. By incorporating these materials, we aim to support the shift towards greener manufacturing and contribute to a more sustainable future in high-performance engineering sectors.”
As well as working to improve the materials it utilizes, KS Composites has also invested significantly in improving operational processes, as Jamie explains: “We are embracing smart factory technologies as part of our commitment to continuous improvement and digital transformation. Advanced manufacturing is evolving rapidly, and by integrating data-driven solutions, we are enhancing productivity, efficiency, and quality across our operations.
“One key area where we are leveraging smart factory principles is in data management and process automation. We utilize real-time monitoring systems and Internet-of-Things-enabled sensors across our production lines to track performance, material usage, and environmental conditions. This data allows us to optimize workflows, reduce waste, and improve predictive maintenance, minimizing downtime and ensuring consistent quality. Additionally, we are implementing digital twin technology and creating virtual models of our manufacturing processes to simulate and refine production before physical implementation. This enables us to anticipate potential challenges, streamline operations, and accelerate innovation.
“Our goal,” Jamie concludes, “is to create a fully connected, intelligent manufacturing environment that not only improves our internal processes but also enhances the service we provide to our customers. Digital transformation is an ongoing journey, and we are committed to staying at the forefront of smart factory innovation.”