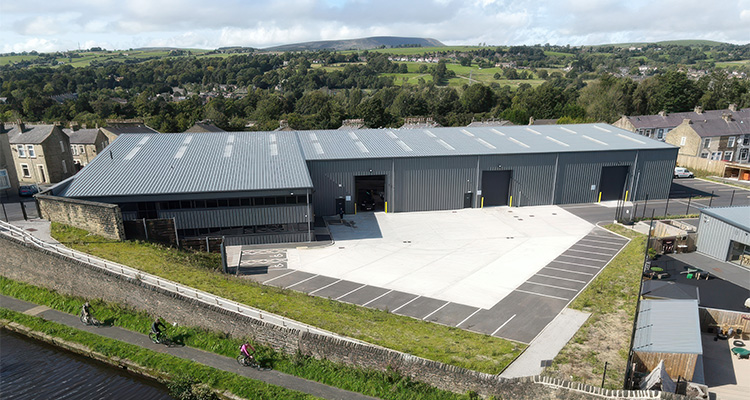
In preparation for a record year ahead, Sugden is driving operational efficiency
Founded in 1973, Sugden Ltd has evolved significantly to become one of the world’s leading designers and manufacturers of hotplate plants for producing a range of products like pancakes, English muffins, crumpets, potato cakes, farls, and Welsh cakes. The company added stroopwafels, Belgian waffles, funcakes, and soft waffles to its portfolio in 2021 through production lines under the VanderPol Waffle Systems (VanderPol) brand.
With more than 50 years of experience and an international reputation for custom-configured, high-quality prover and griddle solutions, it’s no surprise that Sugden has grown tremendously in recent years despite the disruption caused by the Covid-19 pandemic. Manufacturing Today spoke with Chris Baldwin, Managing Director, in early 2024, so we’re keen to catch up with Chris to learn how the business has evolved over the last 12-to-18-months.
“It feels as though we’ve finally turned a corner from the difficulties caused by the pandemic, and in terms of sales and component supply, we’ve grown in Europe
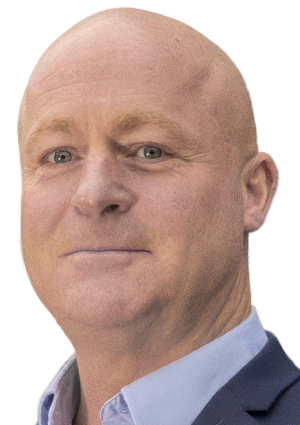
and especially in North America over the last couple of years,” Chris opens. “In the last 12 months specifically, we’ve seen a strong increase in orders, and with several investments in streamlining our processes and enhancing efficiency, including a new assembly area within our workshop, we’ve been able to execute these orders seamlessly.
“We’ve done a lot of traveling to North America and Asia to pursue enquiries, meet customers, and get orders over the line. With two lines just landed in North America and there’s another huge machine being commissioned in the Middle East. On the VanderPol side of things, we’re gaining traction in the market for these products and establishing the best practices to grow the brand from both a sales and awareness perspective.
“We’re currently implementing ProgressPlus, a new CRM system, which will be fully embedded by the end of the year,” he adds. “By adding this system, we’re hoping to further streamline operations and create even more efficiencies, but we’re not stopping there. We’re evaluating each department to identify improvements and then giving ourselves a timeline to implement new processes that make an impact.”
However, Sugden’s product range and order book are not the only aspects of the business that have grown. “When it comes to staff, we’ve invested in both new and existing people to ensure we’ve got the best people in the right places as we continue to grow,” Chris explains. “Many of our staff started off as apprentices and we remain committed to supporting apprenticeship schemes. We’ve also added a quality control engineer to oversee the quality of parts we source externally.
“Similarly, we’ve streamlined our supplier base to focus on creating positive, long-lasting relationships with key partners. Alongside external suppliers, we’re also taking back some control by investing in a new 5-axis CNC machine to boost resilience and enhance our in-house capabilities.
“In terms of projects, we are installing a large capacity pancake line for a client in North America. Our capacity was 19,000 pancakes per hour, but we’ve exceeded this figure by creating a product line that produces 30,000 pancakes per hour. We’re super excited about this development and we believe it will give us a huge opportunity to expand our offering to other high-capacity customers.”
While on the topic of new product development, Chris shares a glimpse of a new product launching in 2026, although the details are still under wraps. “We currently have a new product line under development, which we’re committed to launching next year at Interpack, a processing and packaging exhibition held in Germany,” Chris says. “Whenever we explore new product development, we always assess the market to identify where demand lies. Our historical product lines for English muffins and crumpets are slightly niche, so we now focus on creating products for a global audience.”
Offering some of the most efficient baking lines in the industry, Sugden is also embracing sustainable practices. “We use a special insulation system to maximize gas efficiency, with our lines emitting over 30 percent less gas than our competitors,” Chris states. “We’re constantly pushing ourselves to improve further. We’ve switched repeat motion from pneumatic to servo systems to reduce our consumption of compressed air, and we’re currently trialing electrical emitters rather than gas burners, which are proving to be successful so far and not too heavy on the electrical grid. As demand for more sustainable systems continues, we’re hoping to receive some orders for fully electric lines later this year.
“We’re also aiming to be paperless by the end of 2025, with engineers then using computers to analyze drawings instead of printed drawings that may have since been updated. Although this requires significant investment, it’s one that will pay off almost immediately by further streamlining our production process.”
From speaking with Chris, it’s clear that he’s experienced challenges within the business and is pleased to see Sugden returning to its industry-leading position. Considering the investments made in streamlining processes and enhancing efficiency, we’re keen to hear what’s next for the company.
“Our financial year for 2025 begins in May, and the year for 2025 into 2026 looks like it will be a record-breaking one,” Chris states. “We’ve got a phenomenal order book and with the improvements we’ve made to our operations, we’re on track to execute these orders more efficiently than ever. After the turmoil and inconsistency of the pandemic and supply chain, it’s great to be back in a good place, facing a record year, and I genuinely feel that the business is in the best place it has ever been since I took over the small mill in 2014.
“We’re also engaged in conversations about potential acquisitions, seizing opportunities to grow and gain more traction in the market,” Chris concludes. “To support this growth, we’ll hire additional people and apprentices while supporting the development of current staff. Although we’re not entirely driven by numbers, it’s good to have a target, and we have an ambitious plan to double our turnover by 2027-to-2028, which I believe we can achieve, especially with our new product range launching next year.”