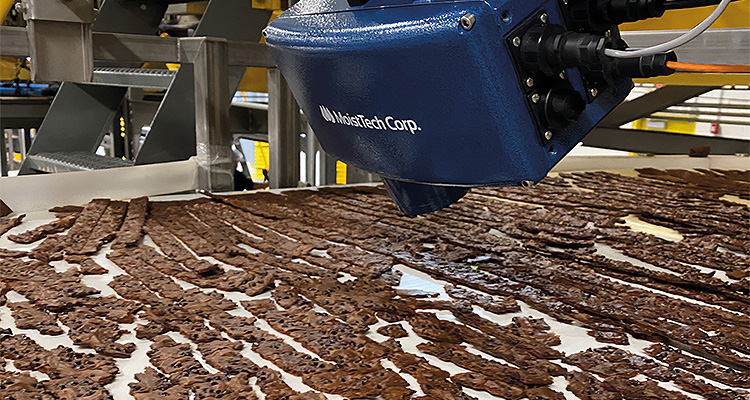
How MoistTech’s leading sensor technology can improve your manufacturing process
In 1975, John Fordham and Roger Carlson founded MoistTech. The Sarasota, Florida-based manufacturer sought to overcome common industry issues such as waste, low-efficiency, and inconsistency.
It went on to pioneer the industry’s first patented method of non-contact, non-destructive moisture analysis and detection. With the passing of time, MoistTech has continued to refine its technology.
Today, the company’s near-infrared (NIR) equipment is chosen by market leaders all over the world, providing reliable moisture measurement and controls that manufacturers can trust. On-line and at-line sensors for real-time process control – that’s the name of the game, and MoistTech is most certainly winning it.
With numerous applications, its proprietary technology enables customers to gauge real-time processes and gather data regardless of gaps and interruptions (for instance, material variations: color, height, particle size) in product flow. As a result, MoistTech’s solutions are valued by a diverse range of clients across open and niche disciplines: adhesives, biomass, chemicals, coatings, food, minerals, renewable energy, textiles, and wood products.
In 2021, we caught up with CEO John Fordham. Back then, he told Manufacturing Today about the company’s soon-to-launch Linear Belt-Driven Slide, a traversing system designed to allow multiple sensors to concomitantly move back and forth over a manufacturing line.
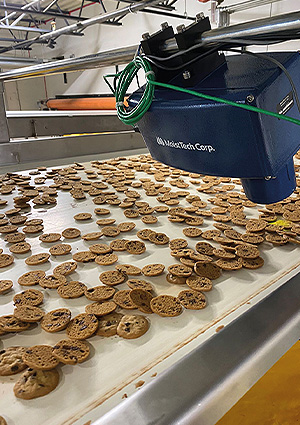
“NIR technology is specific and stands out from other moisture control technologies as it never comes into contact with the product and provides instant, accurate, and repeatable results,” he divulged in 2021. “By harnessing this core technology, we can produce variants and new, more efficient products like the Linear Belt-Driven Slide.”
But that was two years ago. To get the latest on MoistTech and find out how the launch went, Marketing Manager, Sarah Hammond, recently joined us in conversation. Before we dive into that, though, it would be prudent to cover some of the reasons why moisture control is so important in the first place.
“Depending on the material being manufactured, moisture can play a sizable role in transportation costs, product consistency and quality, plant efficiency, equipment wear and tear, and more,” begins Sarah. “Immediate Return on Investment (ROI) is seen with installation of a moisture measurement system as plant controllers can instantaneously see the reduced waste and energy usage, as well as the overall increase in product quality.
“Consistency is the ultimate test of quality,” she explains. “Therefore, figuring out the necessary requirement of manufacturing a product and consistently achieving that standard is paramount. Moisture control is a huge determinant to the overall quality of a product, and as such we give you the data you need to maintain a level of consistency while also improving quality control processes.”
For those still not convinced, take the example of wood pellets. Several metrics must be considered when it comes to making a quality pellet. As Sarah points out, something to know about pellet mills is that they’re only as efficient as the consistency of the material being inputted. Multiple factors must be considered: wood species, die specifications, grind size, geometry of the grind, conveyance, and binder requirements, among others.
Improving customer experience
However, one often overlooked metric is the moisture rate of the biomass. Users find that changing the moisture percentage by as little as one percent will make a noticeable difference in the final pellet quality. In wood pelleting specifically, explains Sarah, if the moisture rate trends upwards the amperage of the motor swings upwards, too.
Conversely, when the moisture rate drops, the amperage falls significantly. This bouncing of the amperage rate can have a detrimental effect on the production capacity of the pellet mill. In fact, users report production rate losses of more than 20 percent – just because the inbound biomass wasn’t a consistent moisture.
That’s where MoistTech comes in. According to Sarah, NIR moisture control enables users to adjust the programming of dryer systems to counter the aforementioned issues and not only boost production rates, but also produce a higher quality pellet.
“Since we last featured in Manufacturing Today, we’ve implemented two new pieces of equipment for our customers,” notes Sarah. “On top of that, we’ve also increased our presence at trade shows, meeting new customers and increasing our market reach. The trade shows are for industries we’ve been present in for quite some time, but we’ve not necessarily capitalized on the shows themselves before.
“They allow us to get in front of a whole new group of professionals to show how moisture measurement is a crucial aspect in their processes. Looking ahead, we will be searching for new shows that will no doubt help launch us further towards market domination, as we share the latest advancements and progressions in NIR technology.
“By revamping the look of our marketing materials and advertising, moreover, we’re on a mission to stand out from the competition,” she goes on. “Naturally, we also continue to come up with ways to improve our customers’ experience and always ensure that our equipment will stand the test of time.”
Product innovation
What about the Linear Belt Driven Slide that John was so enthusiastic about in 2021? “We successfully launched that product in November 2022, enabling customers in the paper and converting industry to measure moisture at multiple points throughout their processes,” Sarah reveals. “The slide gives customers the option to customize the sizing needed to fit their web and equip the entire line with multiple sensors.”
Instant data monitoring
Six months on, MoistTech is continuing to blaze new trails in the manufacturing measurement sector. Recently, for instance, it debuted a new Food Grade Sanitary Valve Connection, enabling the measurement of moisture content in soft cheeses, chocolate, sauces, condiments, and more.
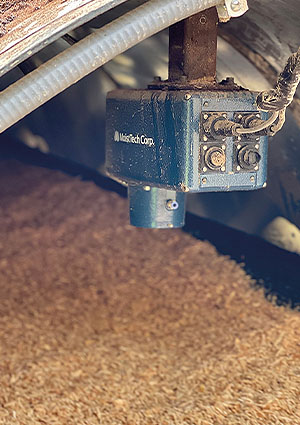
“The ability to efficiently monitor moisture content in these types of food applications is usually very time consuming,” she explains. “But with an instant, in-process ability to measure moisture content, manufacturers can now seamlessly tie our product directly into their pipeline for instantaneous data monitoring.
“The new piece of equipment is a connection unit that attaches to the food grade moisture sensor, providing a pipelined process across the measurement window and thus offering instant data back to a display module. Utilizing the Food Grade Sanitary Valve Connection promises to improve efficiencies, minimize waste, and cut energy costs.”
Its products are second-to-none, there’s no doubt about that. But we’re keen to learn more about the company manufacturing them. Fortunately, Sarah’s on hand to give us the lowdown. “We’ve been family-owned for more than 45 years,” she reflects. “We continue to serve our customers based on an ability to consistently evolve alongside advancements in technology and changing customer needs.
“With MoistTech, customers are more than just a sensor; they’re the backbone of our company, and meeting their production needs in moisture control is our passion,” avows Sarah. “Have you ever got used to a product and how well it works, just to find out the company has been sold and the product isn’t the same anymore? That will never happen with MoistTech; we pride ourselves on directly serving our customers and improving long-lasting relationships.
“Our process is pretty straightforward: we gauge the issues that our customers are having and identify how we can implement a solution. All our sensors come pre-calibrated to each customer’s exact product requirement and are manufactured near Boston, Massachusetts before being sent to Sarasota for calibration. Each sensor comes with full instructions and a USB with unlimited licensing software, meaning it can be offered out to multiple employees.”
It’s been great catching up with Sarah. For one, it’s demonstrated that MoistTech is most certainly fulfilling John’s ambitions of being “the best option for anyone looking for moisture measurement and control solutions.” To continue on that trajectory – and to get ever closer to that goal – Sarah says that the company will only be doing more.
“More shows, more interaction, more marketing: we want to grow our presence in multiple ways, whether that’s with boots on the ground at trade shows or by increasing our online presence,” she concludes. “We’ll also look at growing the team, developing Original Equipment Manufacturer (OEM) partnerships, and adding to our proven track record of being a trusted partner in the field.
“We’ve been – and will continue to be – on an upward trend regarding near-infrared moisture sensing equipment. Solving moisture problems with the customer in mind has always been our focus – and that won’t change. But we will roll with the times, continuing to evolve as moisture sensing technology advances, thereby ensuring, as a company, we will never become outdated.”