Key areas of focus for manufacturers in 2025.
Being ‘fit for 2025’ for manufacturers means being in the best possible position to respond to change while not being thrown off course… whether by wars, disease, weather, governments’ policies, technological development or whatever 2025 and beyond will throw at us.
By now all business leaders realize that volatility is a constant and no longer a surprise. Whilst the eventual causes in 2025 might be uncertain, it is time to focus on a business model that delivers truly integrated outcomes and is focused on people, process and technology to achieve growth and profitability.
As we move into 2025, it gives the opportunity for leaders to reflect on getting their business in the best possible position to identify and respond to changes. To achieve this, key areas of focus for manufacturing businesses need to be:
Flexibility
In recent years people have had to learn a lot about how to deal with volatility. But in many cases the processes that were successfully developed, often through trial and error, will be quickly forgotten… and with the next crisis people will be back to improvising. Instead, there needs to be a process for such situations so the lessons from the recent past are not only captured and reapplied, but also formalized and improved.
In 2025 make sure you have embedded the lessons from overcoming the recent problems and add systems and processes so that when volatility hits again you don’t revert to firefighting and making on-the-hoof decisions about tactical planning, and realigning portfolio demand with the supply chain. Not just in operations, but across all support functions too.
Agility
Flexibility and agility both are overused words, and often without much substance given both are organizational capabilities achieved through process.
Flexibility is about dealing with short-term changes, particularly through flexing people and equipment capacity. It’s vital to have this, but it is not the same as
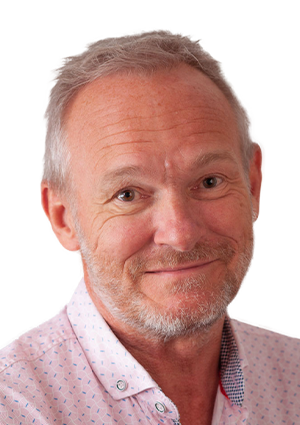
having the ability to quickly move the whole organization according to a plan.
Business agility (as opposed to firefighting and flexibility) is having an organization that can, as a whole, respond to change. It’s not just the supply chain, but the whole organization’s capability (commercial, finance, etcetera) to deliver a planned response from the rapid identification of opportunities and threats.
Where your organization has been thrown off-track by firefighting crises (as many have been every year this decade!) it is not about congratulating your team on successfully handling yet another unforeseen problem. It instead should be seen as an opportunity to understand the root causes for such problems and remove them in 2025.
Instead of rushing from one reorganization to the next, manufacturing leaders’ priority needs to be ensuring their business is structured so change can be implemented quickly and throughout the business on an ongoing basis.
An agile capability is key as we can’t know everything that will hit us in 2025. But the rigor of creating properly worked-through plans ensures you are in the best place to respond whatever the challenge. The very best way to have this capability comes through having scenarios and worked-through plans for responding to the most likely eventualities – worked through by all involved, not just a small team in isolation.
Timely information
Manufacturing businesses are now typically managed with a suite of sophisticated best-of-breed applications, most of which only talk to each other with a great deal of effort and cost.
Technology that actually integrates in 2025 needs to become a reality and not just words that are used endlessly by technology and implementation partners.
In 2006 Marconi PLC, a pillar of British advanced manufacturing, collapsed – ultimately because senior management were oblivious to the collapse in demand for core products until it was too late. No manufacturer should suffer this fate today with the business information the technology it deploys should deliver, yet many still make decisions based on out-of-date data because the most recent data is not readily available to senior and middle management! Common examples are financial systems not integrating with planning volumes, and portfolio information not integrating across to demand generation and plans.
In running your manufacturing business, you really should be able to integrate the total enterprise from strategy to detailed execution, whilst ensuring the necessary integrated views of data to allow you and your teams to optimize the enterprise and rapidly identify when the business might be off-plan.
The essential agility and insight to navigate 2025 and beyond’s exigencies will always remain elusive to any manufacturer that has not successfully integrated its various platforms to deliver a genuine enterprise model, rather than the current all-too-common position of trying to manage through a network of unintegrated spreadsheets, data silos and Power BI reports that deliver information that is already out-of-date the moment the Management Information report arrives.
In the world of ‘Big Data’, AI and machine learning, surely 2025 is the time to focus on the ‘so what’ of your technology systems, and how all of this can drive superior business outcomes.
By Les Brookes
Les Brookes is a partner at business transformation consultants Oliver Wight EAME. Oliver Wight is a world leader in IBP consulting (Integrated Business Planning). With a focus on transferring knowledge to clients through coaching, mentoring, and workshops, the organization’s approach differs from other consultancy firms.