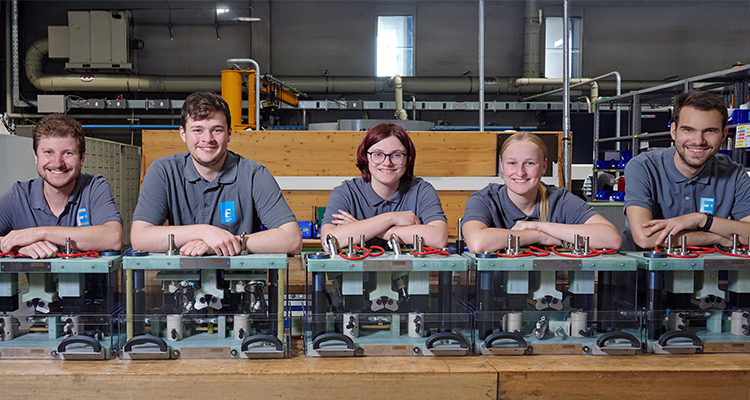
Inside Extrude Hone’s fast, global, and surprisingly green machining technologies
In sectors such as aerospace, automotive, energy, and medical, precision is paramount as the finishing process of machined components directly determines end-product performance. As an industry leader, Extrude Hone delivers advanced machining solutions that achieve unparalleled finished product profiles, completing these critical processes in significantly less time than conventional methods. In fact, the company’s line of technology stands apart by precisely shaping and perfecting even microscopic surfaces to deliver measurable performance enhancements. Bruno Boutantin, Market & Business Development Director introduces us to the various facets of Extrude Hone’s operations.
“At Extrude Hone, we operate across three core areas. One focuses on machine equipment design, manufacturing systems, and tooling production. Another is dedicated to contract services, where we operate contract shops worldwide to handle client components. Essentially, customers send us their parts, we complete the precision work, and we return the finished products to them. The final area encompasses our aftermarket and service operations. The foundation of our services lies in our advanced technologies, beginning with Electrochemical Machining (ECM), which encompasses both ECM static and ECM Dynamic systems. Dynamic ECM is an enhanced ECM system with additional axes to tackle more demanding manufacturing challenges, just like our ECM rifling capability, which has become a popular solution. Complementing this is our Abrasive Flow Machining (AFM) technology and its variation, Microflow, engineered for precision flow tuning using very low viscosity, nearly liquid, media. Moreover, we provide thermal deburring, a pure thermal removal process where parts are placed in a chamber to eliminate and vaporize the burrs through the combustion of gas mixtures,” he begins.
Manufacturing flexibility
Highly specialized and in demand, these services are delivered all across the globe thanks to Extrude Hone’s extensive global footprint. “While we are an American company, we maintain an extensive international presence through our various Centers of Manufacturing Excellence. In Irwin, Pennsylvania, our facilities specialize in AFM and Microflow while also serving as our headquarters. We also have a footprint in Germany, where our Center of Excellence for ECM is based, as well as a manufacturing hub for Asia based in Shanghai, China. Our contract shops can be found in several places around the world, namely in the US, UK, India, and Japan. For regions where we do not have a direct sales presence, we rely on our network of distributors, primarily agents, to ensure coverage across key markets like Asia and South America,” Bruno continues.
Through this widespread global presence, Extrude Hone is empowered to manufacture its products on a larger scale. Its implementation of Smart Factory technologies across its plants makes the company’s operations even more efficient. “On the manufacturing front, we are implementing significant changes, starting with our German operations, where we maintain rigorous standards despite operating under tight constraints. To reduce costs, we focus on boosting our efficiency and leveraging global sourcing strategies. Given that we are a small company producing only a dozen units of each model, we cannot always apply standard manufacturing principles. Instead, we prioritize manufacturing flexibility. Our goal is to combine this flexibility with a global sourcing and manufacturing platform to build any type of machine across all three continents in which we operate. This is further facilitated through the combination of our sourcing network, common capabilities, and sharing of best practice knowledge.
Green priorities 
“Most of our machines are Industry 4.0-ready, equipped with advanced data management capabilities. As a result, they can seamlessly exchange information with customers, providing real-time insights into manufacturing processes, predictive maintenance needs, and downtime prevention; all key tools for optimizing operational performance. Furthermore, unlike traditional models that centralize production in one region before shipping to a different part of the world, our distributed manufacturing reduces environmental impact from shipping while maintaining quality through smart manufacturing technologies,” Bruno explains.
This widespread manufacturing and sourcing footprint plays a vital role in Extrude Hone’s sustainability strategy. Bruno goes on to discuss the company’s initiatives to minimize its environmental impact. “Ten years ago, we moved our German operations to a plant that was specifically designed to be green. As I mentioned, we prioritize global sourcing, an approach that makes environmental sense too. We always source locally whenever possible, but when materials are not available nearby, we have no choice but to look elsewhere. At our manufacturing Center of Excellences, we collaborate with companies near us to minimize transportation costs and their associated environmental impact. We focus on sourcing solutions that contribute to reducing the energy impact, such as less electricity-consuming devices, like pumps and exhaust blowers. By doing so, we not only reduce electricity consumption but also noise. Sustainability remains our top priority, though we sometimes face difficult choices when price pressures conflict with eco-friendly options. For instance, when local sourcing is not feasible and we must import materials, we acknowledge it is not ideal environmentally, but often unavoidable. This balance between cost and sustainability requires constant discussion as we assess each customer’s willingness to pay more for greener solutions. Overall, this approach is working well, and we are committed to managing these challenges responsibly,” he ends.
By merging precision engineering with sustainable global operations, Extrude Hone doesn’t just meet industry standards, it redefines what is possible in advanced manufacturing.