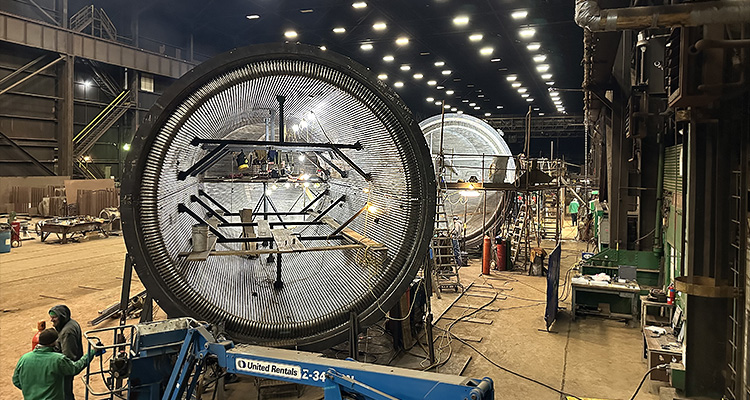
How Woodings Industrial evolved from a family-run forge into North America’s steel industry backbone
Primarily serving industries like steel, power generation, petrochemicals, and pulp and paper, Woodings Industrial is a well-established manufacturer based in Mars, Pennsylvania. The company is known for its specialized industrial equipment and components, which are crucial in heavy manufacturing processes. As one of the oldest continuous family-operated businesses in North America’s steel industry, Woodings Industrial boasts a rich history.
“Woodings Industrial traces its history back to 1872, when it was founded by my great-great-great grandfather, Emanuel, an immigrant from Wales to the US,” begins Rob Woodings, President. “He and his two brothers were coal miners, a typical Welsh trade, but both his brothers unfortunately died in a mine collapse. Emanuel then started a forging operation, which at the time consisted of only an anvil, a hammer, and a furnace. He forged whatever parts the neighbors needed, such as hoses and door handles. When considering the technological advancements of the late 1800s, railroads were akin to AI today: everybody was building railroads. However, railroads faced a significant challenge with trains derailing due to iron rails and the rail spikes that could not hold the rails down. Consequently, Andrew Carnegie introduced the Bessemer process for steel in the US, which he adapted from the UK, to produce steel rails in Pittsburgh at Edgar Thomson Steel Works. Parallel to that, Emanuel invented and patented the rail anchor, a more efficient and effective way to anchor a rail to the ties. This marked the start of the company, known as Woodings Verona.
“Fast forward to 1900, Woodings Verona had 6000 employees building railroad equipment. From then until 1953, the company was heavily involved in defense operations during the wars. My grandfather was involved in the business while my father served during the Korean War. Afterwards, he returned home and started Woodings Industrial in 1957, focusing on building steel mill equipment. This meant that Woodings Verona continued to produce railroad equipment, while the adjunct company, Woodings Industrial, expanded its offerings. Through the 1960s and 1970s, we entered the oil field tubular business and hydraulic cylinder business, as well as steel mill equipment, primarily blast furnaces, which is one of our core areas today. The family sold the rail equipment division to the Bud Company, part of the German company Thyssenkrupp, but retained the steel mill business that I currently run,” he continues.
Now in its fourth generation, Woodings Industrial is led by Rob himself. Despite his passion for the company, he has gained experience across various industries and roles throughout his extensive career, before returning to the family business. “I began working in the company in 1975, starting by pushing a broom and gradually working my way up through machining, fabricating, and assembly. My last job at Woodings Industrial was in 1984, when I operated a 3.5-inch upsetter in North Little Rock, Arkansas. Following that, I decided to go to college, as I found it more appealing than running an upsetter. Upon completing college, I attended law school and worked for a large corporate law firm. When my dad got sick in 1994, I spent some time working in Gary, Indiana with US Steel and other steel producers before returning to Woodings Industrial, where I have now been for 31 years. I sold the oil field tubular and hydraulic cylinder businesses, choosing to focus on the steel industry and blast furnace equipment, and I have been dedicated to building those portfolios ever since,” he reveals.
Under Rob’s leadership, Woodings Industrial has experienced substantial growth and significantly expanded its range of solutions, notably through acquisitions. “Between 1994 and 2005, we developed our collection of blast furnace equipment. The integrated steelmaking process entails components like coke plants, blast furnaces, and basic oxygen furnaces (BOFs). To support these operations effectively, we developed a core group of equipment that is integral to blast furnace operations. By 2005, we had built every piece of equipment on a blast furnace, from the charging systems to the taphole drill, including all the valving systems and probes. As a result, we became the leading supplier of blast furnace equipment design and manufacturing in North America. In fact, we even took those products all over the world, installing equipment in locations as diverse as India, South Korea, Australia, Brazil, Chile, Peru, Argentina, Serbia, Romania, and more.
“In 2007, as we continued to grow, we acquired a Pittsburgh-based company named Munroe Incorporated (Munroe), active since 1835. Munroe specializes in boilers and BOF hoods, and before we acquired it, its product mix was approximately 30 percent BOF hood systems for the integrated steel industry and 70 percent boilers for coal-fired power plants. By adding Munroe to our portfolio, we can now provide BOF hood systems and build coal-fired boiler systems for power plants, alongside boilers for petrochemical operations and other systems that require boilers,” Rob informs.
Woodings Industrial’s comprehensive offerings were further enhanced in 2023, when the company acquired Superior Machine. “Based in South Carolina, Superior Machine is the leading designer, manufacturer, and installer of electric arc furnace (EAF) steelmaking systems in North America. It is worth noting that the steel industry is bifurcated into integrated and mini mill operations. At Woodings Industrial, we operate with approximately 60 percent focused on mini mills, and 40 percent on integrated systems. For the EAF side of the business, we create all the furnace systems involved in the process, from charging operations to the caster, however, we do not engage in finishing and rolling work. Not only do we design and build these systems, but we also install them. To that end, we have two field operations: one is unionized, while the other is non-union. On the integrated side, all work is unionized, and we perform boilermaker field construction. As for the mini mill side, we have a dedicated field group that manages installation and service operations.
“In North America, there has been a major push to reshore manufacturing, and we are ideally positioned for that, thanks to our six manufacturing plants, 400 employees, 30 engineers, and our field construction team. Those team members are full-time employees at Superior Machine, with support from various union halls associated with Woodings Industrial and Munroe. Superior Machine has given us a prime entry into the mini mill business, being a premium supplier of EAF equipment, among other products. While we already had a strong position on the integrated side, we aimed to strengthen our presence in the mini mill sector, as the industry is currently in a state of flux between integrated and mini mills. Thus, we wanted to ensure we had a foothold in both areas,” Rob concludes.
From its roots as a forge to its global dominance in steel equipment, Woodings Industrial has cemented its legacy as a pioneering force in heavy manufacturing.