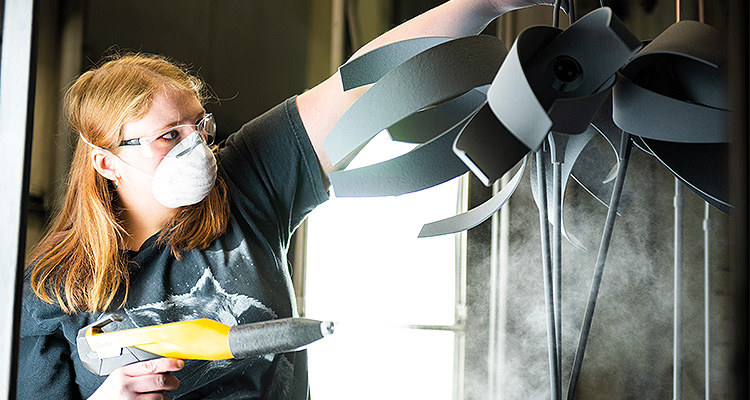
Hubbardton Forge stands to continue as one of the oldest commercial forges for many years to come
There’s a stellar collection of around 240 designers, makers, and doers, who are responsible for the day-to-day operations of Hubbardton Forge (Hubbardton). The organization, which has been producing handcrafted, artisanal lighting solutions since 1974, is also one of the US’ oldest and largest continuously operating commercial forges. Manufacturing Today last sat down with the company in early 2022, so we’re touching base once again, with Steve Wiegers, Vice President of Operations, and Louis Rousseau, Process Engineering Manager, to hear how things are going.
“The last 12 months have given us an opportunity to settle back into normalcy after the whole Covid impact,” begins Steve. “We weathered the storm better than most, and never actually saw our on-time delivery service levels drop below 90 percent, or our lead times exceed four to five weeks, and we’ve managed to fully recover. We feel like we’re all kind of past it now; the challenges in sourcing raw materials and the surges in demand that many manufacturers experienced, and we’re ready to shift our focus back onto the elements that were difficult to prioritize during that period. Chiefly, we’re starting to think about new equipment again, and other investments that we can implement to improve both the plant and the business overall.”
“Of course it was a difficult transition,” agrees Louis, “with all of the changes that we had to adjust to, but I almost think it brought us closer together as a group. Design, engineering, production, and sales, we’re obviously all under one roof here. However, from a development point of view, I really feel like those internal relationships have become even stronger over the past couple of years.”
Hubbardton has recently created three new custom finishes that have proven to be incredibly popular among its clientele, but they have not come without a new set of challenges. “On the eco-friendly side,” Louis explains, “these new finishes enable us to replicate the plated approach that is more common overseas, without having the detrimental impact on the environment. Ours are chrome-based, which is all powder coated, and through working with our partners and vendors, we’ve succeeded in keeping the presence of triglycerides to a minimum, during both the spraying and baking steps. Our emissions are very low, as the products are essentially going through a curing process.”
Community focus
Besides this, Hubbardton has already transformed its in-house lighting to LED solutions, worked on reducing its fossil fuel dependency, and taken steps towards more environmentally friendly packaging options. Furthermore, the company also possesses a centrifuge and water treatment process, which enables it to pass wastewater onto the local town’s facility without any chemicals or physical waste.
“As most of our competitors are based overseas, it’s hard to say where their priorities lie in terms of sustainability,” Steve adds. “But for us, as an enterprise producing domestically in the US, we feel a deeper level of responsibility for our local community, and the overall state of Vermont. It’s something that our employees and customers value, so we ultimately care very strongly about it. We want to be a leader in the area, and packaging is an area that we’re continually searching for advancements in. It’s not an easy one, but an opportunity we’re really excited about.
“Our culture of innovation is wholly inclusive of all of our departments, it’s a real collaborative effort between the sales, design and engineering teams. The former two work together to identify what the current trends are and what the market is looking for, and the latter will then produce samples of different looks and styles based purely off the conversation. This is typically followed by a back and forth to fine tune all the details, so we can fully explore how we can create a specific look in-house, in an environmentally friendly way.”
This ‘it takes a village’ approach extends farther than the company’s walls, as Hubbardton also puts a great deal of emphasis on its ties and presence in its local communities. “A key area of our focus of late, has been connecting with the local high schools in our county,” Steve explains. “Through engaging with the students, we’re spreading awareness of the potential opportunities that a career in manufacturing can offer them; not just in production, but also accounting and design roles, for example, whether they plan to study for a two or four year degree, or want to get straight into work.
“Similarly, a longstanding, family-owned home center not too far from us recently burned down, so we reached out to offer them temporary jobs during the rebuild, among other resources, such as office and warehouse space. We just want to help out wherever we can. The local tech center runs an engineering course, and we’ve been working alongside its students to provide a real-life application project at the forge. They are currently developing us an automated guided vehicle, which will be able to help move materials around the site.
“Looking ahead,” Steve concludes, “we’re not just thinking about execution right now. We certainly want to be a leader when it comes to design and innovation on the product side, but we also want to encourage greater creativity in approaching our operations and processes. We’re considering which potential investments will provide us with greater capabilities, and which are the more sustainable options. There’s been a definite increase in demand for custom products, which we, as a domestic manufacturer, see to be a huge competitive advantage. We can modify practically anything that we do, and still turn it around in a relatively short lead time, which is somewhere that I believe we’re really going to stand out in the future.”