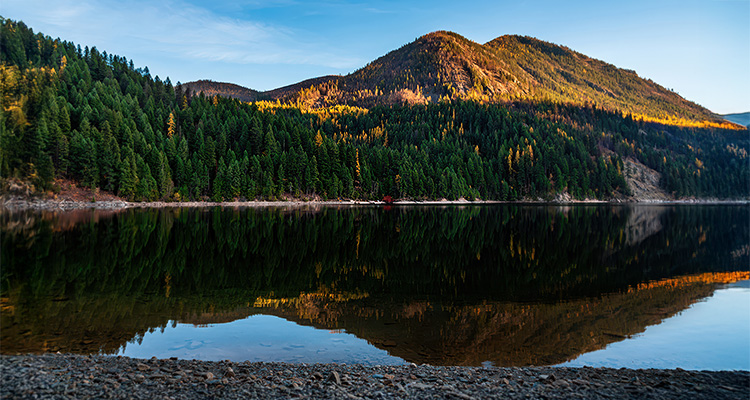
How Vaagen Timbers is transforming the industry through its innovative use of mass timber
Vaagen Timbers, founded in 2017, is based in the picturesque forest town of Colville, Washington. Manufacturing Today caught up with Russ Vaagen, Founder and CEO, to get some insight into the company’s operations and its sustainable approach: “We manufacture cross-laminated timber panels and cross-laminated beams,” he begins. “We take structural lumber and transform it into mass timber, which includes these panels and beams, and we use this to construct a variety of buildings, ranging from small residential structures to mid-rise 18-story buildings. It’s a broad market segment that we serve.”
As well as the company’s transformative products, Russ explains that one of the business’s biggest strengths is its relationship to the land and how it manages the forests it relies upon: “I come from the forest product world. My family has a series of sawmills that have been running since the 1950s, and I was Vice President of that operation for about 15 years. I then started this business to build upon what we had done in my family’s business, but also due to the situation in the United States. We have a lot of wild forest land, and because of that, we are susceptible to catastrophic wildfires. We’ve even seen urban fires in recent times. This often gets attributed to climate change, which is obviously affecting it but is not necessarily the root cause of the issue.
“The reason is we’re not managing the flammable fuels in federal lands. Typically, in Canada or Europe, for example, land that is owned by the government is managed for its resources. Environmental restrictions are put in place, and then management takes place based on these restrictions. In the United States, we did this for about 50 years. Then, after public outcry, a loophole was established that allowed people to file lawsuits against forest management. In the late 1980s, management was very aggressive, but by the 1990s, it had almost stopped completely. Today, we’re in a situation where we’ve been constantly putting out wildfires but not removing the fuel that is growing each year.
“I have been working to educate people about the benefits of responsible forest management. When we thin the forest out, leaving the biggest and best trees, we are left with a naturally functioning and appearing forest that mitigates a lot of the worst risks. We’re now learning how to manage forests in harmony with natural methods.
“When we focus on thinning and forest restoration, it creates material as a byproduct. We have technology that allows us to utilize this material, which might be smaller trees/logs and glue the products together to create large elements in a very efficient and environmentally friendly way. By using the byproduct of what we’re doing, we’ve also created a circular economy that helps rural communities. Then, we build energy-efficient and environmentally friendly homes in our urban areas. There are multiple benefits to operating in this way, which is why so many people are excited about this product.
“With the advances in 3D modeling technology, we can fully design a building, manufacture all the parts, sequence them, and then deliver them to the site. The traditional construction model involves taking materials, delivering them to the site, and then using a 3D model to assemble those materials on-site. You can create a great building, but it’s inefficient and generates a significant amount of waste. What we’re doing is bringing many of these steps into our factory, using the best technology available to deliver highly energy-efficient and environmentally sensitive products to the marketplace. We’re still working with steel and concrete, but we’re now incorporating mass timber into the mix to enable lighter and greener buildings.”
Russ then goes on to explain in more depth the benefits that Vaagen Timbers’ 3D modeling brings: “Because the construction is designed and materials are delivered in sequence, even for people who have never worked in this way, it is significantly easier, more efficient, and even quieter. For example, for our Timber House project in New York, which was a typical urban brownstone building, a number of neighbors remarked on how quiet and undisruptive it was. This was because each day we would have a delivery scheduled to meet the truck crane, which would then assemble the materials. This method required significantly less labor and heavy machinery operating constantly on-site. Some neighbors would leave for the day and return to find a new story of the building completed.”
In addition to a number of projects for tech companies, Vaagen Timbers has recently completed a significant project for Microsoft’s new headquarters. Russ has observed an increased demand within the tech sector: “What we see with the rise of AI and the rapid development of data centers is a substantial move toward mass timber structures. We think it’s a brilliant way to proceed because there are numerous benefits. Distribution centers are another area that presents significant opportunities. Companies like Amazon are growing and expanding; they are looking for ways to make their construction faster, more efficient, and more environmentally sensitive.”
Russ then concludes, highlighting what’s in store for Vaagen Timbers in the years to come: “In the next five years, I expect awareness to be much greater as people will have interacted with many more buildings constructed with these materials and methods. We’ve built a lot of schools and banks that communities will engage with. Seeing people react to the buildings is amazing because people love them. It’s not often you see someone gravitating toward a concrete column, wanting to touch it. But if you have a nice, smooth, beautiful piece of wood, people will, because there is that connection to life. This will lead to greater adoption of these products and projects.
“Over that time, we will also be building larger and larger projects, which will lead to growth for ourselves and the industry. In ten years’ time, though, I foresee a situation where mass timber is regarded on par with steel and concrete. Wood is one-fifth the weight of concrete but offers the same structural support. You can build nearly identical buildings with substantially less weight. This carries cost savings across the entire project, particularly in the transportation of materials. As these processes and materials become more established in the industry, I think we will see enormous opportunities open up.”