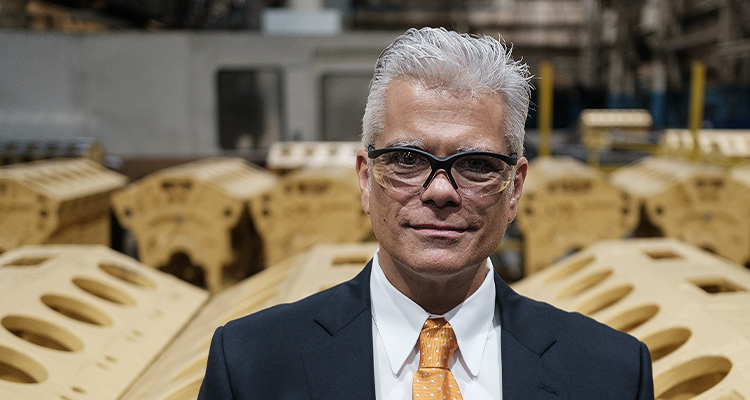
Ingersoll Machine Tools’ CEO shares the company’s fascinating projects from around the globe
Originally established in 1862, Ingersoll Machine Tools (Ingersoll) has successfully navigated myriad market changes, boasting an impressive, ever-expanding portfolio of products. With over a century of industry expertise, the company is well positioned to deliver first-of-its-kind products and innovations across the globe, but particularly in Illinois, the state in which it is headquartered.
Although the company was initially based in Cleveland, Ohio, it moved to Rockford, Illinois, at the end of the 18th century and has remained there ever since. “Illinois not only has a solid industrial base but is a wonderful transportation hub for our domestic and overseas customers,” opens Dr. Jeffrey Ahrstrom, Ingersoll’s CEO.
“We’ve remained in Illinois, but we’ve been an international company since the beginning. In fact, our first export machine went to a customer in Hamburg, Germany in 1892. We then progressed through the 1900s, gradually expanding into composites, which then saw us develop head changing capabilities for some of our larger machines.”
Jeffrey continues: “In terms of myself, I started out in the business in 1985, shortly after I finished my enlistment in the US Marine Corps. It teaches you a lot of wonderful things, but I wasn’t sure to what industry my skill set would be best suited. That was until I had a great interview with a guy from a machine tool builder and joined as a trainee in field service.
“I continued my education alongside my career, completing an applications engineering management program, and I went on to run various departments and progress into general management. I then relocated and worked for a different company in my first high level role as President.
“However, I returned home a few years ago and had the incredible opportunity to work with international companies and be part of Ingersoll’s story as CEO,” he recalls. “I feel very lucky and blessed to genuinely enjoy my job and have the chance to work on some very cool, interesting projects.”
Turning to the company’s recent projects, Ingersoll has recently shipped the biggest hybrid 3D metal printing machine to the US Army. “Many companies are looking at ways to deploy 3D printing to enhance their operations,” Jeffrey elaborates. “The US Army has a huge parts storage plant, meaning that when a vehicle is damaged, the US site must ship the parts to the relevant geographic location.
Cutting-edge capabilities
“We recognized that the army could be much more mobile by harnessing the power of 3D printing, as it would enable them to make parts almost on demand, as well as freeing up the storage space and associated expenditure. So, we started thinking about a way we could ship a manufacturing system capable of that.
“We began working on a hybrid 3D metal printing machine, which is eight and a half meters wide, 20 meters long, and eight meters tall. The army went on to purchase this machine as well as a smaller printer with the capability to print items up to one cubic meter.
“Instead of going through the traditional procurement cycle, the army can now complete the same process internally in just a matter of weeks,” he explains. “It’s amazing to work with the army and help them on the journey to becoming more agile and efficient.”
Ingersoll is also currently constructing the world’s biggest telescope; a project that we are certainly keen to hear more about. “Well, the first question people often ask me is what on earth is a machine tool company doing building a telescope,” says Jeffrey. “But really, it’s nothing more than a huge machine-filled structure that needs to be incredibly rigid and structurally strong, both dynamically and statically. It also must be able to rotate accurately and repeat to microns of accuracy.
“We were approached for this project because we had contacts in the industry, as we built a similar telescope for a solar observatory around ten years ago. These jobs often require long, almost generational contracts, but we were able to leverage our previous experience of building large hydrostatic structures with our world class machine tool experience to secure the contract.
“Our experience with machining huge structures means we have in-house capabilities to design and test, then machine and assemble the telescope, before testing the internal machine tools. It’s a very bespoke structure; we currently have a 16-foot-deep hole in the floor of our plant because the telescope will be nearly as tall as the space shuttle and have a bearing diameter of 52 feet.”
Award-winning concepts
Jeffrey adds: “We wouldn’t be able to complete projects without the support of our trusted suppliers and vendors. The secret to building a longstanding relationship like we have with DTI and Siemens, for instance, is trust and transparency. Developing a partnership is about respecting and engaging with people and sharing your goals to find ways of achieving them together.”
Additionally, the business printed a concept for the Rosenberg Space Habitat (Rosenberg), which was awarded the title of Illinois’ ‘Coolest Thing.’ Jeffrey comments: “Illinois hosts an annual contest to find the coolest product produced by the state’s 16,000 manufacturers. We usually take part every year and end up somewhere in the top five products, but we were delighted that our concept for Rosenberg won this year!
“It was a challenging project, as Rosenberg wanted to demonstrate what life would be like to live and work on the moon. However, it was a particularly interesting and exciting project to work on and one that we’re immensely proud of, especially as it gets the next generation of manufacturers excited about our work.”
As our conversation draws to a close, Jeffrey concludes: “I’d like to see 3D printing and additive manufacturing become mainstream activity over the next five years. There’s constantly new materials and developments, so as other innovative processes emerge, the industry will one day think of 3D printing as nothing different to milling, drilling, or grinding.”