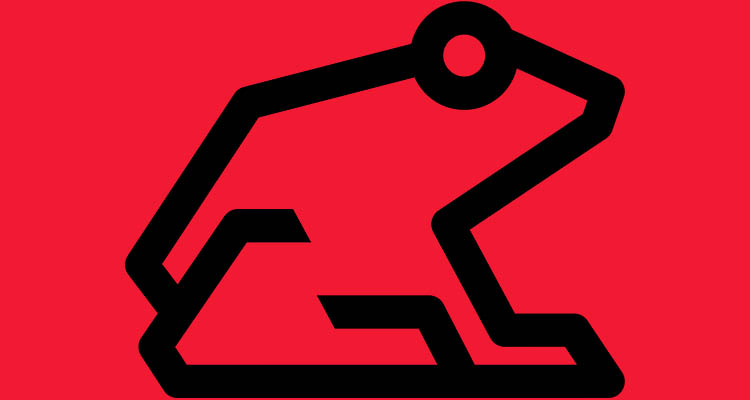
How RDM ESKA has stayed at the forefront of sustainable innovation for over a century
With a storied history that stretches back well over a century, RDM ESKA has grown from two small mills making strawboards to a market leader with a global network of five production units, providing solid board for everything from hardcover books and jigsaw puzzles to games and luxury packaging for a plethora of brands. The business has been at the cutting edge of the industry for much of that time. ESKA began using recycled paper as a raw material as early as 1934 and switched its entire business over to fully recycled materials in 1971.
Since 2021 ESKA has become part of RDM Group, the European leading packaging board producer. The group is committed to the development of cartonboard solutions based on recycled fibers. Sustainability is one of the core values on which RDM Group’s business model is built.
Robert Schreurs, ESKA Technical Support Manager, gives more detail: “We make solid board in calipers between one and four millimeters, consisting of three or four layers. The layers enable us to adapt the colors and materials used, which gives the products the look and feel. The layers are also what gives the product its technical capabilities.
“We have a broad range of products, starting with the grey board, which is the most common product. It’s a fully recycled product that customers can laminate. A book is a good example, as the printed cover is wrapped around the board to complete the product. We also have a full suite of color boards which can be decorated with debossings, hot foil stampings or screen prints to give a more natural, minimalist feel. These can be used for luxury packaging for jewelry, fashion, cosmetics or wine and spirits for example.
“Instead of the highly printed board you see,” Robert continues, “we promote alternative solutions that utilize different layer and color combinations. We can offer a more luxurious product that is not only completely recyclable but also made from 100 percent recycled material.”
As well as recycled paper, ESKA is continuing its tradition of raw material innovation by incorporating cotton fiber recovered from jeans. Robert explains: “Jeans are already widely recycled, approximately 92 percent of a pair of jeans can be used as spinnable recycled fibers or insulation for automotive and electric equipment. Of the remaining eight percent, around six percent is buttons and zippers, and the remaining two percent would previously have been incinerated, but now we can use it to make a beautiful product. Examples include luxury packaging, catalogue covers, labels or POS for the fashion industry.”
Reuse and recycle
Bert Bodewes, Manager of Social Responsibility at ESKA, expands on the company’s commitment to sustainability, as this area is one of the core values on which the RDM Group business model is built. It embraces the principles of the circular economy, based on regenerative resources and circulating materials. “Paper making is sustainable at its core, as it is biobased and biodegradeable, however, there aren’t sufficient timber resources to meet the demand for this type of product if used in a linear business model. Recycling and upcycling are big steps to ensure the sustainability of the operation. We use low-grade waste material to make high-grade, long-lasting products which are sometimes reused, such as books and games, which can be passed on.
Enhancing operations
“Energy consumption represents another significant area of improvement,” Bert continues. “We are constantly researching ways to be more efficient and looking for new solutions. We have one of the most efficient board machines in the world for example. We are also implementing a circular process to capture and transform waste into energy. Regarding water usage, we operate one of the world’s first closed water loops. Eliminating this waste is an important achievement in a world where water scarcity is increasingly important. We are also developing the production of bioplastics as a byproduct from the waste streams. This aligns with our philosophy of upcycling and will hopefully positively impact other industries.”
Robert picks up from Bert, adding: “We are also the only solid board manufacturer to be a certified B-Corporation. This demonstrates a really high standard, and we scored highly across the board. While it’s easy for a business to articulate the right things, it’s much harder to do the right thing, but it makes a massive difference.”
While its products are designed to be renewable, recyclable, and recycled, innovation in the business extends beyond raw materials. ESKA is in the process of completing an automated packing facility in its Sappemeer facility. Brian Oost, Managing Director, sheds some light on the investment: “This automated packing line is about efficiency but also about working conditions. In this specific case there are two board machines that will feed the line ensuring we can always meet the output demands of our customers.
“Recently we have also opened a new cutting facility in Suffolk, Virginia,” Brian continues. “We moved out of a rather aged building in Chesapeake where we have been for at least 40 years and into a state-of-the-art facility in which our order flow is fully optimized. As with the European plants, this will increase our efficiency, but it’s also about the people and creating a light and spacious environment to work in.” For Eska, this is not only a move but also a commitment to long-term strategic growth in the United States and Western Hemisphere.
The business has also been investing in smart factory technologies for some time, and Robert highlights some key uses: “We have a lot of data at our disposal already. We have been using this for some time to help optimize efficiency and quality control. We are also automating any areas that we can. The next major development will be in implementing artificial intelligence (AI) which we are currently exploring. I think we are just at the beginning of what will be possible, so we are researching all these avenues.”
“We are in a great position to capitalize on this,” Bert adds. “Because we invested in a digital processing platform 25 years ago, we have enormous databases with our historical data which AI will use to inform its decision-making processes. A lot of our competitors are only just beginning to think about working with AI and don’t have this reserve of data that you need.”
Robert responds, highlighting a further interesting use case for smart technology: “We are also looking at implementing some of this technology into the product itself. It can be used in a multitude of ways; an obvious example is in the packaging of high-end luxury goods. We could integrate a sensor that will tell you if a package has been opened or if its weight has changed. It could also be used to help discern genuine products from counterfeit. Also, in puzzle games which is one of our biggest markets, you could have a device that would connect people that aren’t in the same physical space to play together. There are many directions this could go in and we are exploring some very innovative solutions.”