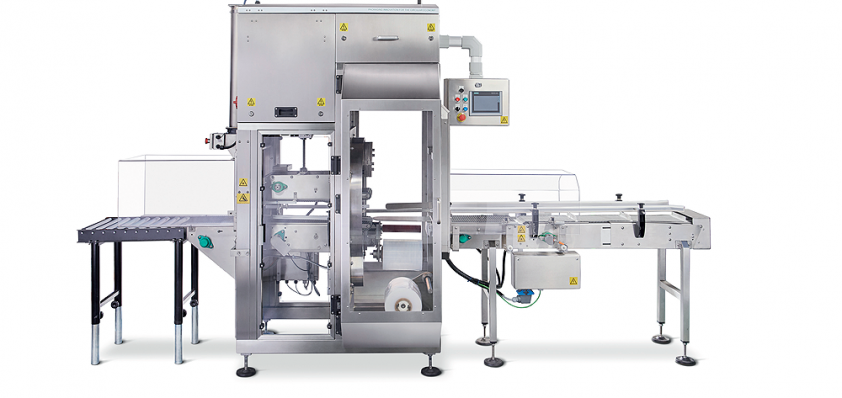
Innovative approaches
Plastic packaging is a vital part of the manufacturing supply chain – especially in the food and drink sector. As well as keeping products protected during transit, plastic prevents them from spilling, leaking or becoming contaminated, keeping them fresh for longer and reducing food waste. However, there’s no denying that when irresponsibly disposed of, plastic packaging can cause enormous damage in the natural environment – as highlighted by the BBC’s Blue Planet II programme – and this is driving the perception that all plastic packaging is bad.
With manufacturers under consistent pressure to improve their eco credentials, reduce waste and their carbon footprint, all whilst improving efficiency and reducing costs, is removing plastic from their packaging the way forward?
It is not. Global warming is the biggest issue facing the planet today and CO2e emissions are accelerating it, so the time has come to acknowledge the carbon footprints of different types of packaging.
Many manufacturers are unaware that plastic has the lowest carbon footprint of all packaging materials, emitting far fewer greenhouse gases than paper or cardboard, even though these are frequently TrakRapheralded as being more environmentally friendly options because they are biodegradable. Despite being biodegradable, corrugated cardboard actually has a far larger carbon footprint than plastic due to the enormous amounts of energy required to create it and because it releases its stored carbon back into the atmosphere when it decomposes.
Similarly, paper carrier bags have largely replaced plastic bags. However, paper bags have carbon footprints more than four times higher than their plastic equivalents, meaning any manufacturer using paper-based packaging in large quantities is increasing their carbon footprint at a time when carbon reduction targets are more important than ever. This is a particularly important issue for consumers, who increasingly refuse to spend money with any company that isn’t doing everything possible to reduce its carbon footprint all the way along its supply chain.
It is widely believed that getting rid of plastic packaging is a good idea, but how long will it be before manufacturers realise that the alternatives are more harmful to the environment than keeping it?
In a developed economy like ours, manufacturers need to adopt a new approach to packaging – one that allows them to utilise the low carbon benefits of plastic while also embracing the principles of the circular economy to massively increase recycling rates and prevent plastic getting into the natural environment. But with many caving to public pressure and announcing plans to eliminate plastic from their operations, how can packaging companies help make this happen?
First, they need to recognise that not all plastics are born equal. There are ‘good plastics’ – like PET and LDPE – which can be recycled many times over, and ‘bad plastics’ – like black plastic, PVC, PLA and polystyrene – which cannot. Although some companies are aware of this, the packaging industry needs to make these plastics easier to identify by using a simple colour coding system on their packs.
Next, manufacturers need to embrace the principles of the circular economy. PET and LDPE can be recycled back into themselves many times over and LDPE can also be turned into harder plastics that have long-term use. These are valuable commodities with an established value chain and justify local authority investment to enable them to be separated and returned to source for recycling.
Finally, it must become easier for consumers to make informed choices. By printing the carbon footprint of the packaging on the pack, attitudes to plastic will change. Consumers want to protect the planet so it must become easier for them to identify ‘good plastics’ and get them back to manufacturers for reuse.
Today, eco-innovations are available that use ‘cold wrap’ technology to replace traditional secondary packaging systems, which are used to safely package items for transit. These systems use an ultra-thin, 100 per cent recyclable LLDPE stretch film to wrap products, completely eliminating the use of heat from the packaging process. Compared to shrink wrap systems, cold wrapping reduces plastic usage by as much as 70 per cent, energy usage by as much as 90 per cent and carbon footprints by as much as 70 per cent, while innovative pack designs can also reduce cardboard usage by as much as 40 per cent. In addition, the film can be colour coded making it easier to collect and return to the supplier in a closed loop system.
Manufacturers should embrace these innovations as a matter of urgency to help them meet their carbon reduction targets and allow them to take responsibility for the packaging they send out via a closed loop system. And because these systems use less of everything, they also cost less, typically reducing end of line packaging costs by between ten per cent and 20 per cent.
The idea of banning plastic packaging is both unhelpful and impossible. Instead, manufacturers should turn to eco-innovation, try to use less of everything and, when it comes to plastic, ensure they use the right type – that which is recyclable and can be contained in a closed loop system.
Martin Leeming
Martin Leeming is CEO of TrakRap. Low-carbon secondary packaging company TrakRap designs and produces sustainable packaging solutions for manufacturers in the Fast-Moving Consumer Goods (FMCG) sector that supply supermarkets and retailers.
TrakRap’s packaging solutions are created using revolutionary cold wrap technology – an environmentally friendly, cost effective alternative to the traditional shrink-wrapping process that uses 100 per cent recyclable, ultra-thin stretch film to stretch wrap products.
http://trakrap.com/