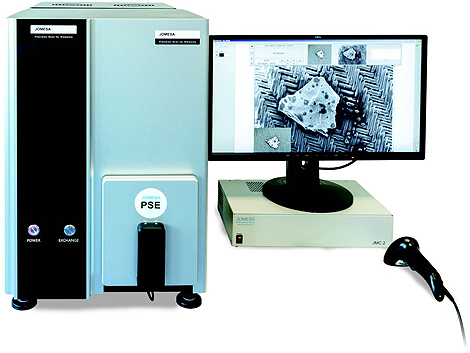
JOMESA North America
Seeing is believing
Seasoned readers of Manufacturing Today may well recall that it was back in 2018 that this publication last documented the activities of JOMESA North America. That particular piece covered much of the history and background of the North America operation of JOMESA – a Munich-based company offering microscopic filter analysis systems since the mid-1980s – as well as its rise to becoming a world leader in its field through the creation of a system that could take detailed images of filter membranes and measure contamination.
Today, JOMESA’s main product portfolio consists of optical and electron microscope systems for filter analysis (specializing in cleanliness analysis and oil cleanliness analysis), filter-mounts and filter-archiving accessories, laser-cut mesh filters, and image analysis software. However, when reconnecting with Product Management Director Peter Feamster in January 2021, the topic he wishes to discuss centers on a new solution that the business has been developing in the last several years.
That solution is the JOMESA PSE material analysis system, a desktop size SEM/EDX system that integrates with the JOMESA HFD Automated Cleanliness Analysis System, and which represents an entirely new approach to performing material analysis on particles extracted during cleanliness testing. Sharing a local network connection, the JOMESA HFD system performs the optical counting and measurement of contamination particles while allowing the operator to identify interesting particles to be further analyzed for material composition. The filter sample is then loaded into the PSE system for material analysis directly on the particles identified. This synergy between optical and SEM technology greatly reduces wait times normally associated with SEM/EDX analysis for cleanliness testing as the particles in question are directly analyzed, thus a full scan of the filter membrane is not necessary.
“Since 2017, we have made a determined effort to integrate SEM technology with our optical microscope systems,” Peter explains. “Filter membranes have long been inherently challenging for SEM systems, due to several factors including the membrane not being a conductor of electricity, which makes the process of analyzing contamination all the more difficult. At the same time, our customers are increasingly needing a lot more information to really develop root cause analysis and to answer their contamination questions more fully.
“Our clients have found that the standard method for detecting contamination particles is insufficient for certain highly damaging materials; by incorporating the optical analysis data with our PSE system – in a way that has not been seen anywhere else in our industry – our clients can detect a wider range of particles on the filter membrane in a much more practical, efficient and detailed way than ever before.”
The data sharing capabilities of the PSE system means that data captured by the optical microscope – including where particles are on the membrane, their size and their shape – is fed back to the SEM, which then scans them to identify their material composition. “Historically, to do this, operators would have to physically try and tweezer small particles – most less than 100 microns in length – from a filter membrane onto another substrate that would be more easily scanned by an SEM, which as you can imagine is a really cumbersome endeavor,” Peter details. “What our system does is it allows you to travel directly to these particles, saving a lot of time and manual effort.
“In addition, the preparation of the filter that we have developed is much more effective when analyzed within the SEM. Where previously, analysis of the filter itself which tends to be a nylon or polyester substrate – would often result in distorted images or in particles becoming ejected due to static build up, what we have done is come up with a liquid solution that we call a ‘fixation’ solution. This is applicable beneath the filter membrane and it adheres the particles to the filter itself, preventing jumping. We have also devised a conductivity solution, which is applied to the top of the filter to create something of an ionic film, allowing electrons to discharge and ground off of the filter. This gives you really crisp, clear images of the particles themselves.”
Response from customers to the company’s PSE system has been universally positive, with particularly strong interest being shown from those active in the automotive and lithium-ion battery industries. “Getting the PSE system to market was an incredible undertaking, however, now our work involves refining it – and our other solutions – to meet our customers’ needs and their respective feedback,” Peter continues. “2021 is going to be an important year in terms of how we make improvements across all manner of things, for instance we have some filter handling products that we are currently working on that we believe will make the handling of membranes themselves far easier. We also have some new technology in development for improving particle detection and increasing the speed of our scanning capabilities.”
JOMESA’s development of its PSE material analysis system is just the latest example of the company’s dedication to being at the cutting edge of cleanliness analysis. “We have always, and will always, want to be innovators within our industry. To do so, it means bringing to life cutting edge technology such as our PSE system so that we can not only answer the questions that our customers have today, but also potentially solve those that they simply haven’t come up with yet,” Peter concludes.
JOMESA North America
Products: Microscopic filter analysis systems
www.jomesa.com